Latest News
December 1, 2012
By Kenneth Wong
In Paris, after his lecture on the range of architectural modeling programs available, Dr. Peter Macapia, architect, artist, founder and director of labDORA, was confronted by a testy audience member who asked, “So, is design just about running a program and pushing buttons?” Macapia replied, “Not if you’re a creative thinker.”
![]() |
Peter Macapia, founder and director of labDORA, began using solidThinking Inspire for structural engineering. Eventually he shifted to using the optimal shapes the software proposed as inspiration for new architectural environments. |
Several years later, when he discovered Altair Engineering’s solidThinking Inspire, Macapia would remember that awkward exchange. For shape optimization, Inspire does simplify the operations so that users can obtain the answers they seek with a few inputs, followed by a mouse click or two. Is that what design has become?
Software-driven optimization is a natural evolution to software-driven simulation, powered by finite element analysis (FEA) programs. Simon Pereira, senior product manager at simulation software maker ANSYS, mapped out the anticipated trajectory of ANSYS users’ technology adoption in the pursuit of robust design.
“It starts with single physics, moves to multiphysics, then what-if scenarios, design exploration, optimization, and ultimately robust design with probabilistic algorithms,” he says. “Most of our customers are halfway up this ladder ]in what-if scenarios and design exploration]. We’re pushing them to go a little higher.”
The push is evident in the digital optimization tools that have sprung up in the last few years: Altair Engineering’s solidThinking Inspire and OptiStruct; Autodesk’s Inventor Optimization; Siemens PLM Software’s NX Toplogy and NX Shape Optimization; RBF Morph with ANSYS Fluent; and Within Technologies’ Enhance software, to name but a few.
In some cases, optimization leads to possibilities that the designers might not have intuitively created. Modern hardware and software can subdivide a geometric model into millions of micro-elements (known as meshes in analysis programs) and compute the best alternative for each. Consequently, software-driven optimization can reveal structural weaknesses, potential failures, and opportunities that a designer cannot spot from sight alone. But that doesn’t mean designers can now sit back and take a nap. Making sense of the optimized shape proposed by the software still falls on their shoulders.
Putting Designs on a Diet
Topology optimization—identifying the best possible shape for your project—is often driven by the need to reduce material or weight. There are clear advantages to shaving off excess weight from your product. A lighter vehicle or aircraft, for example, gives you better fuel economy. In large-volume manufacturing, a lighter, smaller personal computer requires less material to build and package, and costs less to ship. But optimization possibilities have to be balanced against the stresses and loads anticipated. Shave off too much material from the wrong part of the structure of a car, and you’ll end up with a vehicle that won’t survive even a low-impact crash.
Many optimization tools are built on top of robust analysis tools. In fact, the input they often require—material type, load, pressure, fixed points in the geometry, and so on—are nearly identical to the variables used in analysis programs.
Where optimization programs differ from analysis programs is the type of results they offer. Instead of displaying stress distribution, displacement and deformation, they display the best (or optimal) shape for counteracting the anticipated loads and stresses.
Light Enough for Edison
In addition to developing engineering software, Altair also operates Altair ProductDesign, a thriving product design consultancy, headed by Mike Heskitt as COO (see page 26 for more information on the company). His division has been recruited to help design the next generation Very Light Car (VLC) by Edison2, a company specializing in workable, sustainable transportation solutions.
Edison2 had set its sight on a prize—the Progressive Insurance Automotive X PRIZE, to be precise. In 2010, Edison2 grabbed the $5 million prize for Mainstream VLC. The company’s electric VLC is now on the market. It’s continuing its pursuit with the development of the next-generation VLC.
“]Edison2] investigated what really drives the efficiency of a vehicle. It came down to two fundamental things: weight and aerodynamics,” says Heskitt. Now, while keeping most of the design parameters that made its first VLC a success, the company wants to further refine the next version. “We’re helping ]Edison2] with their safety strategy, and with the weight—by putting materials at the right place and choosing the right materials. We’re also helping them with improving the ride and handling of the car,” Heskitt explains.
For topology optimization, Altair is using primarily OptiStruct to identify the optimal load paths in the structure. From there, a design concept will be developed for further refinement. Altair would also be using RADIOSS for crash simulation and safety verification.
“We can routinely reduce the mass of a mature design anywhere from 10% to 15%, but applying the process this early in the concept stages can yield even greater benefits,” Heskitt says.
Jumpstarting Design with Optimization
Siemens PLM Software provides a host of simulation tools that are tightly integrated with its design modeling program NX. In releasing NX 8.5, the company adopted a similar strategy for its optimization tools.
“The advantage of this integration is that designers and design engineers can directly access these capabilities within their familiar design environment to jumpstart the concept development process,” says Ravi Shankar, director for Simulation Product Marketing at Siemens PLM Software.
For example, the NX Topology Optimization module guides the user through a step-by-step process to dramatically reduce the weight of a heavy part (such as a bracket), starting from a very rough shape. The output from the optimization process is reference geometry that the designer can use to design the part, while taking manufacturability and other criteria into consideration. The module allows the user to optimize the part for a longer life by eliminating areas of stress concentration.
“Data flows seamlessly from the design environment into these optimization modules, so the user can concentrate on making better product decisions rather than wasting time moving files or data around between different applications,” Shankar says.
Automatic Morphing Leads Optimal Shape
Gilles Eggenspieler, a senior product manager at ANSYS, says he believes the key to shape optimization is mesh-morphing.
“A mesh morpher is a tool capable of performing mesh modifications in order to achieve arbitrary shape changes and related volume smoothing without changing the mesh topology,” he wrote in his presentation of RBF-Morph, an add-on module to ANSYS Fluent. RBF-Morph was developed by an ANSYS partner.
“The software doesn’t predefine the optimum function. The user defines it: uniform velocity, maximum temperature, maximum power, minimum resistance ...” Eggenspieler wrote. “Then the user defines the sections to morph. The rest is automatic.”
In defining morphing possibilities, the user may place certain constraints. For instance, if your objective is to seek minimum resistance, and the design submitted for morphing is a typical four-door passenger car, the software may propose a flattened block as the best shape (in theory, that would produce the least resistance). Therefore, to preserve the shape of the vehicle, you may place constraints around its windshield, hood and passenger compartments.
2A![]() | 2B![]() | 2C![]() |
The evolution of a bracket optimized in OptiStruct. 2A shows the original design; 2B shows software-proposed optimized shape; 2C shows final result based from optimization results. |
In a typical analysis workflow, you run a simulation, study the results, modify the geometry, re-mesh, then re-solve the design, and it goes on for several rounds until you get the optimal shape. In software capable of automatic morphing like RBF-Morph, the solver has the ability to take the results from the initial analysis, then try out various morphing strategies to achieve the optimal function he or she desires. In doing so, the software starts with various experimental approximations, until it identifies the right direction. The advantage with this method is, you no longer need to manually oversee the iterative process.
Bio-inspired Optimization
London-based Within Technologies takes optimization a step further by creating optimized designs that are ready to build using additive manufacturing (AM). The Within Enhance software specializes in optimizing parts by using variable-density lattice structures and surfaces. The company describes the algorithm in its software as “bio-inspired.” In optimization, the software mimics the way objects are designed by nature (such as bones)—using denser lattice structures where heavier load is expected, and more porous structures where lighter load is expected or flexibility is required.
“Our works in certain spaces, including aerospace, motorsport, medical and footwear, all gain advantages from using additive manufacturing to achieve extremely light-weighted results of around 30%,” says Katherine Prescott, executive assistant, Within Technologies. She adds that in the majority of cases, traditional manufacturing methods cannot produce the optimal shape desired, so Within relies on AM to produce them.
“Our software allows users to import material settings at the start, so the part is optimized taking into account the material properties the part will be built in, as well as the design rules of additive manufacturing,” Prescott explains. “We also utilize advanced 3D printer parameter settings—for example, in our medical structure—to allow complex structures to be built at a resolution that wouldn’t be possible otherwise. With Within Software, you can use optimization to produce the final design; it’s unlike other software, which generates a model for inspiration, which then needs to be revalidated.”
Number Crunching in the Cloud
“In Inventor Simulation, you can say, I want to minimize the mass of my design, while keeping a certain safety factor and the stress level within a certain range,’” says Bankim Charegaonkar, a product manager at Autodesk. “But when we took a look at it, we realized it might be intimidating for some people. So we came up with a new environment, called Inventor Optimization—really, just a subset of the functionalities in Inventor Simulation.”
The new optimization tab reduces the steps to a mere four icons. You have the option to define which aspects of the design can be treated as variable (for example, you may specify that the height and width of the part can vary within 30% of the current values). With Inventor Optimization, the number crunching takes place in the cloud, a remote server accessible from the Internet (the company has adopted the same approach to powering its simulation and visualization products); therefore, your local CPUs remain unencumbered by the process.
“We keep it simple. We set it up so it only optimizes by reducing the weight of the part, and it only uses the safety factor as guidance,” says Charegaonkar. “That should be helpful because you know, from general rules, what the required safety factor is for your product in the industry.”
A Tool for Discovery and Inspiration
Altair’s Heskitt recalls many instances where he felt, based on his professional training and experience, he knew exactly what the optimal shape for a certain project should be, only to be surprised by the dramatically different solution proposed by the software.
![]() | ![]() | ![]() |
The optimization of a camera’s mounting arm, completed in Siemens PLM Software’s NX 8.5 with Topology Optimization. |
“Sometimes the result is obvious and it reinforces your assumption,” he says. “But many times, when we put in the loads for our structures, we got results we didn’t expect. After investigating why the results are the way they are, we usually gain far deeper understanding of the project.”
For one reason or another, all of Macapia’s ideas about building seem to emanate from structure. He once considered writing a topology-optimization program of his own from scratch, or developing a plug-in to his favorite surfacing program, Rhino—all because he wanted to integrate structural analysis into design. When he stumbled on Altair’s solidThinking Inspire (called Morphogenesis Form Generation at the time), he decided it was the right program—not only for his research but also for his classroom at SCIARC/Pratt Institute, where he serves as adjunct assistant professor of architecture.
“I can use ]Inspire] to solve structural problems, to find structural fitness, and I have. That’s really important, of course,” says Macapia. “But what’s more interesting is, you can reinvent structural systemsArchitects can build buildings, but the art of architecture is about rethinking what a building is.”
A software like Inspire, Macapia says, gives him “responsibilities as well as creativity” because he can think about both “structural optimization and structural innovation.” He likes to experiment by applying different load conditions to his structural concepts, and varying the loads to see what new optimized shapes the software might propose.
“You see interesting patterns, so you can follow up on those,” he says. “It’s really about the potential for imagination.”
Don’t Put Blind Faith in Software
“Once you get the optimization results back from the software, you still need to understand what the results are telling you,” notes Autodesk’s Charegaonkar. “You still need to make a design decision based on what the safety factor is. Do I change the diameter, leave the chamfer or the fillet in, or change the thickness of the part? You need to decide what the acceptable tradeoff is.”
Altair’s Heskitt agrees. “To take full advantage of optimization, you have to spend time and effort to define your environment carefully,” he says. “You do need to understand the loads and constraints pretty well. If you leave out some fundamental loads, your optimization will be missing out on something important.”
Even if you have confidence in the software, you are still responsible for reshaping software-proposed shapes into consumer-acceptable products. The software doesn’t make aesthetic judgments when considering geometric alternatives, but consumers do when they purchase something. You may be able to obtain a mathematically optimal shape with the simple push of a button in a software menu. But good design is so much more than mathematics.
Kenneth Wong is Desktop Engineering’s senior editor and resident blogger. He believes the optimal time to write articles is after his morning espresso drink. Email him at [email protected] or share your thoughts on this article at deskeng.com/facebook.
INFO
Subscribe to our FREE magazine,
FREE email newsletters or both!Latest News
About the Author

Kenneth Wong is Digital Engineering’s resident blogger and senior editor. Email him at [email protected] or share your thoughts on this article at digitaleng.news/facebook.
Follow DE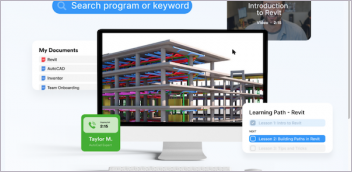

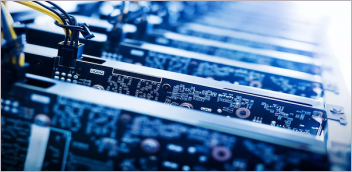
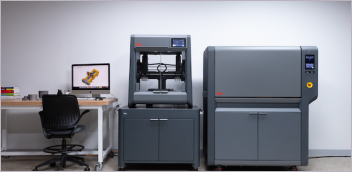