Advanced Materials Allow Engineers to Print, Glue and Drive!

BMW’s 3D-printed water pump, built from an aluminum alloy powder. Image courtesy of BMW.
Latest News
October 1, 2015
A car that’s glued together sounds like a preposterous idea, but you may have already used one. The BMW i3, a poster child for the era of mass-produced composite vehicles, is assembled with a combination of welding, bonding and adhesives.
The BMW i3’s passenger cell, dubbed the Life Module, is made of carbon fiber reinforced plastics (CFRP). The vehicle’s powertrain, chassis, battery and structure making up its Drive Module are made of aluminum. “The CFRP structure requires only a third of the number of body components used in a conventional steel body; the Life Module’s basic CFRP structure comprises around 150 CFRP parts in total,” reveals BMW. Because of the reduction in parts and the use of advanced adhesives, the carmaker is able to shave off significant production time. “At 20 hours, the total processing time in the body shop and on the assembly line is only half of what would be required in a conventional production process,” states BMW. (See “A Revolution in Car Making: BMW i Production”)
Next to the use of composites, BMW is also exploring 3D printing or additive manufacturing (AM) in metal. In April, during the season of the German Touring Car Master, BMW announced that one of its racecars was sporting a powertrain fitted with the 500th water pump wheel made on a 3D printer. “In a race, the high-performance powertrains run up to 70% of the time under full load; in addition, the moving parts in particular have to handle extreme conditions. This is why, back in 2010, the BMW engineering team developed a one-piece, light-metal water pump wheel to replace the previously applied series plastic part,” writes BMW.
In the article, Dow Automotive, an adhesive supplier to the BMW i3 project, and NanoSteel, a company breaking into metal-based AM, provide insights into the two cutting-edge approaches.
A Different Kind of Bond
The use of composite materials like CFRP nudges automakers toward bonding and adhesives instead of traditional welding and bolting. BMW writes: “Significant advances in the development of the adhesive mean it is now workable for only 90 seconds after being applied to a component and before adhesion begins. An hour and a half later it has fully hardened and achieved its full strength. This represents a tenfold acceleration of conventional adhesive hardening times.”
Ana Wagner, Dow Automotive’s global strategic marketing manager, pointed out, “The use of adhesives reduces welded parts, which increases the vehicle’s load bearing capacity. It also reduces noise, vibration, and static and dynamic stiffness, leading to increased safety and crash behavior.”
Original equipment manufacturers (OEMs) like BMW tend to have unique specifications with assembly processes that vary from plant to plant. Therefore, Dow Automotive works closely with such customers to address their needs. “Dow Automotive adhesive was customized to accommodate the unique assembly process for the BMW i3. The cure time also was customized to meet the assembly time requirements of vehicle production,” says Wagner.
Dow Automotive noted, “Composites are gaining traction in automotive production due to their weight-saving potential, yet they remain difficult to join. Adhesives offer a reliable alternative to traditional mechanical and thermal processes, which cannot be applied to these lightweight materials.”

Wagner thinks the use of composites will enable part consolidation among automakers. “Composites can be molded into the desired shape as a single part to replace what used to be three or four parts,” she says. The indirect benefits of adhesives include a reduction in CO2 emissions. Wagner pointed out, “Adhesives enable OEMs to use thinner steel or alternative materials, including aluminum and composites (like carbon fiber), or a mix of these materials for the purposes of lightweighting the vehicle. Lightweighting leads to improved fuel economy and reduced CO2 emissions.”
Dow Automotive products are free of the chemicals regulated by the RoHS guidelines; the company issues written assurance of this to its customers. The company’s adhesives comply with the Global Automotive Declarable Substance List (GADSL), an initiative by the automotive industry leaders, parts supplier, and chemical/plastics industries to be transparent about the use of certain substances throughout the supply chain.
A Different Kind of Print Job
When 3D printing first emerged, it was a rapid prototyping method, a way for engineers and designers to quickly produce physical mockups of their ideas. Printers typically relied on plastic filaments as materials. With 3D printing, it’s possible to fabricate and manufacture shapes in complex geometry outside the range of traditional machining. However, the use of structurally inferior materials (compared to metal’s durability) limited the parts built with this technology to prototypes—not end-use parts or finished products.
The technology entered a new era when manufacturers began to explore the idea of producing end-use parts with 3D printing. The development of metal-based 3D printing now opens new possibilities. Celebrating the deployment of a 3D-printed water wheel pump in one of its racecars at the German Touring Car Masters event, BMW noted: “[3D printing] allows for the inclusion of design refinements in the six-bladed centrifugal pump wheel, whose implementation would require much greater effort with other production methods.” The new part was printed using selective laser melting (SLM) in aluminum alloy powder.One company betting on the trend is NanoSteel, which, in its own words “designs new steels using conventional steel alloying elements in novel combinations.” Last September, NanoSteel entered the AM market with the expansion of its engineered powders business. “By leveraging its uniform metal matrix microstructures in the laser-sintering process, the company was able to build a crack-free, fully dense bulk sample. NanoSteel’s initial focus in additive manufacturing supports the market need for on-demand, on-site wear parts while addressing the current challenges in 3D printing of high-hardness parts,” the press announcement states.
The company reveals that its technology creates steel powders that are “well suited to the rapid cooling experienced in most AM processes, facilitating the generation of unique mechanical and physical properties.” Its materials are currently undergoing validation tests.
“Metals in general are more challenging to print than most plastics. They must be printed with higher power (energy density) to melt the metals, and the process must be tightly controlled to obtain full density, and avoid cracking and oxidation. There are a few stainless steels that are 3D printed today, mainly 316L and 17-4PH, but providing significant wear resistance remains a hurdle. This is where our materials excel and can provide additive manufactured solutions for industries such as oil & gas, tool & die, and agriculture,” says Harald Lemke, vice president and general manager of Engineered Powders at NanoSteel.
In April, GE’s 3D-printed sensor housing, dubbed T25, got FAA clearance to take off. In a post on GE Reports, the company explained, “[The T25 is a] piece of silver metal that houses the compressor inlet temperature sensor inside a jet engine … [It’s] the first 3D-printed part certified by the FAA to fly inside GE commercial jet engines.” More than 400 of the GE90-94B jet engines powering Boeing’s 777 fleet are expected to be retrofitted with the T25.
The new part is printed in a cobalt-chrome alloy to protect the temperature sensor’s delicate electronics from icing and punishing airflows inside the engine. “Additive manufacturing allows engineers to replace complex assemblies with single parts that are lighter than previous designs, saving weight and boosting a jet engine’s fuel efficiency,” writes GE.
The trend suggests a need for CAD modelers and simulation software programs to add tools specifically developed to process geometry intended for AM. A sub-segment of the design software market is devoted exclusively to simulating the process of CAM using CAD geometry. A similar repertoire may be in its early development for 3D printing. In the latest release of Autodesk Fusion 360, Autodesk added the ability to automatically generate support structures needed in 3D printing projects. Another company, Materialise, specializes in developing and marketing software for those deploying 3D printing for medical use.
“The true benefit of additive manufacturing is shown when parts are created that could not be made with conventional manufacturing processes. AM gives the designer free complexity, which creates advantages like lightweight matrix structures and internal channels that would not otherwise be possible,” says Lemke.
Terry Wohlers, founder and president of the AM industry analyst firm Wohlers Associates, says metal-based 3D printing will likely facilitate part consolidation, but cautioned, “The cost structure will need to improve dramatically, and faster machines will help.”
Subscribe to our FREE magazine,
FREE email newsletters or both!Latest News
About the Author

Kenneth Wong is Digital Engineering’s resident blogger and senior editor. Email him at [email protected] or share your thoughts on this article at digitaleng.news/facebook.
Follow DE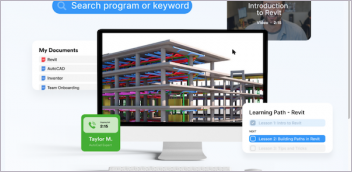

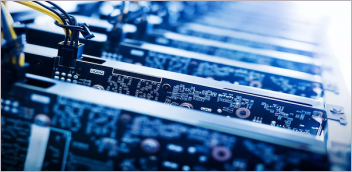
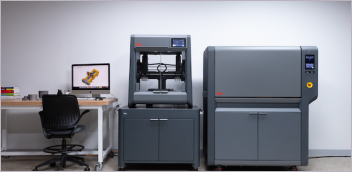