Latest News
July 1, 2010
By John Hanks, National Instruments
![]() |
The complexity of devices and systems has increased significantly in recent years, requiring a mechatronics system-level approach to design. This approach enables engineers to integrate mechanical and control design, quickly realize a prototype, and reuse algorithms in the final embedded deployment platform. Growing investments in the medical, life sciences, and renewable energy fields as well as developments in industrial machines are fueling this system-level trend.
This approach significantly improves the design process by integrating the best available development practices and technologies to streamline design, prototyping, and deployment. By dividing the design process into parallel threads, engineers are able to implement a more efficient development process. In the past, a team developing a control algorithm for a mechanical system had to wait for a physical prototype. Now engineers can get started earlier using a virtual prototype based on design models and simulation data.
In addition to reducing development time and its inherent costs, this approach enables vivid collaboration between design teams and provides system performance data in the early development phases. A digital model of the complete system allows teams to jointly optimize the overall system while maximizing performance.
Yet a successful mechatronics design process requires integrated design tools. During the past few years, tool providers have heavily invested to support this design approach. Companies such as National Instruments created interfaces to provide seamless integration between different tools. This enables engineers to create virtual prototypes of their systems with a seamless path to embedded hardware and to reuse code and make the most of investments made in the design and simulation phases. During prototyping and deployment, algorithms need to be implemented on embedded hardware.
During deployment, engineers have a variety of options to cut development time. These include designing a custom control system at the component level to optimize cost and deploying to commercial-off-the-shelf (COTS) embedded systems. Reaching the most appropriate decision based on these tradeoffs is often the difference between earning a profit and experiencing a loss. To test market acceptance before a cost-optimized custom design is built, “application ready” subsystems are often used to prototype or as a deployment platform.
Over the last couple of years there has been a trend toward customizable embedded platforms that offer the simultaneous flexibility of a custom layout and rapid implementation associated with COTS hardware. About seven years ago, National Instruments introduced the RIO (reconfigurable I/O) platform. A programmable plug-in board for PCs featuring an FPGA and built-in analog and digital I/O offered customers a way to embed software algorithms in hardware using the graphical development tool NI LabVIEW. Since then, this technology has evolved and is currently used in rugged industrial-grade embedded hardware as well as board-level products. High-level graphical programming tools provide a system-level design approach by abstracting the complexity of low-level drivers and board support packages, streamlining the design process.
Software plays a key role in the future of mechatronics and embedded systems. By providing a system-level view on different design aspects and abstracting the complexity of the latest technologies, software tools enable engineers to implement high-performance systems for the challenges of tomorrow.
John Hanks is VP of Product Marketing, Data Acquisition, and Industrial Control at NI. Send e-mail about this commentary to [email protected].
Subscribe to our FREE magazine,
FREE email newsletters or both!Latest News
About the Author

DE’s editors contribute news and new product announcements to Digital Engineering.
Press releases may be sent to them via [email protected].

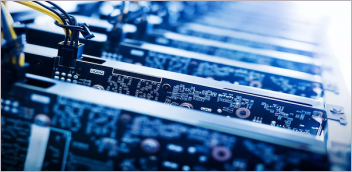
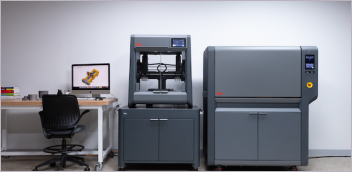
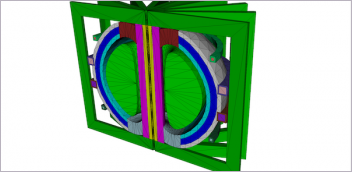