Virtual Printing Enables Next Phase of AM Adoption
Simulating 3D prints will make it easier to create high-quality end-use parts using additive manufacturing.

Image courtesy of Materialise.
Latest News
January 1, 2019
As more companies use additive manufacturing (AM) processes to create end-use metal parts (not just prototypes), quality and scrappage issues associated with AM have become a bigger issue. Many 3D printing technologies have demonstrated high degrees of variability regarding consistent parts creation, and because design for AM skills are often in short supply at most companies, there is great trial and error involved in creating usable parts.
That has resulted in a high percentage of scrap and wasted materials. To reduce waste and improve part quality, end users need a way to virtually test builds before creating physical parts.
An example of the print process in the Materialise Magics Simulation Module. Image courtesy of Materialise.
“What we see is that in order to industrialize and use the technology in higher volume production scenarios, we need to do a few things to get it right,” says Ravi Shankar, director of global simulation product marketing for Siemens PLM Software. “One critical area is to do what we call first-time-right print. Typically, companies attempt to print a part multiple times at a high cost before they actually achieve an acceptable result. That is delaying the transition of what is a very exciting technology into real production scenarios.”
“If you look at AM today, the scrap rate is still very high compared to traditional manufacturing,” says Stefaan Motte, vice president and general manager of software at Materialise. “You can see anywhere from 5% to 10% to 15% scrap, depending on the parts involved.”
Software vendors have responded with a variety of AM simulation tools, including solutions from Siemens PLM Software, ANSYS, Autodesk, Dassault Systèmes, Materialise and most recently ESI, which launched its AM simulation tool at Formnext in Frankfurt, Germany. Simulation helps companies predict the behavior of a part during production, so that they can optimize build preparation and reduce costs.
“Specific simulations can be done in the virtual environment to reduce errors and optimize the entire production process for a specific part or specific geometry,” Motte says. “You’re not just reducing scrap, but increasing productivity.”
The use of simulation also helps companies address the shortage of AM experts. “You need simulation to have stability in the process, because staff come and go,” says Brent Stucker, director of additive manufacturing at ANSYS. “It also helps companies get better results. We’ve seen an explosion of adoption of 3D printing by new companies, and they’re in this conundrum of seeing other people be successful with it, but they are six months in and turning out garbage. Simulation helps them be successful.”
Value in Virtual Printing
Software providers have developed AM simulation tools using various approaches. Materialise offers an AM simulation module (from Simufact Engineering) for its Magics 3D software suite that allows users to simulate a print, and then work with support generation and orientation tools in Magics. ANSYS acquired 3DSIM, and merged that company’s work with its own internal development program.
With underlying technology like XFEM analysis, the Simcenter 3D AM Process Simulation tool shows how the predicted distortion on the left is confirmed by the real-world part via the original CAD data on the right. Image courtesy of Siemens.
The ability to reduce waste and scrappage comes from being able to predict potential points of failure and provide operators with the information they need to correctly calibrate the machine and orient the part on the build plate, as well as ways to tweak designs so that they will perform well in an AM environment.
Dassault Systèmes offers simulation for a variety of 3D printing processes as well as post-processing operations. “We can capture process-dependent and machine-dependent crack initiations,” says Jing Bi, technical consultant at Dassault Systèmes SIMULIA. “Often the support structures are weak and break during the print because of large residual stresses. That can affect part distortion. That’s a big issue in metal printing. With the latest updates, we actually simulate and predict the exact crack initiation location, and how it propagates through the different support legs to exaggerate part distortion.”
ANSYS’ Stucker sees virtual printing having the same effect that “print preview” had on 2D printing decades ago—eliminating most of the frustration and mistakes that came with not being able to know whether what you’d just created on the screen was going to come out of the printer looking as you intended.
“That saved a massive amount of time in turning out something that looks correct,” Stucker says. “I’ve been working in metal 3D printing for years, and up until eight years ago you always relied on experiments. You’d print it, see how it worked and then try it again. With virtual printing, you move beyond physical trial and error and move to a whole new paradigm for developing products. You’re not only looking at the process, but also how the material performs, and how you get the microstructure so that it performs how we intended it to.”
ANSYS has approached this issue based on roles. There are simple tools that designers without simulation backgrounds can use that predict the properties of interest to them. Other tool sets are targeted at machine operators. There are also tools for traditional analysts or material scientists who need expert-level insight.
At Materialise, the company has worked closely with printer manufacturers to gather machine-specific data. “We get that information from builds that have been happening,” Motte says. “This is not generic information on machine type, but usage data on specific machines in a production environment.”
Complex Simulation Challenge
There are many factors that can affect how well a printed part conforms to expectations. Operator experience, machine calibration, environmental factors (temperature, vibration and humidity), position on the build plate, part orientation, material condition and the nuances of the specific print process can affect quality.
Simulation of heat exchanger displacement before being additively manufactured. Image courtesy of Additive Industries via ANSYS.
“We’re trying to provide a solution that lets end users not only design the part, but understand where the support structures need to be and how the print process should work,” Siemens PLM Software’s Shankar says. “They want to be able to anticipate distortions and shrink lines, and avoid collisions, as well as look at areas of potential overheating.”
Assuming the machine is operating properly, simulation allows users to evaluate a variety of “what if?” scenarios to determine the optimal printing approach. “To do that experimentally costs a fortune, but simulation defines the process parameters and geometry features that are the most robust. You find what works and then you lock down the machine calibration,” Stucker says.
3D printing equipment has a high level of variability. Two identical machines may produce different quality parts, or the same machine may generate variability quality over the course of a shift, or with different operators. In some cases, there can be variability even across different areas of the build plate.
“If you are printing one part and print it 10 times, you might end up with different part quality among those parts,” Bi says. “That could be due to certain machine parameters or environmental settings that have not been set up or correctly monitored to provide consistency.”
Bi explains that simulation can be combined with topology optimization and other technologies to generatively design a part, optimize the topology in functionality and weight, and then ensure that the design is optimized for digital manufacturing so that the machine can be properly programmed.
Virtual printing solutions can provide quick info for designers, who are generally not simulation experts and need faster answers to basic questions, Motte says. “They want to reduce the potential risks that have been identified,” he says. “They need quick answers. Process engineers can have immediate information without having to become experts in every single detail of simulation.”
Material Science Gap is Closing
Material science has not quite caught up to the needs of 3D printing—new materials are being developed, and existing materials don’t necessarily predictably behave when they are exposed to different 3D printing processes.
But new work in material science and features in some new simulation tools are helping companies grasp how these materials will perform (see page 34). “There’s a far bigger interest now for materials manufacturers to make those investments in refining and better understanding materials,” Motte says. “All of that know-how can feed back into simulation. But simulation can bring significant results even without some of those details.”
ANSYS offers its own intellectual property that helps create phase diagrams and properties that reflect the high cooling rates and other elements that can affect material performance. There are also tools in the software that can help customers create their own material property databases.
“We are shifting from a strategy of using our own internal experts to do this, to training our customers to be successful and take into account the unique microstructures and phases you get out of additive manufacturing,” Stucker says. “They can more quickly try out new chemistries and materials and come up with properties they are looking for from an as-built condition.”
Shankar says that Siemens PLM Software offers standard materials libraries, but many customers want to calibrate materials themselves. “They are looking for the data and thermal properties being measured, and then use that measured data to feed into the database,” he says. “Not only is that just the material, but also that material in combination with the 3D printer being used. The specific inputs are machine dependent.”
SIMULIA has specific features that can help users better predict material performance. “For parts that have different geometries, the material microstructure may evolve differently based on different machine settings,” Bi says. “With our simulation tools, we can track how the powder will evolve into a liquid state and then solidify, and we can track the microstructure phase of this. It’s not just the pure material; there are different microstructure phases in the material as it’s being built.”
A Path to More Optimized Printing
Future AM simulation features will focus on optimizing machine performance, increasing speeds and increasing print volumes, according to the vendors interviewed for this story.
An example of the print process simulated with ANSYS Workbench Additive. Image courtesy of ANSYS.
There will be more work done to optimize AM machines for high volumes of particular parts as end users will want to turn these printers to highly specific use cases, according to Motte. That means those users will want more capabilities when it comes to calibrating and customizing the equipment. “Some machine manufacturers still work in a very closed way, but there will be a lot of pressure on the manufacturers from volume production companies to open those machines and allow changes to be made,” Motte says.
Motte says that Materialise worked with one customer on the plastics side that was able to decrease production time by more than 40% after simulating changes in the part orientation and machine behavior. “That shows you the power of simulation,” he says. “The machine is 40% more productive after altering the production flow. That’s something you’ll see happening more in these volume manufacturing lines.”
Stucker adds that there will be a bigger push for more microstructure and property prediction capabilities. “Long term, people want to optimize performance of the component through a combination of geometries and properties and we need simulation tools that do both,” Stucker says.
The data generated by simulations can help improve the design of the printers themselves. “As this virtual testing becomes ingrained with machine manufacturers and users, and the entire supply chain, that will increase the rate of innovation and rate of success,” Stucker says. “That helps us get to another inflection point to take adoption of AM to an even higher rate.”
More Autodesk Coverage
More Dassault Systemes Coverage
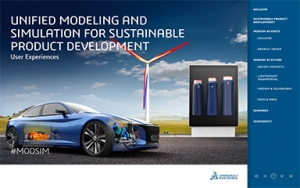
More Siemens Digital Industries Software Coverage
Subscribe to our FREE magazine,
FREE email newsletters or both!Latest News
About the Author

Brian Albright is the editorial director of Digital Engineering. Contact him at [email protected].
Follow DE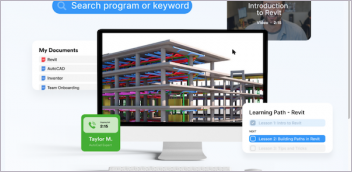

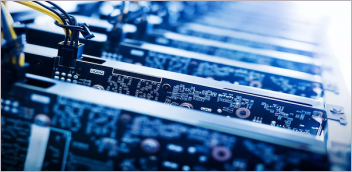
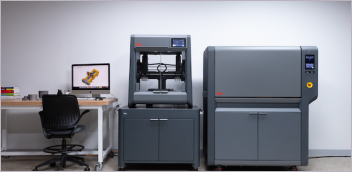