GibbsCAM Gives American Chopper Star the Speed to Beat His Deadlines
Paul Teutul Jr., star of TLC's "American Chopper," used GibbsCAM to machine bike parts in time for the Sturgis Rally.
Latest News
October 20, 2010
By DE Editors
Paul Teutul Jr., star of TLC’s reality TV show “American Chopper,” chose GibbsCAM in order to challenge his father’s shop in designing and building custom motorcycles for the fall season of the TV show.
![]() |
For the last six years, American Chopper has featured Orange County Choppers, the custom motorcycle builder co-founded by Paul Teutul, Sr. and Paul Teutul, Jr., who left the shop to start his own design firm, named Paul Jr. Designs. The fall season of American Chopper, titled “Senior vs. Junior,” will follow Paul Sr.‘s Orange County Choppers and Paul Jr. Designs, as the Teutuls challenge each other. Paul Jr. Designs planned to unveil two new motorcycles at the Sturgis Motorcycle Rally, so they had to meet that tight deadline as well as TLC’s shooting schedule.
“I don’t believe we would have met the Sturgis deadline—maybe not even our shooting schedule—without GibbsCAM,” says Teutul Jr. “With our committed schedule, we didn’t have the time or patience to learn some cumbersome CNC programming software. We had to be very selective in finding a CAM system with optimal capabilities and the ability to program anything we threw at it for our chosen CNC. That’s why we chose GibbsCAM, for its reliability and ease of use. Our machinist, Mark Harris, found GibbsCAM to be extremely flexible and easy to use, and we were really grateful for the terrific support that we received from the local Gibbs representative. We look forward to similar success using GibbCAM for other bike parts throughout the season, and for our future design projects.”
Paul Jr. Designs programs its Haas CNC machine, and its supplier’s CNC, with GibbsCAM. The first parts, which were required for the Sturgis Rally unveiling, were some twisting 3D “spider webs” to be mounted on a motorcycle’s wheels. The complex parts are not a typical first project for any CAM-system user, especially where introduction to the system was less than a month before the Sturgis deadline.
Programmer-machinist Mark Harris had eight days to model and machine six pieces, each composed of two different (front and back wheel) spider webs, in addition to modeling and machining other webbed trim parts and tending to other responsibilities.
“This was my first introduction to GibbsCAM,” he says, “and it’s incredibly easy to learn and much easier to use than the system I have used for years. The GibbsCAM modeler enabled us to make a machinable model with the flexibility required for easy modification, while the programming modules let us try different approaches to machining, which were required because the parts were a real challenge to machine.”
The “lace” of the spider webs is 3/8 in. thick. “The fragility made machining very time-consuming,” says Mark Harris. “We were fortunate to have that software for machinability. Modifying the front-wheel web to fit the rear wheel, without destroying the integrity of the design, was easier than anticipated. Any delay or difficulty would have prevented the unveiling at Sturgis.”
For more information, visit the GibbsCAM site.
Sources: Press materials received from the company and additional information gleaned from the company’s website.
Subscribe to our FREE magazine,
FREE email newsletters or both!Latest News
About the Author

DE’s editors contribute news and new product announcements to Digital Engineering.
Press releases may be sent to them via [email protected].
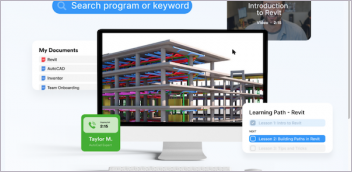

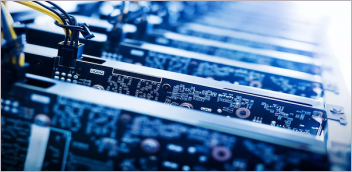
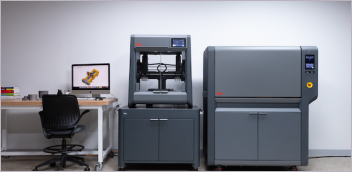