Reebok Makes New Strides in Major League Baseball with Signature Shoe Design
Product development time shaved off "Big Papi's" new shoes with the use of rapid prototyping software.
Latest News
December 18, 2008
By Susan Smith
![]() Screen capture of the shoe sole in Magics RP. |
When a major all-star athlete needs a signature shoe in time for a Major League Baseball event, how does an athletic shoe company get a shoe developed to stringent specifications and ready in time?
That was the dilemma faced by Reebok when one of the players it sponsors, Boston Red Sox’ David Ortiz, nicknamed “Big Papi,” needed a signature shoe in time for Major League Baseball’s 2007 All Star Break. The shoe would need to meet Big Papi’s expectations while also adhering to Reebok’s standards.
For starters, Reebok sought tools to hasten the development cycle of the shoes. Typically its shoes are designed and developed between its Canton, Mass., location and one of its Asian facilities, making it imperative that there is communication and the ability to share files between all parties.
In the typical design process, shoes take about 18 months to go from concept to store shelf. A product brief is created by the marketing group, based on many influences, such as current product sales, consumer data, the competition’s offerings or even pure innovation. Once this brief is written, a designer is assigned to create a shoe to best meet the brief’s specifications. A collaborative effort between the design and marketing departments ensures that the shoe meets requirements such as design and price.
After the initial design is approved, the information needed to manufacture the shoe is delivered to a development center in the U.S. or Asia. CAD files or rough sketches usually comprise the information from which uppers are created and assembled, molds are opened, parts are sampled and finished sample shoes are assembled into design confirmation samples. Samples must be shipped back to the U.S. to be reviewed by marketing and design teams. Modifications are made to the design where needed, making sure market requirements are met as well as maintaining the consistency of the Reebok product line. Clearly, this is a time consuming process.
![]() Big Papi’s shoe, ready in time for the 2007 All Star Break. |
Once the final design is settled upon, it is sampled and the shoes are sent through four stages of technical review to reconfirm design and test for form, fit, function and durability. Then the shoe is ready to move into the commercialization process, which includes the creation of production tooling and finalizing processes such as assembly, quality control, and packaging.
With Big Papi’s shoes, Reebok had to “crash” the shoe design, meaning they had to crunch the time taken to design and produce the shoe. This type of project is reserved for times when a market shift creates a need for a new shoe in a much shorter time frame than 18 months. The shoe design is then accelerated or “crashed,” as they say in the industry. Because the athletic footwear industry is a fashion industry and creates high demand for new product, this type of development has become common.
Because Reebok needed to speed up the process for Big Papi’s shoes considerably, they needed their designers and developers to be able to interact with a physical 3D part so they could understand it and foresee potential problems. When files are used across several CAD platforms, as they are when traded between different locations and suppliers, file formats such as STL can be adversely affected. In order to build RP parts quickly for each facility, the STL files need to be repaired. Paul Bates, director and Gary S Rabinovitz, RP Lab Manager of Reebok International Ltd. said they chose Magics RP for STL repair.
By using Magics RP’s new automated tools and wizards for file repair, Reebok was able to achieve a much faster turnaround for their STL files.
Getting started with the Magics RP software took some adjustments, because the combination of bad STL files developed via traditional surfacing CAD tools coupled with getting used to the new software program made it tough going. At that point it could take three to four hours to repair an STL file before it could be sent to Reebok’s prototype machines.
![]() Giant floating version of Big Papi’s shoe. |
The good news is that once these files were clean and watertight, designers and developers could do great things with them. For example, a mirrored image could be made by just the click of a mouse. Reebok could produce multiple samples and parts could be hollowed, which saved on material costs and build times. The company could do part measurements and resize parts.
Over the years, Reebok has taken advantage of advancements made in Magics RP such as the IGES translator and added it to their arsenal of tools. This helps them import an IGES file into Magics RP, which streamlines the translation process with third party software.
Big Papi was “on his feet” with his new shoes completed in time for the 2007 All Star Break, which he was obviously happy about. A giant display of the shoe also floated in San Francisco Bay outside AT&T Park, home of MLB’s San Francisco Giants.
Reebok International, Ltd.
Canton, MA
Materialise
Leuven, Belgium
Subscribe to our FREE magazine,
FREE email newsletters or both!Latest News
About the Author

DE’s editors contribute news and new product announcements to Digital Engineering.
Press releases may be sent to them via [email protected].
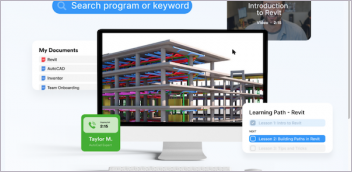

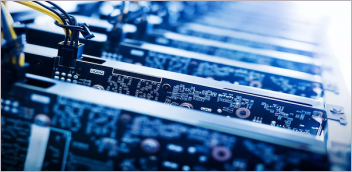
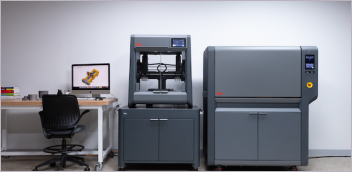