
The Hyproline initiative is working on developing high-performance additive manufacturing processes for large-scale, customized parts. Image courtesy of CCM.
Latest News
August 1, 2016
The goal of the Hyproline initiative is to design, implement and validate a flexible, high-performance additive manufacturing line for serial fabrication of customized high-quality metal parts. The initiative combines innovative component technologies for net shape manufacture, direct write structuring, inspection and intelligent automation. It began as a result of an EU FP7 Factories of the Future Program grant.
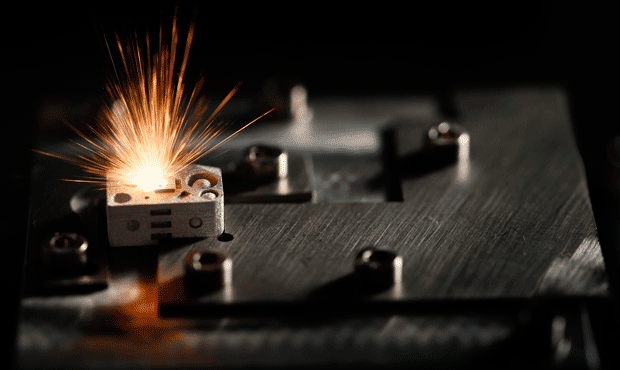
Hyproline endeavored to develop production lines designed to produce multiple, unique parts, while simultaneously adapting to the specific requirements of a given component on the same line. The solution featured an innovative combination of additive manufacturing and laser-based structuring, coupled with integrated process monitoring and metrology systems. The results were successful.
Program researchers focused on three metals: stainless steel 316L, titanium and copper, and on the serial production of customized parts in the order of 10mm with a goal of 10,000 parts a day.
One of the biggest challenges researchers faced was how to increase the quality of 3D printed metallic parts. ITI’s CADfix greatly contributed to the solution through improved slice generation from CAD and the processing of inline 3D scanning and laser ablation with real-time point cloud capture and 3D comparison. This culminated in the generation of customized laser toolpaths for live use by the continuously running production line.
CADfix Contribution
Software development is an important component of Hyproline, given the very large data sets. The team made progress on data flow for scanning of geometries with very high precision and on the processing of that information.
CADfix, ITI’s translation, repair, and defeaturing solution, was used to prepare CAD geometry for the additive manufacturing step, to convert the point cloud to the 3D surface, and to compare the as-produced 3D object with the CAD model while on the production line. CADfix was also used to generate tool paths to drive the laser ablation stage of the production line.
CADfix is ideally suited for this type of additive manufacturing because of its flexible, closely linked representations of geometry, ranging from continuous CAD geometry to discrete faceted geometry such as facets, slices or point clouds. Access to multiple forms of geometry enables CADfix to be effectively applied to all aspects of the AM geometry process chain. For the Hyproline platform, CADfix compared the point cloud scans to the as-designed CAD to extract the excess material to be removed by the laser processing stage.
Outcomes
By further developing the manufacturing process itself, as well as researching and applying work on materials, treating the parts produced, and supporting software, Hyproline adds capabilities to commercially available manufacturing systems. These capabilities include speed, product quality and versatility, thus improving time-to-market (TTM), which is a crucial competition parameter for SMEs. Hyproline promises to enhance the competitive position of Europe’s SMEs.
The partners are confident that the Hyproline project will remove major technical barriers, which today inhibit the use of AM due to limited accuracy and the high product cost associated with the post-processing steps.
More Info
Subscribe to our FREE magazine,
FREE email newsletters or both!Latest News
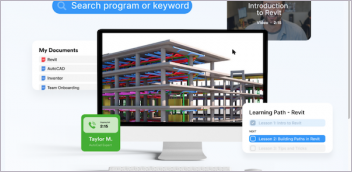

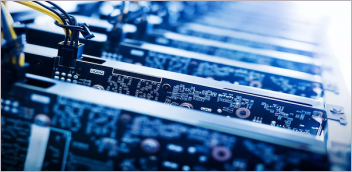
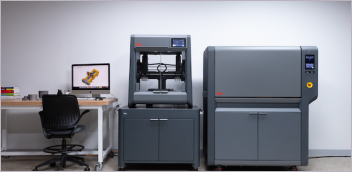