Latest News
May 20, 2009
By DE Editors
![]() Seen here are a pair of analyses in the mechanical simulation application that were launched from the new schematic concept in Workbench 2.0 project page. |
ANSYS, Inc. (Canonsburg, PA) has announced the availability of ANSYS 12.0, its engineering simulation platform and integrated technology for predicting how product designs will operate and how manufacturing processes will behave in real-world environments. ANSYS 12.0, according to the company, enables parametric studies and design optimization across multiple physics while facilitating the capture and reuse of simulation processes and data. The net effect, according to ANSYS, is that version 12.0 enables innovative products, lowers development and manufacturing costs, and accelerates time to market by compressing design and analysis cycles.
“Using virtual prototyping to reduce development costs and time to market is not a choice—it’s a requirement,” said Jim Cashman, president and CEO of ANSYS, Inc, in a press statement. “The pressures of global competition, complex customer requirements and shorter development schedules are forcing engineering organizations to rely on virtual prototyping to ‘get it right the first time’—and launch products with a higher probability of market success.”
![]() Simulation results for the flow inside a cylinder in an internal combustion engine. |
The ANSYS 12.0 software suite supports product design and validation in a virtual environment that captures complex and coupled physical phenomena. The key to ANSYS 12.0 is the ANSYS Workbench 2.0 platform, a simulation environment that, the company says, “is the glue” that allows engineers to set up, visualize, and manage simulations easily as well as capture and automate repeatable processes. It is from within the Workbench environment that engineers investigate multiple what-if scenarios, optimize designs across multiple physical phenomena, and design for six sigma.
The Workbench 2.0 project page has been expanded with the introduction of a project schematic concept. Project schematics enable engineers to build complex, multiple physics analyses by connecting systems. It indicates data dependencies as connections, and state icons indicate whether cells are up to date, require user input, or need to be updated. Engineering Data and ANSYS DesignXplorer, formerly independent applications, have now been integrated within the ANSYS Workbench project window.
The ANSYS FLUENT fluid flow solver has also been introduced into the ANSYS Workbench platform. This functionality means that CFD (computational fluid dynamics) practitioners can now leverage a parametric and persistent modeling environment and gain access to key enabling technologies such as bidirectional CAD integration, advanced meshing and powerful post-processing.
![]() This sequence of ANSYS 12.0 images simulates the motion of a screw pump solved using immersed solid fluid structure interaction. |
Geometry interfaces have been enhanced in ANSYS 12.0 to import more information from CAD systems. Enhancements range from new data types such as line bodies for modeling beams to better support for named selections created within the CAD systems. For preprocessing larger models, release 12.0 offers 64-bit operating system support and selective updates of CAD parts. Additionally, geometry modeling in the ANSYS Workbench environment is said to provide increased automation, greater flexibility, and improved ease of use when preparing geometry for analysis. Merge, connect, and project features have been added for improved surface modeling.
The ANSYS 12.0 suite offers a range of technologies for exploring dynamic behavior, including frequency response and large overall motion of nonlinear, flexible multibody systems. The suite’s solver portfolio includes functionality for structural mechanics, explicit dynamics, fluid dynamics, thermal analysis, and electromagnetics. The connectivity of individual ANSYS 12.0 capabilities to one another enables multiphysics simulations of compound physical effects for analyzing and assessing product performance in the real world. Coupled physics simulations with ANSYS 12.0 technology are set up and managed with drag-and-drop ease.
![]() This ANSYS 12.0 image depicts the high-velocity impact of a steel ball on a brittle ceramic target enclosed in a steel ring. The contour plot highlights regions damaged and cracked. |
ANSYS 12.0 also allows engineering team members to collaborate on product design and development. Within a single project, several engineers can assess their designs within individual disciplines or coordinate multiphysics simulations. To manage the workflow of a group of engineers and their projects, the ANSYS Engineering Knowledge Manager (EKM) provides process and data management tools for archiving, searching, retrieving, and reporting simulation data. With release 12.0, ANSYS Workbench users can now directly connect to an ANSYS EKM data repository designed for enterprise or workgroup requirements or they can deploy a single-user version of ANSYS EKM from ANSYS Workbench to manage simulation data on their local machines.
Scalable and customizable, ANSYS 12.0 can be configured for advanced or professional users, deployed to a single user or enterprise, and executed on laptops or massively parallel computer clusters. For complete details, visit the ANSYS 12.0 web page.
Click here details on upcoming ANSYS 12.0 seminars.
Register for an ANSYS 12.0 webinar.
Visit the ANSYS Virtual Demo Room.
Download a white paper (registration required).
Read why DE’s editors chose ANSYS 12.0 as a Pick of the Week.
Subscribe to our FREE magazine,
FREE email newsletters or both!Latest News
About the Author

DE’s editors contribute news and new product announcements to Digital Engineering.
Press releases may be sent to them via [email protected].
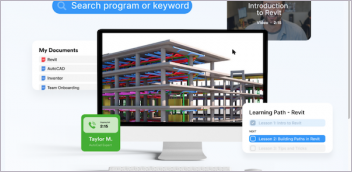

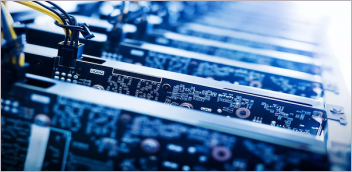
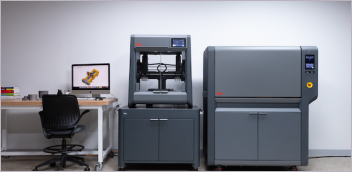