Rapid Tooling: The Manufacturing Disruptor

Direct metal printed tooling inserts. Image courtesy of 3D Systems.
Latest News
July 1, 2015

3D printing is not a new technology, of course. Even though it has been around for several decades in the manufacturing industry, recent technological developments have raised its profile among makers, hobbyists, DIYers and the public in general. The creation of 3D printers on a smaller and more affordable scale has led to a lot of hype about the future of consumer-based 3D printing, but that’s not stopping manufacturers from finding more and more practical uses for the technology today.
“There is just an amazing array of very smart, creative people that are figuring out new ways to use this technology. That’s no hype,” says Bill Dahl, vice president, Products & Marketing at Solidscape, a Stratasys company.
Many companies have been using 3D printing for prototyping or for making end-use parts. However, manufacturers and industrial designers are also using 3D printing for rapid tooling, “a broad term that covers a variety of different types of molds, dies, patterns, forms, fixtures, jigs and other tools that are made using 3D printing or other manufacturing methods that are faster than traditional tool making,” says Tom Charron, vice president of Product Marketing at 3D Systems.
Aiding Traditional Manufacturing
Traditional manufacturing practices often use tools and materials that are expensive and can take a long time to create. This forces companies to iterate slowly, creates a need for large production runs and increases risk. What if the product fails or doesn’t catch on?
According to Charron, 3D printing your tooling reduces costs and time to market by providing “faster prototype tooling and faster manufacturing ramp-up.” It provides lower costs because “3D printed tools themselves are often less expensive than CNC (computer numerically controlled) machined soft tools” and also “because manufacturing problems, such as moldability, assembly problems, etc., are found faster and corrected sooner, before investing in expensive hard tooling .”
Cost Saving Techniques
While rapid tooling with 3D printing saves money by producing tools more quickly, it can also reduce costs by taking advantage of a digital inventory for those tools.
“Rapid tools allow companies to discard or recycle old tools rather than warehousing them for infrequent production of legacy components,” Charron says. “With digital inventory, companies just print a tool on demand, produce a short run of parts, and discard or recycle the tool.”
Manufacturers don’t have to store forms in a warehouse if they are 3D printed. Simply reprint the forms you need when you need them. Dahl says his company uses Stratasys printers in the manufacturing process to create their own line of 3D printers. They have used 3D printed trays that hold the tools used by the workers. “We have workstations in the assembly of our printers and at each one of those workstations, to operate efficiently, we need the right tools in the right place,” Dahl says. “We built custom 3D-printed trays that have the exact tool right there on their assembly bench. If it’s not there, they can quickly identify it, order it or make a new tool. But more importantly, it encourages everybody to put the tool back in its appropriate place. You wouldn’t believe what this has done. It has built in efficiency into our production process.”
Another cost-saving aspect of rapid tooling , according to Andrew Snow, senior vice president at EOS of North America, is that 3D printed tools are “much more precise and can reduce time to market up to 70%.” He described the 3D printing tooling process as a way to “grow the tool.” According to Snow, costs can be reduced because the 3D-printed tool provides “precise geometry, which means you grow the tool once or twice. Conventional processes take much more time to create and there is a significant savings in material.”
Time may provide the largest savings using rapid prototyping. “3D printing is the fastest way to make most types of tooling—typically with same day or next day turnaround,” Charron says. “For example, 3D printed injection molds are printed in a few hours, versus two weeks to three weeks for aluminum soft tools that are rapid CNC machined. 3D printing allows companies to iterate designs faster, shorten development windows, save money on tooling, 3D-printed tools cost a fraction of the money required for traditionally made tools, and produce limited product runs very quickly.”
Rapid Tooling Advantages
A client of 3D Systems, Bi-Link, is a supplier of mechanical components. The company uses 3D printed injection molds to create limited run and prototype production plastic parts for a variety of engineering clients.
Snow said EOS’ clients can “create more custom jobs, custom designs, can perform quick redesigns, and can employ part count consolidation” techniques so that they can manufacture fewer parts, thus shortening the manufacturing process time.
A Solidscape client created a prototype for a wearable device that wirelessly connects to a smartphone in five weeks and at a cost of $4,000 using conventional methods. Comparatively, the second prototype they made using 3D-printed rapid tooling techniques only cost only $300 and was made in one week. Because of the 3D printers’ speed and precision for creating molds and prototypes, the tooling they produce is made quickly and for a far less cost.
What Tooling Can be 3D Printed?
3D printers can handle many materials and print different types of tools. They are being used to create room temperature vulcanization (RTV) molds by 3D printing master patterns for casting materials that include wax, gypsum, low melt alloys, metals, urethane, epoxy or even polyester resins. It is also used in hydroforming to create molds or negative molds for epoxy tool pouring that can be used in the shaping of ductile metals. Also, it creates molds for thermoforming, vacuum forming and fiber layout.
And, 3D printers are being used to create molds with materials like thermoplastic, thermosetting polymers or even elastomers. 3D printing is also a direct tool production solution to create jigs and fixtures, and it excels at making custom 3D printed jigs for special purpose tools or production runs. Molds are also printed for wax patterns for plaster, sand and spin and die casting. According to Snow, the only limitation right now to 3D printing is “the size of the tool you can grow.”
The Future of 3D Printing and Rapid Tooling
Rapid tooling using 3D printing techniques has a bright future, but don’t believe the hype that it is a replacement for traditional manufacturing processes. “Not completely, but in several cases, 3D printing rivals or even surpasses traditional manufacturing processes,” says Charron. “For shorter runs or prototyping, 3D printing has the level of accuracy required and achieves a level of speed that simply can’t be matched.”
Solidscape’s Dahl says 3D printing and rapid tooling will affect the future of manufacturing. “The adoption rate continues to grow. It will democratize this process to the smaller companies,” he says.
Snow says 3D printing and rapid tooling will “create new jobs, and new spinoffs creating new units of business.”
Rapid tooling using 3D printing techniques offers more flexibility with time, material costs and customization. Designers can create more precise molds more quickly than before, making a better product at a lower price and in less time.
Subscribe to our FREE magazine,
FREE email newsletters or both!Latest News
About the Author

Brian Benton is a freelance writer based in Florida. He writes the CAD-a-Blog website at cadablog.blogspot.com.
Follow DE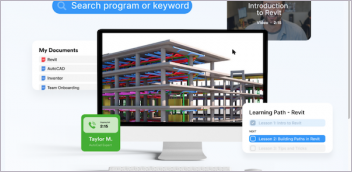

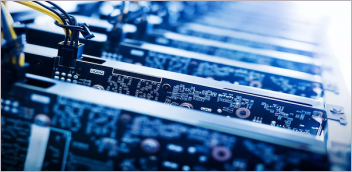
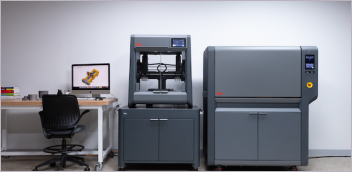