Using 3D Printing for Welding Fixtures

The on-demand webinar “Using 3D Printing for Welding Fixtures” demonstrates that 3D printing can produce durable, custom fixturing quickly, saving both time and money. Image courtesy of Markforged Inc.
Latest News
March 26, 2018
Off-the-shelf welding fixtures are multipurpose tools, albeit setup and tear down takes away profit-making time. But when you need customized or specialized fixtures for one-offs or single purposes, that's kids’ stuff. The costs and lead times to design, then machine custom, high-precision weld fixtures are budget- and schedule-busting. Maybe even a reason to turn away business. 3D printing can help ease some of these pain points.
Markforged's on-demand webinar “Using 3D Printing for Welding Fixtures” shows how 3D printing can help you contain costs and regain lots of productive time quickly. This is a fast presentation—just 13 minutes. Yet it packs in a ton of details and never strays into boosterism.

Basically, the webinar sets the table like this: You need custom and specialized weld fixtures to hold specific components in place. The more complex your structure, the more complex your fixtures get. Adapting traditional fixtures is a kludge job. High-quality and precise custom fixturing can ensure you do the job right. But machining high-precision custom or single-purpose fixtures takes weeks and a tidy checkbook balance. 3D printing offers three answers.
First, 3D printing makes parts exhibiting high precision and dimensional stability. Deployed wisely, fiber-reinforced 3D parts won't deform. Two, 3D print materials cost less than metals. Three, 3D printing provides shorter turnarounds to make customized fixtures. Like next-day delivery shorter.
A side benefit: 3D printing can reduce setup and tear down costs. How? You can design in features that allow for quick and simple alignment and easy removal.
The webinar puts this thesis to test through three implementation examples. The first steals the show.
It's a 3D printed fixture for track welding steel. After discussing some part details and matching them to 3D printing's capabilities, you're treated to a brief, unnarrated video of a human welding a structure with the fixture right there doing its job. Great stuff.
Next are examples of custom risers and mounts, followed by customized alignment jigs and check gauges. If not for the strength of the first demo, these examples alone would be showstoppers.
Perhaps the strongest aspect of “Using 3D Printing for Welding Fixtures” is its implied advocacy of 3D printing as a partner manufacturing system and not the avatar of a new world order. That pragmatic, “here's what you can do” approach makes this presentation an enjoyable and down-to-earth learning opportunity. See for yourself. Hit the link.
Thanks, Pal. – Lockwood
Anthony J. Lockwood
Editor at Large, DE
More Markforged Coverage
Subscribe to our FREE magazine,
FREE email newsletters or both!Latest News
About the Author

Anthony J. Lockwood is Digital Engineering’s founding editor. He is now retired. Contact him via [email protected].
Follow DE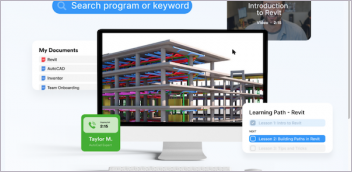

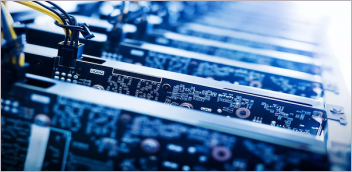
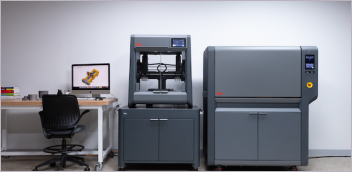