Clicking Parts Certification into the AM Puzzle
Validation and certification of 3D printed parts is getting easier as standards efforts mature and process monitoring capabilities take aim at consistent quality.

KREPE-1 (Kentucky Re-Entry Probe Experiment) space capsules intended for a NASA mission, features parts that will require certification if slated for end-use production. Image courtesy of Protolabs.
May 6, 2024
Parts certification and validation, foundational to any manufacturing process, is one of the last remaining pieces needed to click into place to drive additive manufacturing (AM) of end-use parts at scale.
Companies are increasingly looking to AM for end-use part production to gain efficiencies, enable on-demand output closer to the point of need, or to manufacture or lightweight a design not possible with conventional methods. Yet as the desire for production-grade AM builds for everything from replacement parts to jigs and fixtures, incomplete standards and immature processes make it difficult to validate and certify repeatable accuracy and quality of parts, especially for companies in highly regulated industries like aerospace, automotive and medical devices.
For companies to opt for AM over traditional manufacturing processes, the industry has to meet the extra burden of defining and implementing a robust qualification and validation process. The goal is to demonstrate production consistency along with an ability for AM parts to maintain their quality benchmarks over time.
“It’s a critical topic in our industry right now—a testament to the fact that AM processes are experiencing stability and moving from the typical short-term project into serious manufacturing,” says Cary Baur, senior manager of polymer technology for EOS, a maker of high-end metal and polymer AM systems. “We’re stepping into the ballgame of higher-level production and with that, we need to make qualification a more serious process.”
AM Raises Bar on Validation
AM is unique among manufacturing practices because its nature injects variability at each step, whether build methodology, postprocessing steps, or materials used across hardware original equipment manufacturers (OEMs) and potentially different parts printed on the very same system.
For example, Multi Jet Fusion (MJF) and Selective Laser Sintering (SLS) AM technologies create very similar material and mechanical part characteristics, but the manufacturing processes are completely different, requiring diverse controls to achieve repeatable quality, says Greg Paulsen, director of applications engineering and marketing at Xometry, an on-demand industrial parts marketplace.
In this case, one AM method commands a broad spectrum infrared heat lamp recoater arm while the other involves a computer-controlled focused laser. Other variabilities could be heat dissipation across the varying pack density of a build box, which can affect each part differently, he explains.
In contrast, the feedstock processing guidelines for most materials used in injection molding vary little between different OEMs and are readily available while flow simulation software can help validate processes before even getting a print job off the ground. Similarly, computer numeric control (CNC) milling systems are relatively consistent, with most subtracting material in the same manner, again, using certified bar stock.
That level of standardization is not the case with AM.
“Since we have a wide variety of AM build platforms, simulation of part manufacturing is difficult and expensive for most users,” Paulsen says.
Formal and well-understood standards have existed for decades governing parts validation for industries like aerospace, automotive and medical devices, including over 50 published by ISO/ASTM. Though the standards serve as an invaluable tool for companies trying to stand up an internal certification framework, many aren’t tuned to the unique characteristics of AM processes.
“The standards don’t change—it’s what has to be done to meet the standard that changes,” says EOS’ Baur. “At the end of the day, our customers are responsible for getting [Federal Aviation Administration (FAA)] or [U.S. Food & Drug Administration (FDA)] approval of a specific product. They have a strong understanding of the base requirement of products within those regulations, and our job is to help them translate that to get what’s needed out of the machine.”
Some requirements around certification and validation are a close fit, but not a great fit for AM, in part because of lack of data. AM is a fast-changing technology with no extensive databases yet available and no extensive and specific ISO standards or processes.
“There are certain levels of accepted information that’s been around for 70, maybe 80, years for traditional manufacturing and we just don’t have that longevity around on the AM side,” says Sherri Monroe, executive director at the Additive Manufacturer Green Trade Association (AMGTA), a global trade organization founded to promote the environmental benefits of AM. “We need more data to have more understanding.”
For its part in data development, AMGTA is working with partners to create standards for its AM Lifecycle Assessments; these in-depth analyses of data helps organizations evaluate the sustainable impact of different AM products and technologies.
The challenge is also more complex than validating a single part as sufficient, but rather to formalize consistent processes to effectively scale AM.
“It’s less about part certification and more about process validation and certification,” says Gert Brabants, business line manager, certified manufacturing, at Materialise. “The challenge we need to overcome is to prove AM can produce consistent quality parts with validated processes—the only way to build that trust is with data, data and more data.”
The CO-AM Quality & Process Control (QPC) system takes quality and process control to the next level, helping to certify part quality. Image courtesy of Materialise.
Talent is central to executing production-scale AM, and most companies are still lacking the requisite AM skills and expertise required to man production-grade operations. Finding team members experienced enough with AM to identify key characteristics that would support a proven qualification process is rare, and educating the next generation is slow.
“It’s a multidiscipline role from design to manufacturing to quality until AM becomes more industrialized,” Xometry’s Paulsen says.
Solving the Certification Problem
Given the momentum behind AM, companies are working on a variety of efforts to address the parts certification and validation challenge, including creating and sharing more robust data, working with standards bodies and developing technologies to boost process monitoring and quality controls.
International standards organization ASTM has created the Additive Manufacturing Quality (AMQ) certification designed to validate the capabilities of service providers and manufacturers in consistently producing high-quality parts in accordance with established international standards. Most service providers operate using their own internal standards, and OEMs typically qualify third-party partners with their standards so no generally accepted qualification program exists. The AMQ, based on published ISO/ASTM standards, helps build confidence and consistency.
“By availing AMQ certification, OEMs can focus on the functionality of the part rather than the way it is manufactured,” says Mohsen Seifi, vice president, global advanced manufacturing programs division at ASTM.
At Materialise, there is a big emphasis on developing their own standards for process control and building up a database of parameters and materials properties that can be actively shared with customers to build trust in production-grade AM. The company’s decades of work in the manufacture of end-use parts in the medical and aerospace industries has created a rich library of intellectual property about machine control and process monitoring, providing an advantage for traceability and certification of parts in these highly regulated sectors, Brabants says.
“Companies can’t look up the properties of an AM part like they can for an injection-molded one so we need to focus on generating and sharing this data to build trust, reliability and consistency,” Brabants says.
Another way Materialise helps advance AM parts validation and certification is through the Quality & Process Control (QPC) system, part of its CO-AM cloud-based platform designed to help organizations scale AM workflows. QPC takes AM quality and process control in certified manufacturing to the next level by allowing companies to track, monitor, analyze and correlate data critical to part quality. The software connects critical AM resources like 3D models, raw materials, process parameters, in-situ process monitoring, postprocessing and quality inspection data. With the addition of an artificial intelligence layer, it also delivers a holistic view of processes, identifies potential anomalies and ensures consistent quality of output.
“Getting feedback during the process enables more effective root cause analysis and improves processes,” Brabants says. “You’re not simply checking a part at the end of the process and throwing a bad part away.”
Aerospace manufacturers have been at the forefront of leveraging AM production parts, with most current aircraft featuring a smattering of AM produced parts, according to Foster Ferguson, Stratasys’ global director of aerospace.
Stratasys has been actively working to mature aerospace part qualification processes, including collaborating with the National Center for Advanced Materials Performance (NCAMP), under Federal Aviation Administration (FAA) and European Aviation Safety Agency oversight, to create a public domain database. The database would include standardized processes, machine calibration and operation specifications, and materials that can help parts meet FAA qualification standards.
“We’re trying to break down the barriers of entry for people in manufacturing because it’s challenging for someone to create their data set when they’re adopting a particular AM technology because there’s a lot of uncertainty in the process,” Ferguson says. Instead of qualifying entire material systems, manufacturers can pull a system from the independent NCAMP databases, prove equivalency and gain FAA certification much faster and at less cost than a traditional qualification approach, he says.
GrabCAD Pro’s Accuracy Center ensures repeatable, tight-tolerance production of 3D printed parts to aid in certification and validation. Image courtesy of Stratasys.
Stratasys is also coming at the validation and certification challenge through new software capabilities. For example, GrabCAD Print Pro’s Accuracy Center feature takes a scan of a printed part, aligns it to a design model and compares the two for an accuracy score that helps tighten up tolerances and meet the specifications required.
Protolabs, a digital manufacturing services provider, offers an a la carte approach to parts certification and validation, tailoring its offering based on customer needs, says Eric Utley, 3D printing applications engineering manager. For example, Protolabs can perform the due diligence to ensure parts meet rigorous AS9100 quality standards for the aerospace industry or simply work with customers to ensure part consistency from a visual standpoint.
“For less critical parts, companies are often just interested in consistency, ensuring a part looks the same as one they ordered three months ago,” Utley says. “With aerospace and metal parts, there are concerns about material strength and that the part doesn’t fail. There, we are locking in as many variables as possible to keep that output as consistent as possible.”
When using a service provider, Utley advises defining requirements in 3D models as loosely as possible for the applications because AM technologies are evolving so quickly. For example, instead of validating a part for a specific model printer, structure the requirements so it’s more about layer thickness or material composition.
“Specify printing on a laser powder bed fusion system in 30 micron layers instead of a specific printer model,” Utley says. “Getting the technology, laser thickness and material down gives you more freedom for manufacturing.”
More ASTM Coverage
More EOS Coverage
More Materialise Coverage
More Protolabs Coverage
Subscribe to our FREE magazine,
FREE email newsletters or both!About the Author

Beth Stackpole is a contributing editor to Digital Engineering. Send e-mail about this article to [email protected].
Follow DE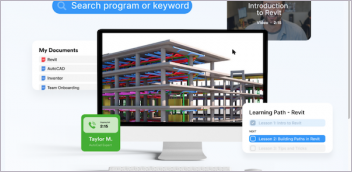

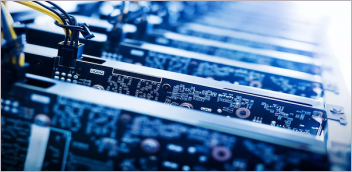
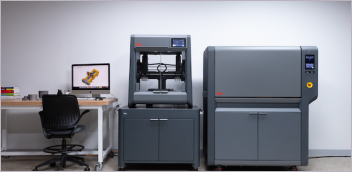