Latest News
May 2, 2009
By DE Editors
![]() Bob Williams, ALGOR |
In the early 1980s, CAE industry experts said FEA would never run on PCs. Yet, in 1984, ALGOR pioneered the first such comprehensive FEA system.
During the last two-and-a-half decades, the CAE industry has tried to keep pace with increasing computing capabilities to take best advantage of them. Today, PCs are routinely used for complex analyses such as motion-contact, CFD, and multiphysics.
Take a look at some recent software developments that have improved hardware support. Our customers report that 64-bit processing enables them to perform large-scale analyses that weren’t possible before. In one example, an engineer routinely meshes and analyzes models with approximately 2 million solid elements.
The solvers used by ALGOR analysis types have been developed using industry standards such as the OpenMP (open multiprocessing) application programming interface to support multicore parallel computing on HPC systems. This allows our solvers to take advantage of dual- and quad-core speed and positions us for newly released 6-core technology as well as future plans for 8-core processing and beyond.
We support distributed memory processing (using the industry-standard MPI) on a cluster of up to 32 computers. The user simply specifies a remote execution PC and a Windows or Linux computing cluster. Then, the sparse multifrontal massively parallel solver can be used to perform analyses across multiple machines.
And, finally, a current area of software development is aiming to take advantage of graphics processing technology. A GPU is a second processor in your PC dedicated to graphics, which offloads graphics processing from the CPU so the CPU can focus on primary system processing, thus promoting faster analysis solutions.
For FEA vendors, supporting the latest hardware advancements is essential for reaching CAE software’s ultimate concept: true virtual prototyping, where testing designs can be simulated as accurately as physical tests in a lab. In the future, a designer won’t need to know about FEA details such as types and meshes. Instead, the software will function as a “black box” virtual prototyping tool, requiring the user to simply describe physical characteristics of the product environment. The “black box” will then automatically handle setup and processing so the user can see how the product performs.
Already, CAE software is headed in this direction. Increasingly, entire CAD assemblies are used in simulations that include most or all of the environmental factors a product may experience. Growing computing power will continue to speed processing to enable users to see results in real time and focus on accurate representations.
This all leads to true virtual prototyping, where complex multiphysics can be solved and viewed in as close to real time as possible. And that can only be achieved if computer systems continue to become faster, more powerful, and better integrated. With the continuing development of HPC, we’re getting there.
That’s why it’s important for FEA users to keep up with growing computer capabilities. Older hardware can’t get you the full benefit of recent CAE software developments. Upgrading hardware can help maximize the return on your CAE software investment. Your simulations will run faster—and that speed means increased productivity. Furthermore, the closer you get to an “ideal” hardware setup for today’s CAE software, the more you can expand your simulation toolkit and take on more realistic and sophisticated simulations. We can provide the tools, but you need to make the commitment to incorporate them into your design process.
Bob Williams is the product manager for ALGOR. Send your feedback to [email protected].
Subscribe to our FREE magazine,
FREE email newsletters or both!Latest News
About the Author

DE’s editors contribute news and new product announcements to Digital Engineering.
Press releases may be sent to them via [email protected].
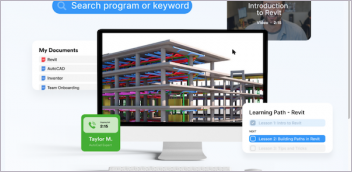

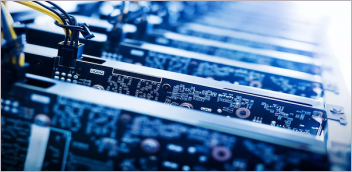
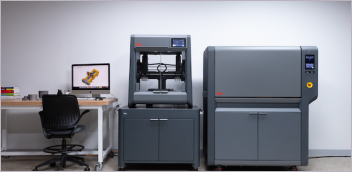