Toy Research Institute Studies Rapid Manufacturing Recycling Materials
Study shows the degradation that materials suffer under various processing cycles, time and temperatures.
Latest News
October 27, 2010
By DE Editors
Selective laser sintering (SLS) is a rapid technology where successive previously defined layers are caused to solidify powder under the action of a laser to form a 3D object. The range of materials for this technique is wide, as any material that becomes soft and has a low viscosity under heat could be potentially used. Nevertheless, after several processing cycles these materials are notably degraded in such a way that they cannot be re-used.
The Toy Research Institute (AIJU), Ibi, Spain, says it has developed a systematic method to determine the degradation that non-solidified SLS processed materials suffer after several uses. The application of this technique shows the changes the materials suffer in their structure according to temperature and time exposure.
This technology is based on the Melting Flow Index or MFI of the non-sinterized material during its processing. Previous studies undertaken demonstrate that the MFI is the fastest and simplest method to measure the powder degradation rate for the SLS process, according to the association. From the fluidity difference before and after the SLS process some conclusions regarding the degradation suffered by the material during the process can be obtained. There is a minimal average weight decrease due to the breaking of molecular chains, which implies material degradation.
Within the study of recycled PA12 powder for sintering, the next activities will focus on studying the influence that powder location has on its own properties. These tasks have been done within the IBE-RM project framework, partially supported by MICINN and the European Union with FEDER resources and the Matsinter Project supported by IMPIVA - Regional supporting organization.
For more information, visit AIJU.
Sources: Press materials received from the company and additional information gleaned from the company’s website.
Subscribe to our FREE magazine,
FREE email newsletters or both!Latest News
About the Author

DE’s editors contribute news and new product announcements to Digital Engineering.
Press releases may be sent to them via [email protected].
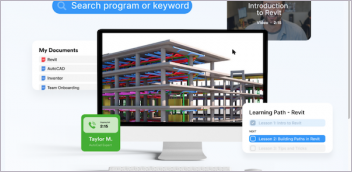

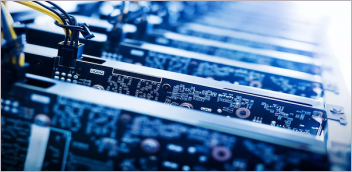
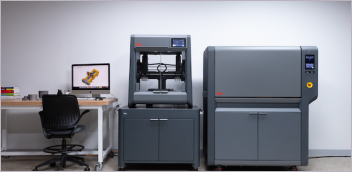