Kicking the Tires on Digital Twins
The benefits of virtual representations of individual physical assets aren’t just for large enterprises.

Digital twins are increasingly important to automakers and other large enterprises, but SMBs can make use of them as well. Image courtesy of PTC.
Latest News
May 1, 2019
Imagine designing a wearable device that reports your heart rate and blood pressure to your cardiologist. How about cement that warns hydroelectric dam operators of increased stress levels, a robot that lets the maintenance crew know when they should order a replacement servo motor or a shopping cart that reads the grocery list on your smartphone and helps you find the canned peas?
Welcome to the Internet of Things (IoT). Anyone who’s read about it has already heard about these intriguing possibilities, but what they might have missed is how IoT sensor data from planes, trains and automobiles can be applied to digital replicas of these objects, then used to predict and improve their performance.
“Digital twins are not an all-or-nothing proposition. Practically speaking, you only need subsets of relevant information to drive initial use cases, not thousands of data points.”
It’s called a digital twin, and whether your company has 10 employees or 10,000, think of a digital twin as a living, breathing, but entirely virtual, replica of a manufactured product. It could be one of the products just mentioned, or it could be some widget that a startup company like yours has recently developed, one that will surely leapfrog the competition if you can collect accurate, real-time usage data.
Whatever the case and whatever the scale, digital twins allow designers to collect and analyze data from their “as-manufactured” products and compare to their “as-designed” 3D models. Properly implemented, digital twins provide a wealth of information: predictive maintenance becomes more predictable, product safety and durability improve and development costs go down. And one day soon, digital twins will be as common as CAD models, without which no company large or small can long survive.
But What Exactly is a Twin?
Unfortunately, the term digital twin is still nebulous, especially to small- to medium-sized businesses (SMBs) who don’t have fleets of technical experts around to explain what it is and how to leverage it. One definition comes from Deloitte Consulting LLP, which in a recent white paper described digital twins as “an evolving digital profile of the historical and current behavior of a physical object or process that helps optimize business performance.”
Aaron Parrott, a managing director with Deloitte Consulting LLP’s Supply Chain and Network Operations practice, says digital twins can “simulate specific complex deployed assets such as jet engines and large mining trucks in order to monitor and evaluate wear and tear and specific kinds of stress as the asset is used in the field,” adding that the information gleaned from these and other digital twins will almost certainly affect future product designs by providing hitherto unavailable insights into their performance in the field.
Yet Rahul Garg, vice president of mid-market at Siemens PLM Software, offers a broader, three-pronged definition. “We like to think of the digital twin in holistic terms,” he says. “From the design perspective, a digital twin assures that all of your analysis, simulation, prototyping and testing can be done digitally, streamlining the entire engineering process. Then there’s the digital twin for production, which allows manufacturers to evaluate and manage all of their different processes, quite possibly using factory floor data to improve product design. And of course there’s the more classical definition of digital twinning, where IoT-based technologies are used to provide performance data from the field.”
Closing the Loop
Garg says this third version of the digital twin can generate significant advantages to companies that wish to increase proactive maintenance activities, because historical tracking of performance data from the pumps, motors, controllers and other components found in a typical mechanical assembly—especially when collated across hundreds or thousands of such assemblies—provides a fairly reliable prediction of future performance. When that same data is applied to the digital twin, however, the advantages exponentially grow.
“You also have to consider solutions like virtual commissioning, which make it very easy to develop and evaluate the automation model, the electrical model and the physical and kinematic model as a digital twin, and ensure that when you build the real machine, it will behave and function like its digital twin,” Garg says. “The result is an iterative loop of continuous improvement, not only of the product itself, but of the manufacturing processes associated with it. This is what makes the digital twin truly transformative.”
For an SMB concerned about securing funds or hitting the next project milestone, all this talk of feedback loops and business transformation might seem overwhelming. Yet Dave Duncan, vice-president of PLM and connected engineering at PTC, explains that a digital twin initiative doesn’t have to be difficult.
“Digital twins are not an all-or-nothing proposition,” Duncan says. “Practically speaking, you only need subsets of relevant information to drive initial use cases, not thousands of data points.
“For instance, you don’t need machine-based sensors or even a whole lot of technical sophistication to collect the ‘as-built’ bill of materials from the production floor, and electronically tie that to the upstream CAD/eBOM (engineering bill of materials) definitions for use as a reasonable approximation of the fielded asset configuration. You can drive a lot of enterprise change planning, closed-loop quality and data-driven design use cases from this fast starting point. This is a simple but useful example of digital twinning, incepting a program that can build upon over time as business systems and connected product data improve.”
Stuck in the Middle
But perhaps you don’t have a production floor. Many SMBs subcontract their manufacturing to others, and then sell their wares to service providers or original equipment manufacturers, who then assemble those products into an appliance or motorized vehicle of some kind. What opportunities do digital twins offer to those stuck in the middle?
Duncan says end-use data collection can be challenging for these companies, but that mechanisms can and should be introduced during the design phase to assure that information is shared in both directions. Subcontractors must be willing to provide manufacturing data such as material specifications and test results for inclusion in the product designer’s digital twin. And provided the product is equipped with wireless sensors and has regular access to the internet (a basic tenet of the IoT), feeding performance data back to the designer should be no big deal—however, it often is.
For example, an automobile should be a perfect scenario for the digital twin today, says Duncan. However, vehicle service is typically provided by independent vendors, so it can be difficult to get relevant data back from the equipment owners or the car dealers.
“This is changing over time as manufacturers offer more services to subscribe product connectivity with their value chains,” Duncan adds. “A well-known example is Tesla’s over-the-air update program that delights their customers—most voluntarily subscribe. Programs like this that offer capability, convenience or risk share to the downstream value chain are enhancing digital twins for the manufacturers.”
On the Factory Floor
This situation will obviously change as the manufacturing industry embraces and then insists upon compliance, but in the meantime, there remain plenty of opportunities for SMBs of all stripes to leverage the digital twin.
“It could be something as simple as a toolpath simulation, where machining data can then be tied to the digital twin for performance analyses,” says Al Whatmough, CAM product manager at Autodesk. “On the other end of the spectrum, there’s digital twinning of the factory floor, which gives industrial or manufacturing engineers greater ability to optimize their entire operation.”
Sanjay Thakore, business strategy manager at Autodesk agrees, although he’s quick to point out that the latter of these two examples is generally not found in an SMB. “Large-scale models of factory layouts like these are typically more prevalent in enterprise-class businesses, where they have teams dedicated to modeling the factory and all its equipment, and the ability to install sensors wherever they’re needed,” he says.
Looking Ahead with AI
Does that mean SMBs should hold off on a digital twin initiative? Not at all. Breaking down such initiatives into smaller incremental goals is a good starting place, Thakore suggests. Examples could be eliminating manual programming of computer numerical control machines or digitizing factory floor processes.
Once in a digital environment you can begin comparing post-manufacturing data to what the software initially predicted and create feedback loops—a product lifecycle management (PLM) system might reference various aspects of a digital twin’s history, while artificial intelligence (AI) could analyze this and other parts of the digital twin to predict when and how a product will fare years from now.
Partly due to increasingly affordable cloud computing and software as a service (SaaS), Thakore explains, these tools and more are available to even the smallest small business, making some level of digital twinning a possibility for all. “Whatever the company’s size, a digital twin environment promotes greater connectivity between the design team and the manufacturing floor,” he says. “Even though you might not be putting IoT-capable sensors in your products anytime soon, digital twins bring a lot of value to the table. There’s really no reason to wait.”
More Autodesk Coverage
More PTC Coverage
More Siemens Digital Industries Software Coverage
Subscribe to our FREE magazine,
FREE email newsletters or both!Latest News
About the Author

Kip Hanson writes about all things manufacturing. You can reach him at .(JavaScript must be enabled to view this email address).
Follow DE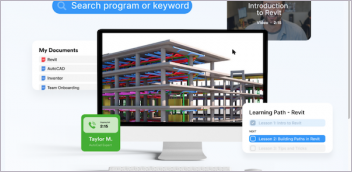

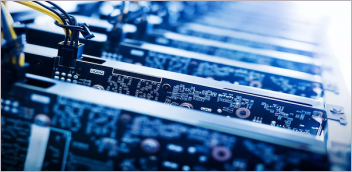
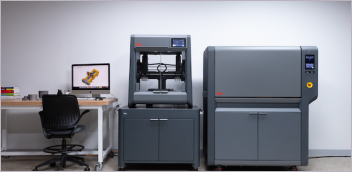