Simulation Blazes New Innovation Frontier
To advance the tech, vendors are boosting simulation’s accessibility to stakeholders and bringing in more functionalities for AI, automation and multidisciplinary modalities.
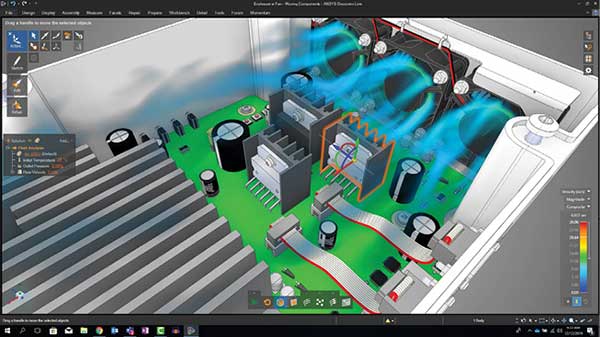
The GPU-based ANSYS Discovery Live delivers real-time insights into how design changes will impact simulations. Image courtesy of Ansys.
Latest News
May 1, 2020
On the heels of increasing product complexity, shorter time-to-delivery cycles and rising consumer demand for highly personalized products, simulation is in the spotlight as a critical innovation vector and fixture in the engineering toolbox.
To secure simulation’s role in modern-day product design, innovation is happening on two fronts. First, there are myriad efforts to democratize simulation, making it easier for the average engineer to routinely tap sophisticated analysis capabilities as part of their core design environment without the need for cumbersome file translations, extensive meshing and a reliance on experts to refine and advance the models.
Second, plenty of efforts are underway to boost the rigor and breadth of advanced simulation. Multidisciplinary capabilities, real-time simulation, automation and infusions of artificial intelligence (AI) and machine learning are underpinning a new wave of simulation solutions designed to power up next-generation products in development hotspots like autonomous vehicles, electrification and 5G.
Although not all activity is new, the pace of innovation has stepped up, and engineers seem hungry to get on board and embrace more widespread use of analysis tools.
“Simulation, despite our best efforts, hasn’t permeated the everyday design engineering ranks as well as we would have liked—that is finally going to change,” says Brian Thompson, divisional vice president for PTC’s Creo CAD business. “The biggest innovation we see relates to the ability to make simulation easier and simpler for the everyday engineer. It’s less about pushing the boundaries of what you can simulate with new techniques or brute force computational technologies.”
Simulation Simplified
Much of the current simulation innovation is focused on transforming what has historically been complex technology for experts into a toolset that is usable and accessible for mainstream engineers. The so-called “democratization” of simulation has been underway for some time, but recent technology advances are finally making good on the promises.
Today, it’s common to see basic analysis capabilities covering areas like finite element analysis (FEA) and computational fluid dynamics (CFD) folded into popular CAD and design tool environments. At the same time, a growing number of products put far more sophisticated and highly specialized simulation functionality well within reach of mainstream engineers typically as integrated extensions.
Autodesk is addressing the problem and removing much of the work associated with preparing CAD geometries for simulation and moving models between design platforms. The company now offers a CFD-based electronics cooling workflow directly inside Fusion 360, and officials say there will be additional, similar streamlined workflows to come.
PTC has continued to build in an array of simulation capabilities into its core Creo CAD platform, making FEA-type structural, thermal and vibration analysis solutions available within the familiar Creo user interface.
Through a partnership, PTC has gone further with Creo Simulation Live powered by Ansys. The tool positions simulation as a real-time feedback mechanism for in-progress designs as part of the regular upfront design workflow, not just as a late-stage tool for validation. At any point in a Creo workflow, engineers can set specific temperature or thermal loads, for example, and the software delivers analysis-enabled feedback that steers design exploration and drives the iterative process.
“Half the problem associated with simulation is that engineers have to move data from the design environment to the analyst environment, which creates a loop of continuity that is difficult to maintain and manage,” Thompson says. “Now simulation is getting easier to use and so fast, design engineers can use it as part of their everyday workflow.”
The Ansys view of spreading simulation use is not just about making it easier and more accessible to non-experts—it also involves making simulation use more pervasive across all engineering stakeholders and throughout each stage of the design process.
“Simulation used to be a capability only a handful of top analysts in a company would engage in to determine how a physical device might work or how fluid would flow through a structure,” explains Larry Williams, Ansys’ director of technology. “Over the last few years, we’ve been driving the idea of more pervasive simulation. Instead of simulation being a scarce resource only available to [select users in] big enterprise industrial product manufacturers, it’s now a more central part of the workflow.”
Ansys is focused on numerous areas to meet this goal. It is leveraging automation, streamlined user interfaces and tools like Discovery Live to eliminate complexities associated with simulation use and promote more widespread use of analysis tools in the upfront design process. It is also taking a multiphysics approach to extending its analysis portfolio.
“In order to be pervasive, you have to be comprehensive—to be true to life means you need to include more than one kind of simulation,” Williams says.
Consider a biomedical application involving simulation of the human heart; Williams notes it would require a range of physics to perform a realistic simulation, including electrical signal, structural and material modalities.
COMSOL is also pushing hard on multiphysics innovations at an expert level in highly specialized areas such as autonomous vehicles, high-frequency electromagnetics and lithium-ion battery modeling. But the company also is making multiphysics capabilities accessible to non-experts. Key to that effort is Application Builder, a tool that lets simulation experts with years of experience create easy-to-use applications based on their simulations.
With Application Builder, multiphysics expertise and models that were historically the domain of Ph.D. experts can be made available to a much wider audience. This includes use by engineers as part of their upfront design exploration or for non-engineering experts like sales and marketing people who can leverage the apps to more effectively communicate product development choices and performance.
At Harman International, a library of COMSOL apps created with Application Builder is being leveraged by various engineering groups to predict loudspeaker performance with various configurations under different conditions. By democratizing simulation via the COMSOL apps, simulation experts are then freed up to focus on other, higher value projects, including work the company is doing in virtual reality.
Volkswagen Kassel is using COMSOL Application Builder capabilities to let non-experts in mechanical simulations predict stresses in rotors. The apps help increase product quality by automating the lengthy model creation process as well as standardizing models and results, says Marie Hermanns, one of the simulation experts at VW Kassel.
“With a few clicks of a mouse, they can make single physics or even multiphysics available to people who have never touched simulation because they don’t have expertise or time to dig into that area,” explains Bjorn Sjodin, COMSOL’s vice president of product management.
It also prevents the simulation experts from becoming bottlenecks in the development process.
“It’s inefficient for the engineer to go to the expert over and over again if they are changing a parameter,” Sjodin explains. “[With COMSOL Apps] if they change the width or thickness of something, they can run a simulation and get results immediately without bothering a simulation expert. It makes for a completely new way of working with simulation.”
Virtual Reality Meets Simulation
Melding virtual reality (VR) capabilities with simulation is another way to frontload the engineering process with insights gleaned from analysis-led design. Siemens Digital Industries Software is embedding collaborative VR capabilities in its STAR-CCM+ environment to help engineers to this.
Siemens has been offering VR functionality as part of its simulation portfolio, but more recently introduced Collaborative Virtual Reality, which allows dispersed teams to interact in the same immersive environment in real time. This allows for guided tours of products in progress as well as the ability to tap into expert knowledge for feedback on design decisions as well as on building, refining and reviewing mesh strategies and digital twins.
VR is also enhancing simulation workflows in COMSOL’s lineup. COMSOL now supports GL Transmission Format (gITF) files, a new standard promoted by the Khronos Group for sharing 3D scenes and models between programs. This allows COMSOL Multiphysics users to export simulations as gITF files, enabling a more intuitive way to present results.
“[gITF support] allows you [to] present simulation results to customers that are easier to grasp in a real-world context,” Sjodin says. “If you can insert a colorful plot representing stress temperatures or fluid flow into a real-world environment like a factory in context, it’s easier to explain the results of simulation to a wider audience.”
Real-Time Simulation and AI
Beyond simulating individual components or subsystems, the trend toward model-based engineering is driving a need for operational-level simulation so product designs can be evaluated in the context of their operating location, according to Arnold Free, chief innovation officer at CM Labs, a provider of simulators and simulation software targeting automotive and industrial equipment use cases.
Consider the example of cars with lane-keeping or even autonomous capabilities, where you need to gather mountains of test data to train models—a scenario that is far too complex for physical testing as well as for traditional offline simulation tools.
What’s required, Clark says, is real-time simulation capabilities coupled with AI and machine learning functionality.
“Real-time simulation is really important to training autonomous systems,” Free says. “It’s not enough to build a system model; you need to be able to take that model and test it in snow and icy conditions.”
Generative design is another emerging area that applies simulation, AI and machine learning techniques to drive what-if scenarios that help engineers make design decisions more quickly.
As opposed to the traditional workflow of applying simulation to determine how to make a potential design lighter or pinpoint and address structural integrity issues, generative design leverages AI techniques to devise a range of possibilities based on specific design parameters, facilitating trade-off studies and greatly accelerating the process.
“Fully-integrated generative design is another beachhead in the front on the democratization of simulation,” says PTC’s Thompson. “It’s simulation for building design alternatives faster and more efficiently than a design engineer could do on their own.”
Creo 7.0 incorporates generative design functionality based on the Frustrum technology that PTC acquired in November 2018.
Process Integration and Automation
In addition to making simulation capabilities more accessible to mainstream engineers, companies like Ansys and Aras contend it’s necessary to make simulation knowledge available to the broader enterprise, not just keep it tucked away within engineering silos.
With platforms like Ansys Minerva, powered by Ansys, organizations can secure and manage simulation data across the greater enterprise. They can also tap into process automation capabilities designed to establish optimized simulation workflows and promote widespread sharing of simulation assets across departments proper through governance.
Ansys’ Williams contends these kinds of enterprise structures, which are common for mainstream business systems, can help establish simulation as an enterprise-wide business intelligence capability. This way, organizations can connect simulation and optimization to their larger product development lifecycle processes—a key tenet for making simulation use pervasive, he says.
“You advance simulation by making it a business-level decision support and knowledge management system,” Williams contends. “It can be integrated and used across the organization much like PLM.”
More Ansys Coverage
More Aras Coverage
More COMSOL Coverage
More PTC Coverage
Subscribe to our FREE magazine,
FREE email newsletters or both!Latest News
About the Author

Beth Stackpole is a contributing editor to Digital Engineering. Send e-mail about this article to [email protected].
Follow DE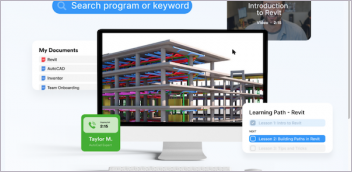

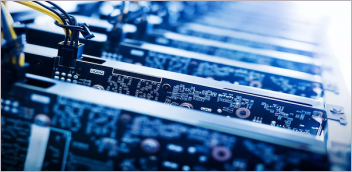
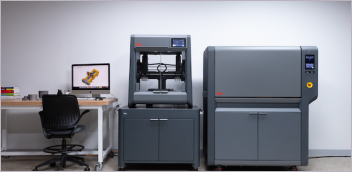