Latest News
October 10, 2013
Last week, when James Scapa, chairman and CEO of Altair Engineering, faced the users assembled in the ballroom at the Hyatt Regency in Orange County for the annual user conference (Altair Technology Conference, Garden Grove, California, October 1-3), he said “[It’s time to] take a blank sheet of paper and rethink how you’re going to design things in the future.”
Later, this sentiment was echoed by Robert McIntosh, Boeing’s chief engineer for weight engineering, another keynote speaker. McIntosh said, “You need to cut off your thumbs because historical rule of thumbs won’t apply.”
McIntosh was talking about weight optimization, a discipline that Altair has made its specialty over the years. “Doing the same thing we’ve been doing for years wasn’t good enough,” said McIntosh. “Topology-based optimization is significantly different from traditional design.”
But the rule of thumb for how people prefer to acquire and use engineering technology may also be heading for a drastic change: “Cloud is driving the enterprise solution and new business models,” acknowledged Scapa.
For better or worse, the iPhone’s app-driven model has spawned a whole new generation of software users with a different attitude. (In my view, it has even retained many who grew up in the pre-iPhone era.) The new technology consumers prefer their software—and, when possible, even hardware—to be as easily and instantly available as mobile apps. Like customized RSS feeds from their preferred regions and outlets, they want a drive-train simulation or a ship-hull optimization solution instead of a general FEA package they need to shoehorn into their existing practices and workflows.
That turns the traditional perpetual software licensing model on its head. It also jeopardizes vendors who rely on all-inclusive packages that give users more than they need: more function, more tools, and far more complexity than what’s possible to master in a reasonable time.
The Era of “What you need, when you need it” has prompted many tech companies to rethink or refine their strategy. PTC’s rebranding of the all-inclusive Pro/E as modular Creo pieces is one example. Autodesk’s swift shift to cloud-hosted and cloud-augmented products is another. Siemens’ move to industry-specific solutions and subscription model on some titles, and a industry-focused approach taken by Dassault Systemes may also be prompted by the same trends.
Perhaps the most significant product from Altair to address the changing consumer behavior is the launch of a three-pronged HyperWorks product line:
- HyperWorks Unlimited
- HyperWorks On-Demand
- Simulation Cloud Suite
The HyperWorks Units works like common tokens within the HyperWorks Partner Alliance, encompassing not just Altair products but those from third-party vendors who belong to the alliance. What makes this alliance particularly appealing to project-based users with short-term needs is the recycleable nature of the units (you may take out a set number of tokens from the pool that belongs to you to gain access to one product; when the job is complete, you may shut down that product and use the same set of tokens to access another product).
If your in-house clusters, workstations, or IT resources prove insufficient to tackle your simulation jobs, Altair’s HyperWorks On-Demand could be the reinforcement you call on. It’s described as “a public cloud solution,” but in terms more familiar to the on-demand industry, it may be called Platform as a Service (PaaS) or Infrastructure as a Service (IaaS). The offering gives you access to Altair’s data center to process simulation jobs.
The Simulation Cloud Suite gives you a way to manage big simulation data (almost unavoidable these days) from a web interface. It’s simulation lifecycle management (SLM) delivered as Software as a Service (SaaS). With this, you can, for example, collaborate with others on shared simulation jobs and view the results online without downloading gigabytes of data to local computers.
The Altair user gathering also marked the launch of Virtual Wind Tunnel, built on the CFD technology from ACUSIM (a Mountain View-based company Altair acquired in January 2011). Comparison with Autodesk’s Project Falcon is inevitable.
James Dagg, Altair’s senior VP of software development, clarified that the product is aimed at professionals, not a lightweight product for enthusiasts and prosumers. It will first appear as a feature in the HyperWorks product line. In the announcement, Altair says the product boasts “a fast, fully-automated unstructured mesher with boundary layers. Volume meshing for an external automotive aerodynamics analysis—including the underbody, underhood compartment and boundary layers—can be completed in less than two hours.” (Altair plans to host a webinar on the product on Oct 17. To sign up, go here.)
In his onstage demonstration, Dagg also showed the early works Altair is doing to refine and update the user interface of one of its classic product: HyperMesh. It’s a product with a huge loyal fan base, so the changes have to be delicately handled.
“We have always been careful not to pull the rugs out from you because we know you have built muscle memories,” said Dagg. “But we really do need to move forward. The good news, when it’s done, your muscles will have less to remember later.” These interface changes are set to roll out incrementally over the next three years, he clarified.
In recognition of the increased importance of 3D-printing, Altair is preparing a topology optimization tool specifically developed to optimize geometry for 3D printing. It’ll appear as part of Altair’s OptiStruct product sometime in the next year. The company hopes it will help 3D printing service users to analyze and built 3D-printable parts with optimized support structures (a basic strategy to reduce material usage in the process).
As he wraps up his keynote, Scapa uttered what might be Altair’s operating principle: “The quest for simulation is to lead design, not just to verify.”
The emergence of on-demand solutions with the option to switch from one title to another as the project demands may encourage more engineers to use simulation as a driving force, not a verification method.
Subscribe to our FREE magazine,
FREE email newsletters or both!Latest News
About the Author

Kenneth Wong is Digital Engineering’s resident blogger and senior editor. Email him at [email protected] or share your thoughts on this article at digitaleng.news/facebook.
Follow DERelated Topics
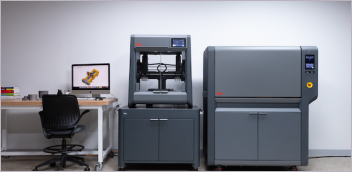
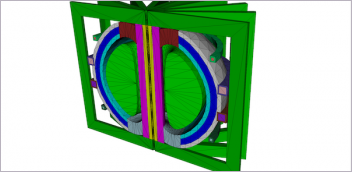
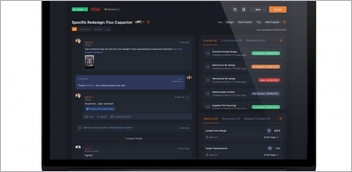
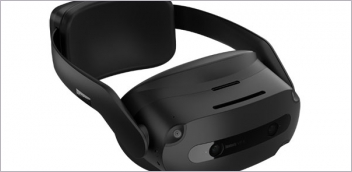