
Integrated into the CAD modeling environment, SolidWorks Sustainability offers guidance on the environmental impacts of a design in various categories. Image courtesy
of SolidWorks.
February 17, 2022
Electricity is measured in watts. Brightness is measured in lumens. Engine strength is measured in horsepower. Rotating forces are measured in torque. How is sustainability measured?
After last year’s United Nations Climate Change Conference (COP26) in Glasgow, Scotland, governments around the world began announcing and adopting new targets and policies for mitigation and conservation. For conscientious engineers, this is an opportunity and a quandary.
Heavily involved in conceptual design, engineers influence not only how a product functions but also how it’s made, used and recycled. But how can we quantify a product’s environmental impact? Is there a benchmark or unit that defines how “green” something is? How can this value be captured when the product is not yet made?
Some people point to the CAD-integrated Sustainability Module that debuted in SolidWorks 2010 as a good start, but also acknowledge more is needed now that climate change has accelerated.
Measuring Sustainability
SolidWorks’ Sustainability tools are fully integrated into the software. Based on the design’s topology, material choice and production method, the module gives instant feedback on the following:
- Air acidification
- Carbon footprint
- Water eutrophication
- Total energy consumed
The calculations are based on some user input and the GaBi environmental Lifecycle Assessment (LCA) database, derived from scientific experimentation and empirical results from the field. Because the estimates are displayed in a CAD modeling environment, design engineers can get real-time updates on the design decisions they make, from different materials and production methods to topology changes in the design.
SolidWorks Sustainability is currently available as an Xpress version, limited to examining parts, or the full version, expanded to cover assembly designs. Later, SolidWorks added a cost estimator, allowing users to balance the environmental impact against the cost of such designs.
Blind Spots
Keith Hanna, VP of Marketing, MSC Software, Hexagon, believes the conceptual design phase is the key to help determine sustainability scores.
“Generally, you know most of your cost in the early design stage. I say it’s also true of all the sustainability metrics,” Hanna says. “We will see pressure on all the PLM [product lifecycle management] and simulation software companies to embed sustainability into the design and UI [user interface] of the software.”
Stephen Hooper, VP and GM of Fusion 360, Autodesk, believes carbon counting gives an incomplete picture of the product’s sustainability.
“If you look at the actual carbon output based on the material volume of a design, you’re only getting a very small part of the picture,” Hooper says. “I also think you’ve got to be thinking about what happens to that product through its lifespan.
Based on a series of user input and embedded lifecycle data, the SolidWorks Sustainability module reveals the design’s environmental impact. Image courtesy of SolidWorks.
“Information like carbon or energy consumption shouldn’t just show up in the 3D CAD model. They should also show up in the PLM tools,” says Hooper.
“Not only should you look at how much energy is used by your product but also the nature of that energy: where it comes from, how it’s extracted, what type of machine is used for the extraction, if it’s surplus to fuel and so on. You have to go five levels deep to get a full lifecycle assessment,” says Zoé Bezpalko, sustainability strategy manager, design and manufacturing, Autodesk.
For Hooper and Bezpalko, CAD-integrated carbon counters and recyclability indicators are good R&D considerations. Bezpalko thinks education also has an important role to play in cultivating a new generation of sustainability-conscious product designers.
“It’s not just about building the right tools. It takes the right mindset and the right tools,” she says.
Hanna also foresees a similar need. “Universities and educators are going to have to change their courses on PLM, on CAD, CAM and CAE to include design for sustainability in the curriculum,” he says.
Designing with Sustainability in Mind
In the last 5 years, the term Design for Additive Manufacturing (DfAM) became part of the industry lexicon as many began exploring ways to design parts specifically to be produced in 3D printers. But it’s a new skill that has to be taught. Finding traditional parametric CAD’s limitation to produce shapes ideally suited for 3D printing, some have also sought out additive manufacturing-specific design software, such as Frustum (acquired by PTC) and nTopology. A similar movement might be driven by the focus on sustainability.
At Autodesk, the Fusion 360 R&D team has been prototyping sustainability tools.
“Similar to DfAM, the technology might show up in the conceptual design environment and provide upfront analysis and guidance in real time. At the moment it’s focused on carbon, but there’s no reason we can’t expand it,” Hooper says.
In 2019, Autodesk entered into a partnership with aPriori to integrated aPriori’s Cost Insight Engine into Autodesk Fusion 360’s generative design workflow.
“With generative design, users have been able to analyze different design variants based on things like structural rigidity, weight or fatigue. With our partnership with aPriori, we added cost as a parameter, so people can look at cost versus structural rigidity. Once we have the carbon material libraries embedded, the next step is to offer the opportunity to look at cost versus carbon, or mechanical performance versus carbon,” Hooper explains.
Hanna also thinks comprehensive material data on toxicity, carbon emission and energy use may become part of future simulation software. “In my view, LCA data has to be across the board in the CAD, CAM and CAE markets to allow engineers to design for sustainability,” he says.
Brian Thompson, Division VP and GM of CAD Segment, PTC, believes better material data in PLM is the key to nudge engineers toward sustainability.
“Your material choice might make a part very difficult to recycle or service,” he says. “There’s a lot of debate recently about the right to repair for electronic, like handheld devices.”
Apple’s trade-in program, for example, offers consumers cash credit for older devices in its upgrade scheme. Such a program reverses the disposable culture that generates electronics waste. (For more, read “Right to Repair Movement Attracting Attention,” October 2021, DE.)
In November 2020, PTC struck up a partnership with simulation software provider, Ansys. The outcome was the Creo Ansys Simulation bundle targeting designers and engineers.
“If a series of capabilities in PTC Creo and Ansys that are directly related to sustainability coalesce into a package, we could conceivably package up all these as a module for sustainability,” Thompson says.
Currently, there’s no such package in PTC’s lineup.
Sustainable and Profitable
One conventional argument against developing greener products is the profit margin. Right or wrong, the general impression among businesses is that greener products cost more to produce, due to limited material choices and the required safeguards in manufacturing methods. But with growing consumer demands for greener products and regulatory requirements that penalize toxic products, the equation is reversed. In the future, greener products may yield more financial incentives.
A 2019 Accenture study revealed more than half of the consumers would pay more for sustainable products designed to be reused or recycled.
“The shift in consumer buying, with more consumers willing to pay extra for environmentally friendly products, reinforces the need for companies to increase their commitments to responsible business practices,” says Jessica Long, a managing director at Accenture Strategy.
More recently, in “The 2021 U.N. Global Compact Accenture CEO Study on Sustainability” involving 1,230 CEOs across 113 countries and 21 industries, “CEOs report that their businesses are already experiencing the damaging effects of climate change and they are ready to take bold action.”
In a recent article that identifies green technologies worth investing in, The Motley Fool points out, “Due to climate change concerns, the world is moving away from carbon-based fossil fuels to cleaner alternative energy sources. The decarbonization of the global economy will take an estimated investment of more than $100 trillion over the next three decades” (“Investing in Renewable Energy Stocks,” December 2021, Fool.com).
“The consumers that are coming of age, coming into the workforce and bringing their buying power have different priorities, like, ‘is this design sustainable?’, ‘what kind of footprint does this leave?’ [and] ‘is it reparable?’” says Thompson.
Hooper looks at consumer demands and regulatory requirements as the “carrot and stick” of sustainability. “I actually think the carrot is a lot more effective,” Hooper says. “You can hit businesses with a stick, but they’ll just break the rules or hide things. But the carrot encourages organizations to adopt more sustainable initiatives.”
Carbon counting seems like an overly simplified method to measure sustainability, but it is a good starting point, says Bezpalko. “It has allowed us at a governmental level and global level, to have sustainability development goals and the Paris Agreement.”
Having established a common benchmark, “we can slowly refine what the environmental footprint of a product is, throughout its lifecycle,” she says.
More Autodesk Coverage
More Hexagon Coverage
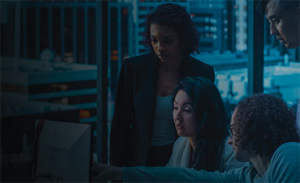
More PTC Coverage
Subscribe to our FREE magazine,
FREE email newsletters or both!About the Author

Kenneth Wong is Digital Engineering’s resident blogger and senior editor. Email him at [email protected] or share your thoughts on this article at digitaleng.news/facebook.
Follow DE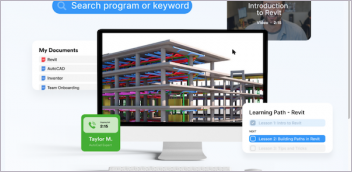

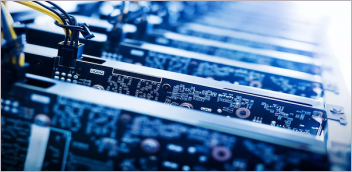
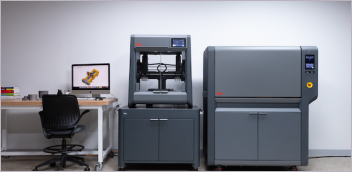