
Developers of the latest generation of PLM platforms provide access to environmental databases. This allows engineers to compare product designs with sustainability factors. Image courtesy of Dassault Systèmes.
February 17, 2022
The emergence of sustainability as a business imperative has changed the basic framework of how product designers must work. The creation of sustainable products now requires engineers to contend with a new, more eclectic set of demands. These not only include engineering and enterprise requirements but also environmental and social interests. As a result, the trade-offs that design engineers must make have become more complex than ever.
The success of new products increasingly hinges on developers’ ability to define and design products that provide the right level of functionality, for the longest use period, with the best energy efficiency and the lowest environmental footprint, at the right price.
To do this, engineers need greater visibility of the broader canvas so that they can better juggle the expanded assortment of demands. At the same time, product lifecycle management (PLM) software developers have begun to add new functionality to their engineering tool sets and now seek to leverage emerging engineering practices like digital twin (Fig. 1).
Dimensions of Change
Companies must recognize that this trend requires engineers to fundamentally change the way that they look at products. Focusing primarily on performance metrics and business objectives is no longer enough. Engineers must now include new dimensions in their designs that are grounded in engineering domains that have long been outside of mainstream attention.
These considerations include issues like the consumption of nonrenewable resources and environmental damage incurred by the product or process, extending from design through retirement. An example is the measurement of a vehicle’s sustainability. This process should extend beyond fuel efficiency and include factors such as the materials used to create the vehicle, emissions produced during its use, maintenance requirements and recycling options.
These concepts have been a topic of discussion for over 25 years, but recently, they have become a driving force in the marketplace.
“Sustainability is the most powerful driver of change in product design and development, next to the COVID-19 pandemic and software-defined products,” says Youssef Tuma, global lead for engineering and manufacturing at Accenture Industry X. “All stakeholders are demanding it—from customers and employees to investors and regulators—which puts it high on the agenda of business leaders.”
Standards Bring Clarity
To help translate general sustainability concepts and goals into actions, governmental and non-governmental organizations have developed standards such as the EU Taxonomy for Sustainable Activities, the International Organization for Standardization (ISO) and Voluntary Sustainability Standards.
These aim to define key sustainability classifications and metrics, which can then be translated into design requirements, manufacturing protocols and retirement guidelines. Standards also enable businesses to enrich their decision-making processes by better understanding the impact of their choices and actions.
“Achieving these benchmarks is a critical part of a company’s ability to successfully certify and/or sell products across global markets,” says Jonathan Dutton, sustainability marketing director at Dassault Systèmes.
As helpful as the standards are, however, they touch on only some of the issues that engineers must incorporate in designs. In fact, many more factors must be considered.
Features of Interest
Sustainability design issues can vary widely by industry and geography. However, a small set of core issues are the most common. These fall into four broad categories: materials, energy, waste and pollution.
To address these general issues, design engineers must answer questions like: Do we use fossil or renewable materials, and how hazardous or harmless are they? Can they be recycled, or must users dispose of them? How durable are they, and what does that mean for the product’s shelf life? Can the product be repaired at a reasonable cost? Can critical components be renewed? How much energy does the product consume?
Although the design phase plays a critical role in sustainability development, companies must not limit efforts to a single segment of the lifecycle.
“Many of the aspects on which companies focus when designing for environmental impact are interdependent and touch several product lifecycle stages,” says Tuma.
For example, how a company engineers a product determines how sustainably manufacturers can produce it. The design also influences how efficiently or inefficiently a product can be packaged, shipped, stored and returned. Companies looking to implement more circular business models need to factor in all these aspects.
Companies also must avoid disconnects between the key performance indicators (KPIs) for different departments. For example, R&D KPIs might be very different from those of manufacturing. A unified company vision and KPI structure is paramount for sustainable product development and production.
The takeaway from reviewing all these factors is the importance of achieving balance between functionality, profitability and sustainability. The most sustainable product won’t help the planet if consumers don’t purchase and use it because it’s too costly or because the features, texture or other characteristics don’t match their needs and expectations.
A View of the Broader Canvas
To achieve this balance, engineers must adopt a systemic view of product development. Rather than looking through a specific functional lens, designers should focus on the broader picture, which helps them to cultivate a better understanding of the holistic impact of design decisions and the many interdependencies that ultimately define the product.
“With systems thinking, we consider the whole process of sourcing, manufacturing, using, and recycling a product and its components in a holistic manner,” says Ilan Madjar, managing partner and co-founder of xLM Solutions. “For example, sourcing a material might have an environmental or even social impact.”
Systems-wide thinking promises to help development teams to move beyond incrementalism toward systemic change as presented by the circular economy and large-scale industry decarbonization.
By adopting a holistic approach to sustainability, designers will also be able to better see the linkage between engineering and business interests.
“Systems thinking will be fundamental to appreciating how economic value retention and capital investment is distributed across the value chain,” says Tuma. “For example, the planning and construction phase for large-scale power transmission capacity in Europe will take five to eight years. This will cause latency in fulfilling the market demand for renewable energy.”
PLM’s Role in Sustainability
The key to understanding and mitigating a product’s environmental impact lies in data from the full product lifecycle. Unfortunately, traditional PLM systems are less able to serve as the single source of truth. For example, when looking at the increase in front-end data, these software platforms often fall short of companies’ aspirations to bring together all required data points. Most legacy PLM systems are just not built to effectively handle today’s volumes of data.
This situation, however, seems to be changing. PLM software vendors have started taking the necessary steps required to close the data gap. The latest generation of advanced PLM platforms is proving to be more capable of facilitating product optimization across dimensions such as user experience; ease of manufacturing; maintainability; and environmental, social and governance performance (Fig. 2).
In industries where data changes often and requires intense tracking, more agile PLM platforms can now help trace product information through the lifecycle, tracking sustainability’s impact in the process. That said, more improvements specific to sustainability are still required.
“At the early design stage of all new and existing products and processes, PLM platforms and CAE software simulation will need to have sustainability KPIs baked in for sustainability ideation,” says Keith Hanna, vice president of marketing for design and engineering at Hexagon. “This will mean sustainability indicators such as the lifecycle analysis of CO2 emissions, total energy usage, and water and air pollution impact of the product being factored into existing and new platforms.”
Moving PLM to the cloud is another necessary step. This infrastructure change will help companies better integrate and process data, leveraging the cloud’s significant analytics and computing resources and simplifying the building of the digital thread and twin infrastructures. Armed with these enhancements, companies can better streamline and run sustainability simulations at scale, across different engineering departments, even with manufacturing.
Cloud-based PLM also opens the door for better and easier enterprise integration, which provides a more reliable conduit between engineering systems and business back-office functions to power design-to-market and bill-of-materials procurement optimization.
Looking ahead, PLM systems may be used to track information about the carbon footprint of certain materials and do constant sustainability checks using lifecycle assessment tools and databases. If handled correctly, the data can identify areas where sustainability efforts will succeed or fail.
A Virtual Window on Sustainability
Probably one of the biggest contributions the new breed of PLM platforms makes to sustainability efforts is digital twin enablement. When considering the inherent capabilities of this virtual technology, it’s an easy leap to see what digital twin can do to advance product sustainability and to achieve the balance of divergent interests required by green design.
In terms of collecting and integrating the data required to achieve sustainability, the digital twin seems to be a perfect match. Product twins collect design and performance data from the real and digital worlds to better inform product design and optimize operational performance. Use of this data bolsters sustainability by improving product performance, quality, reliability, material use and energy consumption (Fig. 3).
In addition, by enabling sustainability modeling and simulation, digital twin promises to provide the means to quickly and cost-effectively visualize and evaluate the effects and interplay of the multiple variables and scenarios that come into play (Fig. 4).
“To attack specifics such as energy utilization and material selection, we need to manage the overall performance of a product and its manufacturing operations at a more fundamental level,” says Keith Perrin, senior director of digital transformation, manufacturing intelligence division, at Hexagon. “This demands a more nuanced, higher fidelity working model than a bunch of files in a common database. We also need a model that allows us to work more closely together, iterating more aggressively, in an agile manner, against energy and performance targets.”
An example of this can be seen in recent achievements in the consumer electronics sector. For example, a global computer hardware company reduced the embedded carbon footprint of its new computer by 47% and built a shell made out of 100% recycled materials using digital twin technology.
“Their product developers used a virtual prototype to run a wide range of thermal, acoustic performance and electromagnetic behavior scenarios,” says Accenture’s Tuma. “Generative design and advanced mechanical simulation and optimization led to lighter structural parts and higher torsion and flexion performance. They also allowed a significantly higher-than-usual rate of recycled materials.”
A Look Ahead
Driven by government regulation and consumer demands, companies now realize that they must be more sustainable in their product development approach. Accompanying this trend is a shift to a more circular economy.
Prevailing wisdom says that the place to begin sustainability initiatives is at the design stage, where the greatest impact can be made.
“Within the retail, fashion and consumer products industries, design decisions account for roughly 80% of a product’s environmental impact,” says Bill Brewster, senior vice president and general manager of global retail at PTC.
Despite agreeing in principle to the importance of sustainability, many companies hesitate to take substantive action toward achieving this goal.
“According to a Financial Times survey, less than a third of companies now take into account environment and/or social-related metrics when assessing the value of product and service development,” says Dutton. “The reasons for this vary, but many stem from the cost and complexity of adapting existing business models for sustainable needs.”
To counter this problem, companies pursuing sustainability are turning to new engineering practices like digital twins and next-generation PLM platforms.
“Digital twins enable the integration of sustainability objectives at the start of the product lifecycle, as this is where environmental impacts and product costs are determined,” says Brewster. “Virtual twins allow for faster design iterations and reduce the need for physical tests, driving significant CO2 benefits. By leveraging PLM and digital twins, companies can readjust the way products are made and offered at speed and scale, with the use or reuse of lighter, more durable materials so products last longer.”
More Dassault Systemes Coverage
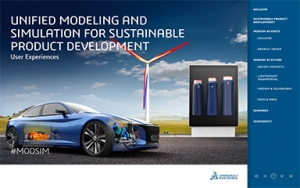
More Hexagon Manufacturing Intelligence Coverage
More PTC Coverage
More xLM Solutions Coverage
Subscribe to our FREE magazine,
FREE email newsletters or both!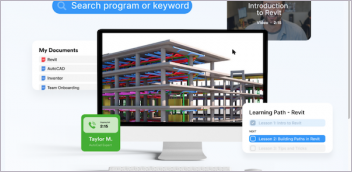

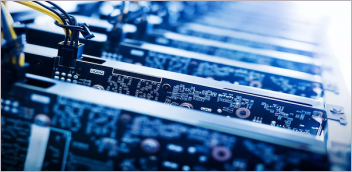
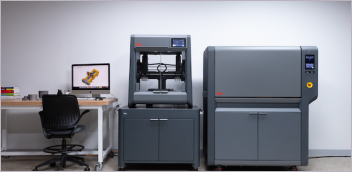