Latest News
January 1, 2012
By Mark Clarkson
For the last year-and-a-half, Andrew Huang has been the interim engineering director of the University of Michigan Solar Car team. He helps guide the engineering component of a team of more than 100 students designing and building a solar-powered car to compete in the World Solar Challenge in Australia—where they recently took third—and the American Solar Challenge in the U.S. Not all of these students are engineers; some are involved in business, logistics and operations, media relations, etc.
“We build a car every two years,” says Huang. “We’ll race the car twice: once in the Australian race and then again in the North American race.”
The bi-annual races are held on alternate years.
The solar car team and their car, Quantum, pose with Jack Roush, founder
of Roush Fenway Racing and one of the teams gold sponsors.
Photo courtesy of Diane Thach.
The team’s current car, Quantum, weighs in at 320 lbs. (sans driver), has a coefficient of drag (CDA) of less than 0.1, and should easily break 100 mph. Its predecessor, Infinium, was clocked at 105 mph. “I would expect Quantum to have a higher top speed and much better acceleration than our previous car,” says Huang. “Unfortunately, I can’t give you any numbers or estimates without revealing too much information about our battery pack.”
But What’s It Good for? Sure, the University of Michigan Solar Car project is fun for the students involved, but does anything practical come out of all this time and money? Yes, says Andrew Huang, the team’s interim engineering director. “The solar car is essentially the most efficient battery-electric vehicle possible,” he says. “We use the most advanced batteries, carbon fiber composites, electric drivetrains and aerodynamic designs to create such an efficient car. These are incredibly critical areas of development to an auto industry that is moving toward battery-powered vehicles. To meet consumer requirements, companies will have to increase their vehicle’s battery capacities, decrease their weight, and waste less energy in their motors and to aerodynamic drag.” Huang admits that the public will likely never see a purely solar-powered car for sale—not unless you want a car with an 8-hp motor. However, he notes that “we do a lot of work in increasing the power output, and thus viability of solar cells for power generation. Technologies similar to this are being developed and deployed in the southwestern US and other sunny places of the world—concentrated photovoltaics, he says. |
CAD, Of Course
DE was unable to obtain any sexy engineering drawings or CAD models to accompany this article; they’re also top secret, although we have been assured they exist. After all, not using CAD on a cutting-edge project like this wouldn’t just be crazy, it would bephilosophically impossible.
“Our design philosophy,” says Huang, “is that anything that exists on the car has to be modeled and assembled ]in the computer first]. You can’t just say, ‘It looks good to me,’ without knowing that the bolts will actually fit.”
The team does its mechanical design and visualization in SolidWorks, which has been a team sponsor since 2006. “We used SolidWorks to model all of our mechanical components,” says Huang, noting that includes the suspension, steering system, carbon monocoque chassis and wheels, among other parts. “We used SolidWorks to make sure power electrical systems would have enough space inside their enclosures. The circuit boards themselves—fuses, circuit breakers, the battery cells and so forth—all take up physical space.”
The team also uses SolidWorks to generate drawings for the manufacturers, sending designs out to professional machine shops to get the actual parts made.
Other Software
The solar car team uses a number of software packages to help design and optimize the car, most of which are available to as a part of the students’ tuition. If they’re not available, well, “software companies tend to be very charitable,” says Huang.
The team employed COMSOL multiphysics to do optimization on the car’s battery pack.
“Our first battery pack had some issues with overheating, internal resistanceall that sort of business,” says Huang. “We used COMSOL to model our connections within the battery pack and look for places where there was too much current.”
The team was able to fix the issues, and Huang says he can foresee multiphysics software “playing a big role in further optimizing the car.”
The computational fluid dynamics (CFD) component of the design requires its own specialized software. Huang reports that the vehicle’s aero team does all of its modeling in Siemens NX Unigraphics, the meshing in BETA CAE Systems ANSA, and the solving in ANSYS FLUENT.
According to Exa Corporation, Quantum was optimized with the company’s Exa PowerFLOW CFD software. The company said it’s software helped engineers achieve a 30% drag reduction compared to the previous car, resulting in an overall drag value below 0.1.
“Our work with Exa has opened a new chapter in the processes by which the aerodynamics of the vehicle are developed,” states Chris Hilger, Business Director for the team via a press release. “By collaborating with Exa and using their suite of simulation tools, Quantum will be the most aerodynamic solar vehicle in the US, and potentially the world.”
No Free Ride
Free software notwithstanding, the cost of putting together a competitive solar car capable of making an 1,800-mile run across Australia’s Outback is north of $1 million—although Huang is quick to point out that “we actually don’t see nearly a million in cash. Most of that is in-kind donations.” Those donations include everything from raw carbon fiber to machine shop time.
Still, there’s a lot of money that goes into building the car.
“A lot of components we need tend to be hard to get for free, and are rather expensive,” says Huang, “It’s mostly because they’re custom, and they’re the cutting edge in performance.”
Solar cells, for example, are expensive and not, Huang says, something you can generally get for free: “The battery pack is a huge part of the car, so that’s one of our large expenditures. We try to get the best cells that we can.” The car uses Panasonic lithium-ion batteries, which are not currently available to the public.
A Team Effort
Huang has been impressed by how dedicated people are to the solar car team.
Power Electrical Engineer Joe Menzia drives Quantum along Grand Traverse
Bay during the teams mock race in Michigan last summer.
Photo courtesy of Evan Dougherty.
“This summer, sometimes we would spend 90 hours a week on the car for about four months straight,” he says. “A solar car seems simple in principle, but to make a really great car, you have to spend all this time to make the tiniest, 0.5% improvement that will put you ahead of the competition. ]You have to] get your craftsmanship up to those really high levels.”
Plus, the cars are never really done. There’s always the next race to get ready for and, after that, the next car to design and build.
“You’ll finish the original design and you’ll think, ‘This looks a little strange; we should change that,’” says Huang. “Or, ‘Oh, we left out a heat sink in this place.’ It’s just constant revisions all the time.
“We have a saying: Good grades, solar car and a social life—pick two. It’s kind of a rough life.”
Contributing Editor Mark Clarkson is DE’s expert in visualization, computer animation, and graphics. His newest book is “Photoshop Elements by Example.” Visit him on the web at markclarkson.com or send e-mail about this article to [email protected].
MORE INFO
Subscribe to our FREE magazine,
FREE email newsletters or both!Latest News
About the Author
Mark ClarksonContributing Editor Mark Clarkson is Digital Engineering’s expert in visualization, computer animation, and graphics. His newest book is Photoshop Elements by Example. Visit him on the web at MarkClarkson.com or send e-mail about this article to [email protected].
Follow DE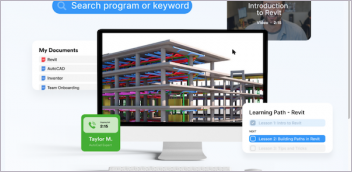

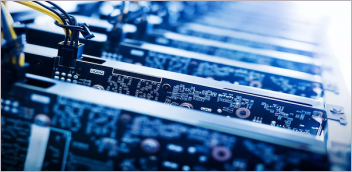
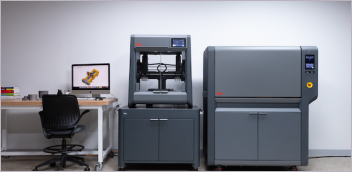