
CONVERGE CFD can help analyze valvetrain components and optimize them for specific NASCAR applications. Image courtesy of Convergent Science Inc.
Latest News
July 1, 2015

When an engine specialist as experienced as Brian Kurn is excited about a technology, others in the field tend to take notice. If they don’t, they should.
Kurn is currently in charge of Valvetrain Development together with all Virtual Prototyping technologies, including Engine and Valvetrain Simulation, as well as CFD (computational fluid dynamics) at ECR Engines, a division of Richard Childress Racing. In a career spanning 25 years he has worked for some of the biggest names in the sport, including Roush Fenway Racing, Hendrick Motorsports and with Bill Davis Racing. Kurn started his craft building and improving V8 engines for the small dirt tracks and worked his way up to the elite series in NASCAR. He was highly regarded for his work on cylinder heads and his ability to extract more power whilst retaining crucial reliability. Today, he’s an engine developer who has worked successfully across many racing formulae – Tudor Sportscar Championship, NHRA Pro Stock, American Le Mans Series (ALMS), Touring Cars in Brazil and Argentina, Truck-pulling, Supercross and, of course, NASCAR.
“In the ‘good old days’, so-called tuners determined the biggest valves that could be used and then they simply began to hand-port the head, believing that the more air that would flow, the more power it should make,” says Kurn.
“After spending a lot of time doing this, you took the parts to the dyno and only then did you find out if you had found a solution or just scrapped another cylinder head! It was an expensive and time-consuming way to see if your idea gained a few horsepower or not. And each time you got a new head design, you really had to start again,” he says. It was this inefficiency that drove the Kurn to investigate simulation technologies.
As an experienced CFD user, primarily to analyze internal flows in the engine, both stand-alone and coupled with engine simulation, Kurn is at home with state-of-the-art technology. But just over a decade ago, CFD posed problems. “The run-times to do the simulations took too long and when we had to create our own mesh, we really suffered with the variability between users,” says Kurn. “It can affect your results, introduce inconsistency and ultimately your trust in the data can go out of the window.”
Mix and Mesh
Even today, creating a good mesh is crucial to resolve the flow. But the quest for an automatically generated mesh never quite delivered the accuracy needed to move away from user-generated data. For years, engineers simply accepted the challenges and did what little they could to minimise the variations.
For Kurn, it was a frustration. “I never believed that an effective automatic meshing tool would happen in my lifetime. I thought we would be stuck with the longer run-times forever,” he says. But after learning that CONVERGE had collaborated with engine simulation provider Gamma Technologies, everything changed.
It was there Kurn first encountered an innovative automatic meshing solution called CONVERGE CFD Software. Developed by Madison, WI, firm Convergent Science Inc., it automates the meshing at run time with a perfectly orthogonal Cartesian mesh that eliminates the need for a user-defined mesh.
“To be honest, I’d heard it all before and I was skeptical,” says Kurn. “Automatic meshing had been around for long time but none of the solutions I tried lived up to their claims of a completely automatic mesh that produced accurate results. But if the guys at Gamma were convinced CONVERGE was different then maybe I should take a look. I’d always struggled with meshing, and longed for the day when I wouldn’t’t have to predict the outcome in order to define the mesh, and I didn’t want my meshing to affect the result. I ended up taking a look and the rest is history.”
Cuts Time First and Material Later
Written by engine simulation experts to address the deficiencies of other CFD codes, CONVERGE offers run-time grid generation and refinement so users such as Kurn no longer need to spend their time creating meshes.
Instead, the user supplies a triangulated surface and a series of guidelines from which the CONVERGE proprietary code creates the grid at run-time. “They had hit on my objective; reduce the run-time whilst retaining the accuracy of the simulation, removing assumptions.” says Kurn. “Testing would become more fruitful as with consistent meshing and we could test more solutions in the same timeframe. Once you have the model you can keep re-running the job without recreating the case.”

For race teams, the software achieves the one thing that is hard to buy – more time – and Kurn has been astounded with the amount he’s saved. “We gained literally weeks on some developments in 2014,” he says. “On our Daytona Prototype engine we got ahead of the development schedule and we were able to start testing different trumpet lengths before the engine was even ready to run on the dyno, or got anywhere near the car. This saved not only time but also the number of prototype parts produced. Knowing the exact parameters of key items such as combustion chamber, intake and exhaust ports means now when we make changes, we can accurately measure just those changes and have complete control over them. We now run a number of simulations and with the accurate data generated can confidently pick the best one or two to try on the car.”
Predictable Combustion
Trumpet design is just one of the areas that Kurn is using CONVERGE. Others include the combustion modeling and he sees the potential for using CONVERGE for optimizing future fuel efficiency.
“Our Genetic Algorithim Optimisation can run cases depending on design parameters such as fuel efficiency or power and think outside the box,” says “Our creators came from engine simulation and struggled with CFD meshing in the early years. They focused on creating a tool that would simplify meshing and increase accuracy. To achieve this they allowed the program to automate the mesh at run-time and automatically refine when and where it is needed through Adaptive Mesh Refinement (AMR),” says Rob Kaczmarek, marketing director for Convergent Science.
In-cylinder flame propagation is another common area of interest where AMR works particularly well. Kaczmarek believes non-CONVERGE users really struggle with hard-to-define areas like this.
“It leads them to either go to a larger-sized mesh, maybe up to 1mm in order to save time but losing accuracy, or go to a smaller mesh increasing the accuracy but also increasing run-times,” says Kaczmarek.
The good news is CONVERGE can take care of this, allowing the program to refine the mesh when and where it is needed at run-time for more accuracy all while keeping run times manageable. In addition, the software also comes equipped with detailed chemistry and physical models to help engineers make the gains they want.
“For example, measuring turbulence of a flame in microseconds and how it changes is very hard to do but crucial for efficiency,” says Kaczmarek. “CONVERGE can help. It’s great for transients and we saw, for example, with the use of direct injection in Daytona Prototypes and other high pressure scenarios, CONVERGE is very effective. Even though NASCAR engines have been around for a long time, well over 40 years, some of the best tuners who think they have understood them can now really see and truly understand what is actually happening for the first time.”
Doing that work on track rather than in the garage is another area where fast and accurate simulation is helping Kurn and ECR. He believes that a NASCAR pushrod engine is probably one of the worst-case scenarios for different behaviors when fired up. “The actual exhaust valve opening can be delayed as much as 10-15 crank degrees as a result of the cylinder pressure acting on the valves,” he explains. “Using trusted valvetrain simulation, we can now optimize the design of the valve train components to work in the real world, even in a NASCAR application.”
Simplicity and Support
Virtual testing is currently unrestricted in NASCAR and is becoming more popular as teams look for the edge over the others. “Track testing, save for the odd tire test, is zero!” says Kurn.
Despite half the teams having simulation tools, he’s unsure how many are actually using them effectively. The simplicity of CONVERGE leads him to believe anybody with CFD experience could use it and within 10 minutes can get a surface modeled.
“I have found CONVERGE to be one of the simplest and most powerful sim-tools out there. Also, we can pick up the phone with any questions and together we have worked to provide answers to many issues. I can’t fault the CONVERGE guys’ support.”
Tracking the Results
Kurn’s motorsport experience is second to none, but it is results on track that define success. CONVERGE was used effectively to make significant gains in power in 2014. These leaps in performance helped Richard Childress Racing secure second overall in the Sprint Cup Series Championship standings with Ryan Newman. Over 23 top 10 finishes resulted in Brian Scott snatching fourth in the Xfinity championship with Ty Dillon gaining a rookie victory at Indianapolis and fifth overall. Teammate Brendan Gaughan showed the versatility of the team’s development, winning on the traditional Road America circuit. ECR’s engines proved crucial in the Tudor Sportscar Series, helping Chevrolet to win the Tudor and Endurance Cup titles. Action Express’ DP car with an ECR engine scored eight podiums including three victories, most notably the Daytona 24 Hours. The ECR engine had reliability too, with the car completing every lap of competition throughout the season. “It was a special year for Kurn and the ECR team,” says Kaczmarek. “We are so proud to have been involved with the team and Brian.”
More Info:
Subscribe to our FREE magazine,
FREE email newsletters or both!Latest News
About the Author

DE’s editors contribute news and new product announcements to Digital Engineering.
Press releases may be sent to them via [email protected].
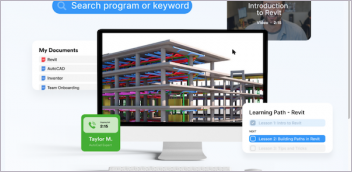

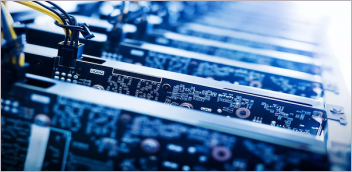
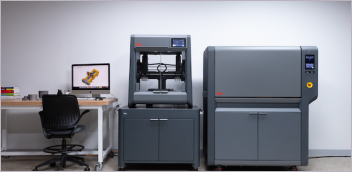