New Print Method Boosts Composites Strength

Latest News
February 6, 2018
Researchers at the Harvard John A. Paulson School of Engineering and Applied Sciences (SEAS) have developed a new 3D printing method that allows control of arrangement of short fibers embedded in a polymer. By programming the fiber orientation in epoxy composites, they were able to create materials that could be optimized for strength, stiffness and other characteristics.
The new rotational 3D printing approach allows for 3D printing of materials that “can be spatially programmed to achieve specific performance goals.” Damage tolerance, for example, could be optimized in specific areas that are expected to undergo stress.
While there are other methods that can orient fibers in composites using 3D printing, they typically generate uniform fiber alignment and can complicate the printing process. The Harvard team has decoupled fiber orientation from the print path using a rotational printhead that also generates a shear field as the ink is deposited.
According to the researchers: “Specifically, fibers can be locally reoriented as the ink exits the nozzle without requiring any coupling to external acoustic, magnetic, or electrical fields.”
“Rotational 3D printing can be used to achieve optimal, or near optimal, fiber arrangements at every location in the printed part, resulting in higher strength and stiffness with less material,” said Brett Compton, co-author of the research who is now an assistant professor in mechanical engineering at the University of Tennessee, Knoxville. “Rather than using magnetic or electric fields to orient fibers, we control the flow of the viscous ink itself to impart the desired fiber orientation.”
“Being able to locally control fiber orientation within engineered composites has been a grand challenge,” said senior author Jennifer A. Lewis, Hansjorg Wyss Professor of Biologically Inspired Engineering at Harvard SEAS and founder of Voxel8. “We can now pattern materials in a hierarchical manner, akin to the way that nature builds.”
The team published their results in the journal PNAS. The method an be used with any material extrusion printing system using any type of filler material.
Source: Harvard
Subscribe to our FREE magazine,
FREE email newsletters or both!Latest News
About the Author

Brian Albright is the editorial director of Digital Engineering. Contact him at [email protected].
Follow DE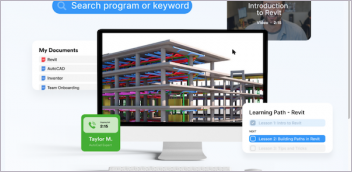

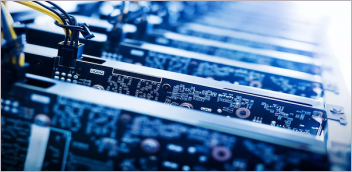
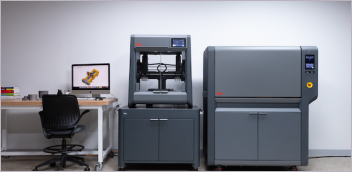