LightSPEE3D Metal 3D-Printer Applies Supersonic Deposition Technology

LightSPEE3D is the world’s first metal 3D-printer that leverages supersonic 3D deposition (SP3D) technology. (Image courtesy SPEE3D)
Latest News
November 7, 2017
Just when you think the world has seen all possible approaches to layer-by-layer manufacturing, along comes another cool technology, this time from a new company: SPEE3D of Melbourne, Australia. Based on a process called supersonic 3D powder deposition (SP3D), its LightSPEE3D system builds fully dense, casting-grade parts in minutes, not hours. I saw this equipment in action via webcam, and the speed was eye-opening.

SPEE3D will debut its printer next week at formnext powered by TCT, the international AM conference and exhibit on advanced manufacturing, now in its third year. Currently the company is focusing its efforts on aluminum, though it has also produced parts in copper and additional materials are in development. SPEE3D’s business model targets the automotive and aerospace markets, for medium-volume parts (e.g., cam rods and manifolds) in quantities up to 10,000.
Seeing a Need, Tailoring a 3D-Printed Solution
Byron Kennedy, CEO of SPEE3D, understands how to start up and manage manufacturing businesses, having done so for more than a decade in the field of high-efficiency electric motors. He knows that cost, speed and repeatability are key to commercial part production, so some years ago he started looking to additive manufacturing (AM) processes to evaluate their viability. As an alternative to traditional methods, AM clearly produced quality parts but at costs and rates that provided little industrial advantage in commodity metals. However, the concept was intriguing.Along with co-founder and CTO Steve Camilleri, Kennedy researched other technologies that could offer cost-effective, scalable, just-in-time parts production. “SPEE3D was born of the frustration that 3D-printing offers lots of advantages but the reality is, it isn’t going to cut it in the real world,“Kennedy says. “Today’s ‘fast printing’ really takes 10 to 12 hours.” The two soon realized the answer lay in combining the versatility of 6-axis robotics (currently an ABB robotic arm system) with the speed of supersonic powder deposition (based on cold spray technology).
Typically used for part repair and coating, a cold spray system operates below the melting point of the metal in use. Combining high-pressure carrier gas with metal powders, the process uses principles of rocket design to accelerate the particles through a small nozzle, achieving a thin flow stream at supersonic velocity. Particles deform plastically upon impact on a target, with particles adhering layer by layer through mechanical interlocking and metallurgical bonding. Advantages include high density of the deposits (>98%) and low residual stresses.

“The U.S. Army, for example, uses cold spray to repair very expensive items such as a helicopter gearbox that has corroded,” explains Kennedy. “They remove any corrosion, spray metal on it, and put it back into service.” It seemed natural to Kennedy and Camilleri to apply this technique to producing complete parts, and so work on the LightSPEE3D began.
Although not the first company to investigate a cold spray approach for AM applications (companies such as TWI and Centerline’s Supersonic Spray Technologies Division come to mind), SPEE3D has brought what appears to be the first such system for complete part-production to market.
The LightSPEE3D rocket nozzle, which is stationary in the base of the enclosed unit and aimed vertically, “fires” metal particles at 1,000 meters-per-second (three times the speed of sound) at the moveable build plate. Facing the nozzle, this build-plate is mounted on the end of a robotic arm and moves with six degrees of freedom while the part builds upside down. This first model of the LightSPEE3D can create parts that weigh approximately 10 pounds and are about 6 inches across; if larger, heavier parts are required, the technology can be scaled up with a larger robot arm.
How fast is fast? The part I saw built — a solid aluminum cylinder about 2 inches in diameter and 3 inches long — was fabricated in just about 20 minutes, and ready for the exact same post-build machining steps required by any other casting. The company has hundreds of sample parts that display the system’s range of capabilities and speed. For example, it only took about one-and-a-half minutes to build a small copper heat sink.
Robot Controls and Touch Input

Having the part itself manipulated during the build eliminates the typical geometry-based requirement for support structures. Likewise, operating well below melt-temperatures avoids the need to incorporate additional segments solely as heat-transfer paths between the part and the build-plate. The entire system operates at room temperature and with a regular air environment, eliminating the need for hours of cool-down or the expense of supplying and regulating specialized gasses.
“It’s all about driving costs down,” says Kennedy. The system uses ordinary metal powders — not even metal injection molding (MIM) types, let alone the highly refined powders required by some metal AM equipment. However, he notes, “The real advance that we’ve brought to the table is the software to install the robot and to build the parts. We first take the STL (3D model) file and simulate the part to see if there are issues. Then we take that back to the customer, agree on any changes, send that software to the robot feed and build the part.”
Another factor the company made sure to address was user-friendliness. The design of the dual-screen user-interface is actually based on proven gaming interface designs. (Watch their cool demo video of building the head of a golf putter below.)
Kennedy sees LightSPEE3D as being a good fit for mid-volume automotive and aerospace applications, both for evaluating a new part-design before investing in tooling (e.g., supplying a 1,000 parts for trial runs), or doing a complete lot of 10,000 for a specialty vehicle model. SPEE3D’s vision for efficiency and just-in-time production may be the perfect match for your production needs.
Subscribe to our FREE magazine,
FREE email newsletters or both!Latest News
About the Author

Pamela Waterman worked as Digital Engineering’s contributing editor for two decades. Contact her via .(JavaScript must be enabled to view this email address).
Follow DE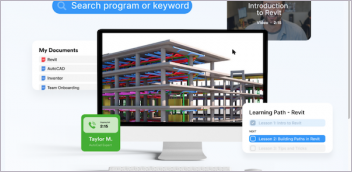

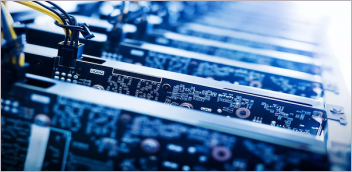
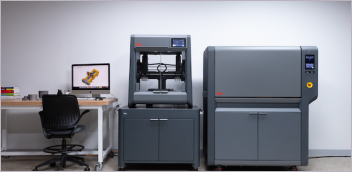