Planning Your Company’s Future with Mechanical Analysis
Computer-aided engineering products save money on physical testing and get designers closer to an optimized design.
Latest News
December 1, 2008
By L. Stephen Wolfe
![]() A soil excavation simulation created using the Coupled Eulerian-Lagrangian capability in Abaqus. (Image courtesy of Dassault Systemes SIMULIA.) |
Mechanical analysis saves money by reducing the amounts engineers spend on physical testing. Analysis also provides insight into the physics that influence products. While a physical test may enable engineers to know the strains or temperatures measured at a few discrete points on a prototype, a computer simulation can enable engineers to visualize the distribution of temperatures or stresses throughout a product, enabling them to better understand how design changes might reduce weight or improve performance.
Industry spends $2 billion annually on mechanical computer-aided engineering (MCAE) software, according to a July 2008 white paper by Cyon Research Corporation titled, “Classes of MCAE Software: Clarifying the Market.” Put in context, that sum is almost as much as engineers spend on software from CAD giant Autodesk, maker of the popular AutoCAD. The amounts spent on MCAE software are likely to continue growing for the foreseeable future as low-cost computers become more powerful, software becomes easier to use, and the number of engineers familiar with MCAE software continues to rise.
For every dollar spent on MCAE software, industry spends an order of magnitude more on the salaries, benefits, and overhead of engineers who use it. With this much money changing hands, firms that are not yet using mechanical analysis are starting to wonder how they can employ it. Those who have used it for decades are asking how they might use it more effectively.
Among the challenges faced by experienced CAE customers are creating analytical models in less time and with less labor. With many of the tools currently in use, CAD models must be translated into a form that can be read by analytical software. The imported geometry must be simplified to remove unwanted detail. Then a finite-element or finite-volume mesh is applied to the model. Loads and boundary conditions are applied, and the simulation is run. If a designer makes a change to the model before the analysis is finished, analytical models must be recreated.
CAE software makers are trying a number of approaches to make this process more efficient. The leading makers of 3D CAD software, including Dassault Systemes, Siemens PLM Software, Parametric Technology, and Autodesk are offering analysis programs that operate directly on native CAD geometry from within their CAD user-interfaces. A radically different approach taken by companies such as MSC.Software and Comet Solutions attempts to associate abstract analytical models with classes of CAD products so that designers can choose an appropriate template for their analysis and quickly apply it to a specific design.
![]() Stress analysis performed with ALGOR’s FEMPRO of a vertebral disc replacement device mounted in a spinal column. Image courtesy of Saba Metallurgical and Spinal USA. |
A second challenge for experienced analysts is solving problems where multiple types of physical phenomena interact. For example, the pressure exerted by a fluid flowing over an airfoil causes it to deflect, which alters the geometry of the fluid flow and changes the pressure distribution. Problems involving plastic deformation, such as simulating automobile crash tests, require periodic re-meshing of geometry as it deforms. Analysts would like to be able to automate these and similar processes that require multiple iterations so that less human intervention is required.
A third challenge for experienced analysts is managing the large volumes of data generated by their analyses. Many analytical studies may be applied to a single product model. Engineers want to be notified when changes to the product model require physical simulations to be re-run. Engineers are also struggling with how much analytical data they should keep about each product version and how to retrieve it if product reliability issues arise. Should they keep every model, load case, and set of results? Or should they only retain the results and recommendations made because of them?
Engineers who are new to CAE software will eventually have to wrestle with the problems of experienced analysts. But at first their problems will be more basic. These include deciding which problems could benefit from mechanical analysis and simulation, choosing the right software for their problems, and training engineers and designers how to use the new tools. They also need to think about how to coordinate the results of analytical modeling with physical testing to validate the assumptions that underlie computer models.
Firms new to CAE will probably want to start with analytical codes that are integrated with their CAD programs. These products are easier to use and less costly than software that’s designed for full-time analysts. However, they may lack the sophisticated functions needed to solve hard problems. When your organization’s needs outrun the capabilities of these products, you’ll have a better idea of the features you’ll want when trading up.
According to Cyon Research, the top eight CAE firms garner 65 percent of worldwide CAE revenues. The rest is divided among several hundred companies. CAE software is a profitable business in part because the market-leading companies charge high prices. Smaller firms with lower overheads can prosper in this field, especially if they can solve specialized high-value problems efficiently.
Here is a brief description of some of the leading CAE software companies and a few smaller firms that have general-purpose products. However, don’t limit your search to these few if you need specialized software for simulating the likes of molding or stamping processes, optics, fluid dynamics, radiant heat transfer, or electric fields.
ALGOR, Inc.
Privately held ALGOR sells a variety of moderately priced analysis products based on the finite-element method. Although Algor’s products are independent of any CAD system, they can read data from most of them.
ANSYS, Inc.
With annual revenues exceeding $400 million, ANSYS offers the broadest suite of mechanical analysis software of any company. The firm was originally founded as Swanson Analysis Systems and renamed after its flagship finite-element-analysis (FEA) solver upon the retirement of its founder, John Swanson. Its current chief executive, Jim Cashman, has tripled the company’s revenues in the past five years by buying smaller makers of analysis software and adding their products to ANSYS’ lineup. In 2006, ANSYS acquired privately held Fluent, the largest maker of computational fluid dynamics (CFD) software. ANSYS products are generally well regarded by the professional analysts who use them and are sold through a network of independent resellers who themselves offer analytical services as well as software.
![]() Static analysis template for a car door being created with MSC.Software’s SimXpert Template Builder. Image courtesy of MSC.Software. |
Altair Engineering
With sales of $140 million, privately held Altair Engineering garners roughly the same revenue from analysis software as Siemens PLM Solutions. Altair’s Hyperworks is used primarily in the automobile industry to simulate vehicle structures. The software includes a complete set of tools for finite-element model building, solving, and displaying of results. Hyperworks also can be used with other companies’ solution software, such as Nastran. Optistruct is a unique component of the Hyperworks tool kit that synthesizes thin-shell structures to carry specified loads.
Autodesk
Autodesk is the largest CAD company measured by revenues, profits, and unit sales, but its presence in the mechanical analysis market remains modest. Autodesk currently offers an extra-cost finite-element modeling option — based on ANSYS — with its Inventor CAD software. The Inventor 2009 version of this product is so limited in its capabilities that it might be worth waiting for the next version of this option. In 2007, Autodesk acquired PlassoTech, a privately held maker of FEA software and Autodesk plans to integrate this product with Inventor, possibly by the 2010 version. At that time, Inventor customers seeking integrated FEA should take another look.
In 2008, Autodesk bought Moldflow, the leading maker of software for simulation of injection-mold filling and cooling. The purchase added $58 million to Autodesk’s manufacturing sector revenues, according to Cyon Research estimates. Moldflow comes in three forms: a stand-alone version for professional analysts called Plastics Insight, the Part Advisor that is integrated with some CAD packages and is intended for plastic part designers, and the Mold Advisor that analyzes gates and runners for mold designers. The Part Advisor is not yet a standard feature of an Inventor CAD package. Representatives have said Autodesk plans to discontinue support for Moldflow products integrated with SolidWorks.
CD-adapco
This privately held company’s Star brand of computational fluid dynamics software competes with the former Fluent line now owned by ANSYS. STAR-CD is the stand-alone professional version used by specialists who tackle the toughest problems including combustion, phase changes, fluid-structure interaction, and complex geometry. The STAR-CAD series is simpler and easier to use and is integrated with popular CAD systems including CATIA V5, SolidWorks, Siemens NX, and Pro/ENGINEER. A company spokesperson said CD-adapco’s annual revenues are approximately $90 million, including software and services.
Comet Solutions
If you’re intrigued by MSC.Software’s concept of expert-driven analysis that designers can use, but can’t afford MSC.Software’s prices, there’s an alternative. Privately held Comet Solutions sells software based on what it calls an “abstract engineering model” that lets customers give designers customized templates instead of general-purpose FEA tools.
COMSOL
Founded in Sweden, COMSOL published the first version of its flagship Multiphysics software in 1998. As its name implies, COMSOL Multiphysics is intended for simulating systems where two physical phenomena that are normally analyzed separately interact. Examples include flexible structures that are affected by fluid flow, electromagnetic forces, high temperature gradients, or acoustic fields. Optional Multiphysics modules are sold separately to simulate various types of physical behavior.
Dassault Systemes
This giant in the CAD field doesn’t break out its sales of CAE software, but Cyon Research estimates them to be about $250 million. Dassault sells analytical software under two brands: SolidWorks and Simulia. The Simulia brand was formed by combining the analytical software that is integrated with Dassault’s flagship CATIA CAD system with the stand-alone Abaqus software acquired in 2005. Abaqus is a highly respected non-linear finite-element-analysis solver that comes with stand-alone tools for model building and displaying results. It is widely used to simulate non-linear plastic deformation and non-linear materials such as biological tissue.
![]() New solver technology allows LMS Virtual.Lab Acoustics to perform a full vehicle acoustic analysis. Image courtesy of LMS International. |
LMS International
Best known for its software to gather, organize, and display complex test results, LMS International also sells $55 million worth of mechanical analysis software and services annually, according to a company representative. The unique strength of LMS’ Virtual.Lab software is its ability to combine theoretical models based on finite-element analysis and rigid-body dynamics with empirically derived test models to predict the behavior of new product variants.
MSC.Software
MSC.Software is the oldest existing company in the commercial engineering software field. It was once the largest seller of CAE software, but a series of missteps by various chief executives have reduced it to a distant second with 12-month trailing revenues of $253 million. Under a new executive team from the former Structural Dynamics Research Corporation (SDRC), MSC.Software has embarked on a new strategy to sell complex and sophisticated analytical systems to large corporations.
Its newly developing products include SimManager, software for storing and organizing analytical models, processes, and results; SimXpert, a set of tools that allows expert analysts to set up generic templates so designers can simulate the performance of specific classes of products; SimDesigner, a finite-element modeling tool that integrates with 3D CAD software; and MD Solutions, a suite of tools that encapsulates various analytical solvers (Nastran, Marc, Dytran, and Adams) under a common data environment.
MSC.Software’s new line has been slow to catch on with customers. If the company can get it working properly, it could regain industry leadership by offering the largest and most sophisticated manufacturers a unique set of integrated tools. For now, however, MSC.Software’s new products are best suited to large firms with deep pockets and the patience to work with their software supplier for the long term.
NEi Software
Formerly called Noran Engineering, this company sells an affordable version of the popular Nastran finite-element analysis solver. For FE modeling and results display, NEi offers the stand- alone NEi Fusion for designers, a Gold Partner integrated version, NEiWorks, for SolidWorks customers, and Siemens Femap for professional analysts. NEi also sells a variety of third-party analysis software including CFD, aircraft structures, rigid-body dynamics, acoustics, and optimization.
![]() Comet Workspace automates a complex multiphysics simulation for an aerospace telescope. Image courtesy of Comet Solutions. |
Siemens PLM Software
Siemens acquired UGS PLM Solutions from private investors in 2007. The company was formed by Electronic Data Systems in 2001 by combining its Unigraphics business with Structural Dynamics Research Corporation (SDRC). SDRC brought to the marriage a rich line of mechanical analysis software that complemented Unigraphics’ thin analytical tool set. In 2006, UGS obtained a source license for MSC.Software’s flagship Nastran solver as part of an anti-trust settlement. Today, Siemens offers a broad line of analytical software that competes on many fronts with ANSYS and MSC.Software. One popular, moderately priced application called Femap for finite-element modeling and results display is sold though independent dealers and works with a variety of FEA solvers. As part of a much larger CAD company, Siemens products appeal primarily to users of its CAD software: NX, I-DEAS, and Solid Edge. Cyon Research estimates that annual revenues of Siemens analytical software business are between $120 and $150 million.
SolidWorks
SolidWorks’ analysis software was originally developed by Structural Research and Analysis Corporation (SRAC) and marketed under the Cosmos brand. Dassault Systèmes acquired SRAC in 2002. With SolidWorks 2009, the Cosmos moniker has been phased out and henceforth the SolidWorks Simulation software will be sold only in packages integrated with SolidWorks. SolidWorks Simulation is intended for engineers who are not FEA or CFD specialists, and the 2009 version comes with a variety of software advisors to guide inexperience users.
More Info:
ALGOR
Pittsburgh,PA
ANSYS, Inc.
Southpointe,PA
Altair Engineering, Inc.
Troy, MI
Autodesk, Inc.
San Rafael,CA
CD-adapco
London, UK
Comet Solutions
Albuquerque,NM
COMSOL
Burlington,MA
Cyon Research Corporation
Bethesda,MD
Dassault Systemes
Paris, France
LMS International
Leuven, Belgium
MSC.Software
Santa Ana,CA
NEi Software
Westminster,CA
Siemens PLM Software
Plano, TX
SolidWorks
Concord,MA
L. Stephen Wolfe, P.E., is a senior analyst of Cyon Research Corporation based in San Diego and is founder and publisher of Computer Aided Design Report and the Product Data Management Report (now CADCAMNet). He has written about CAD and engineering software since 1981 and consults in the mechanical engineering software field. Please send comments about this article to [email protected]. You can also contact Stephen at [email protected].
Subscribe to our FREE magazine,
FREE email newsletters or both!Latest News
About the Author

DE’s editors contribute news and new product announcements to Digital Engineering.
Press releases may be sent to them via [email protected].
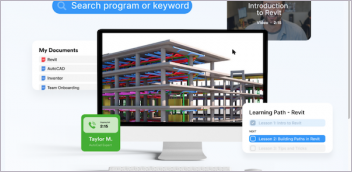

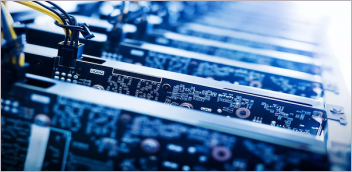
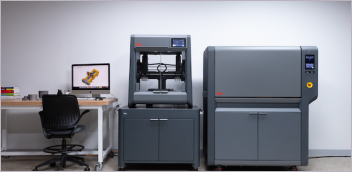