Latest News
November 1, 2011
By John Edwards
Like other mobile device antenna developers, Dr. Jennifer Bernhard, a professor of electrical and computer engineering at the University of Illinois at Urbana-Champaign, faced a fundamental dilemma: how to shrink an antenna’s physical size without sacrificing major amounts of gain, efficiency or bandwidth.
“Most of the time, when you make an antenna small, you make a bad antenna,” she says.
Bernhard’s solution was to think flexibly and to use a 3D printing technique to create antennas that fit around a tiny, space-saving hemispherical substrate. Bernhard notes that antennas created with the process are electrically small in relation to the wavelength—usually one-twelfth of a wavelength or less—and feature performance metrics that are an order of magnitude better than those provided by conventional monopole antenna designs.
“It’s a great solution to a significant problem,” she says.
Addressing the Problem
With mobile devices evolving into ever-smaller form factors (SFFs), antenna developers are investigating a growing array of innovative design concepts. They’re tapping into 3D printing, exotic materials, fresh fabrication techniques and other innovations that promise to give designers additional choices when specifying antennas for smartphones, tablets and other mobile devices.
University of Illinois printed antenna.
Yet as researchers push antenna concepts far beyond existing parameters, they’re also confronting long-standing radio frequency (RF)-related design challenges, including the big one: size and shape versus performance.
“The basic job of any antenna is to efficiently send energy into free space,” says Dr. Richard Ziolkowski, a professor of electrical and computer engineering and optical sciences at the University of Arizona in Tucson, who is working on his own cutting-edge mobile antenna research. “Yet, with antennas that are tiny compared to the wavelength, most of the signal is simply bounced back to its source.”
Overcoming this basic obstacle is fundamental to the work of all researchers exploring new antenna design concepts.
“The goal, of course, is to make the antenna as efficient as possible within the space allowed,” says Bernhard. “That’s the essential thing.”
3D Printing
Bernhard says that she and her team believe 3D printing can allow small antennas to radiate signals effectively, while minimizing the ratio of energy stored to the energy radiated—the “Q” of an electrically small antenna.
“Printing directly on that hemispherical substrate gives us a highly versatile, single-mode antenna with a Q that very closely approaches the fundamental limit dictated by physics, the Chu limit,” she explains.
Building the antenna is relatively simple. Pyrex hemisphere substrates are printed with a conductive ink. Conformal printing can create the meander line antenna on the inside or outside of the substrate for flexibility. Bernhard notes that the approach can be used for an antenna integrated into a mobile device, the inside of a carrying case, or even the wing of an unmanned aerial vehicle. The antenna’s operating frequency is determined by the printed conductor cross, as well as the spacing between the meander lines.
Bernhard says that engineers using software design tools to test and evaluate tiny antennas inside SFF platforms actually have an advantage over colleagues working with larger antennas and platforms.
“Once the platforms get larger, there are fewer software products that can do a good job of accurately predicting what the effect of an antenna would be on a larger package, such as an airplane,” she says. “Those simulations are complicated, and can take a long time to run.”
Metamaterials
Another approach to creating tiny antennas is to build them out of materials that have properties capable of boosting device efficiency despite size and shape constraints. To this end, National Institute of Standards and Technology (NIST) engineers are collaborating with colleagues at the University of Arizona and Boeing to create antennas incorporating metamaterials—materials featuring microscopic structures offering unusual properties.
A metamaterial can make an antenna behave as if it were much larger than it really is, Ziolkowski says: “The antenna structure stores energy and then re-radiates it.” The approach eliminates the need to add bulky matching network components to increase efficiency. Better yet, Ziolkowski notes, metamaterials are more “frequency agile,” allowing designers to use them on virtually any frequency on the fly.
Metamaterial antennas can radiate as much as 95% of an input signal, while defying conventional design parameters, Ziolkowski says. He notes that the prototype metamaterial antennas are as small as one-fiftieth of a wavelength—and could shrink further.
Ziolkowski says his challenges in developing metamaterial antennas were similar to those faced by antenna researchers investigating other technologies and processes.
“Even with metamaterials, the tradeoffs are always among small size, large bandwidth, high directivity and efficiency,” he says. “You’re still fighting to get the best results in all of these areas simultaneously and, because of fundamental physics, it remains a challenge.”
Ziolkowski says that his research team uses ANSYS HFSS, a 3D full-wave electromagnetic field simulation tool, to analyze and tweak their antennas’ performance characteristics. He notes that they use the software as a frequency structure simulator to evaluate antenna performance across the spectrum.
Selecting the appropriate antenna design and analysis software, Ziolkowski says, is mostly a matter of personal preference and taking the time to choose a tool with features that are appropriate to the work at hand. He notes that designers have a wide range of software packages from which to choose, including CST Microwave Studio, COMSOL Multiphysics, GEMS and XFdtd, to name a few.
While software vendors take different approaches to antenna design and analysis tasks, Ziolkowski notes that virtually all of the available tools can help designers reach their intended goals.
“All of these software packages look at the performance of the electromagnetic wave and how the antenna is active, coupled with other systems,” he says. “With HFSS, for example, you actually incorporate circuit behaviors and portions of the antenna with the circuit itself—called co-design—so that you can actually do both the antenna and the circuit analysis together.”
Liquid Metal Fabrication
At North Carolina State University, researchers are investigating a new antenna fabrication technology that’s based on liquid metal injected into elastomeric microchannels. The wirelike antennas can be bent and contorted without snapping because the device’s mechanical properties are governed by the elastomer, not the metal.
“Flexibility is a great attribute to have in an antenna, since the antenna’s frequency is determined by its shape,” says Dr. Michael Dickey, assistant professor of chemical and biomolecular engineering at North Carolina State University. “You can actually tune these antennas just by stretching them.”
The antennas are created by injecting an alloy comprised of gallium and indium, which exists in liquid form at room temperature, into hollow channels about the width of a human hair. Once the alloy fills the channel, the alloy’s surface oxidizes, forming a “skin.” The skin holds the alloy in place, allowing it to retain its liquid properties.
“The alloy essentially remains a liquid,” Dickey says. “The alloy assumes the mechanical properties of the material encasing it.”
![]() | ![]() | ![]() |
University of Arizona metamaterial antennas. |
Dickey says a design and simulation tool, like CST Microwave Studio, could be used to integrate a wirelike antenna into a smartphone or similar device.
“From a design perspective, the engineer is looking at how informal an antenna can be for a consumer product,” he says.
Dickey notes that over the past few years, aesthetic design has become a major consideration in mobile device development—almost a top priority.
“Manufacturers and consumers certainly don’t want something like an antenna sticking out of their box,” he says. “That’s where having good software, and an antenna formed with liquid metal inside a plastic, can be an advantage.”
Eliminating Antennas
At the U.S. government’s Oak Ridge National Laboratory in Tennessee, researchers are investigating the possibility of doing away with antennas entirely—at least antennas in the conventional sense of the term. Instead of a conventional metal or dipole antenna, future mobile devices might incorporate an antenna no bigger than a gnat.
Such an antenna might be made possible by a design that allows an electrically charged nano-mechanical oscillator to be tuned to specific electromagnetic waves. The technology detects small electric fields over large frequency ranges while maintaining power efficiency, making it potentially useful in a wide range of mobile communication devices.
“Having to match the antenna length to the wavelength may no longer be necessary,” says Dr. Panos Datskos, the technology’s co-developer and the lab’s nanosystems and structures group leader.
Datskos says that modeling and simulation software played a major role in helping his team develop the technology, as well as measure results. The team chose COMSOL Multiphysics, although a variety of other products could have also been used.
“It has magnetic modules, and that’s what we used to simulate the electrical distribution, the magnetic interactions—where the charges should be—and to create a more sensitive antenna,” he explains.
The Future
Bernhard notes that innovative antennas, combined with effective design tools, provide a potent one-two punch that will help designers cope with growing pressures to develop smaller and more feature-packed smartphones and other radio-equipped devices. But she predicts that design know-how and talent will continue to be important factors in mobile device development for many more years.
“Technology alone won’t get you to an optimum design,” she observes. “Most tools, for instance, have some kind of optimizing function in them, but it’s important be able to set up the optimizer properly. It’s very easy to get answers that are incorrect due to the inexperience of the user.”
Ziolkowski agrees. “You start with the technology and the tools,” he says. “The rest is up to the designer.”
MORE INFO
ANSYS
CST
COMSOL
GEMS
Remcom
John Edwards is a technology writer based in Gilbert, AZ. His work has appeared in IEEE Signal Processing, Electronic Design and other publications. Contact him at [email protected].
Subscribe to our FREE magazine,
FREE email newsletters or both!Latest News
About the Author

DE’s editors contribute news and new product announcements to Digital Engineering.
Press releases may be sent to them via [email protected].
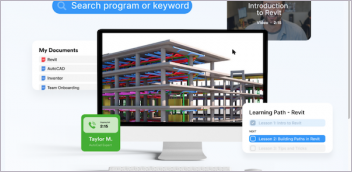

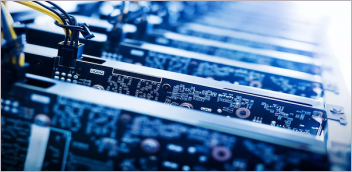
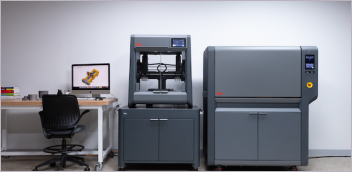