FreeForm Helps Build Wheels Fit for a Hamster
SensAble's sculptural MCAD system helps design innovative motorcycle parts in half the time.
Latest News
January 1, 2009
By Scotty Ziegler
![]() Scotty Ziegler’s TP-powered chopper includes a number of items designed using SensAble’s Free Form modeling system. The designer’s touches and a dramatic front end make it a true custom. |
My firm, Scotty of California, Inc., is a creative design company primarily involved in designing toys and consumer goods. But because of my predilection for motorcycles, we have a growing line of distinctive motorcycle parts and accessories ranging from saddlebags to gas tanks. This motorcycle focus evolved out of my lifelong love of bikes and membership in the Hamsters Motorcycle Club, an elite group of 300 custom bike riders. Membership in the club requires that you ride a highly customized American-made motorcycle.
When the Hamsters roll through the Sturgis (SD) Motorcycle Rally each August, jaws drop and activity stops in deference to these rolling works of art. The parade of colorful, highly sculpted motorcycles winding its way along Black Hills roads and up to Mt. Rushmore and back is a sight that defines the week-long rally for many enthusiasts.
As a Hamster, I thoroughly understand the motorcycle accessory business, and as a result I have won sought-after design projects for leading manufacturers such as Arlen Ness — a founder of the Hamsters — as well as the Indian and Iron Horse motorcycle companies. The 30th anniversary of the Hamster ride to Sturgis last summer was an opportunity to showcase our design innovation and potentially increase the motorcycle portion of our business.
![]() This bike’s air cleaner is seen in the FreeForm environment. Prototypes of the customizedparts were created in a Stratasys 3D printer. |
In keeping with the Hamster image, my bike is a full custom chopper built from the ground up — a 121 c.i. TP Engineering V-twin motor, custom frame, and a hand-built front end. When the bike needed a new air cleaner, no off-the-shelf part would do. Our team decided to reverse-engineer the stock part to keep the measurements and basic functionality intact and then design a unique, eye-catching cast-copper air cleaner that looked as sleek as the rest of the bike. It would also incorporate the 30th anniversary Hamsters ride logo in the cover.
Challenge 1: Efficiently Emboss The Logo
My design assistant began the reverse-engineering project by first scanning the off-the-shelf air cleaner with a Romer Stinger II portable CMM and then used the scan data to build a mechanical prototype using our usual MCAD package.
The team then started trying to manipulate the MCAD model so that it maintained the measurements of the stock part while adding custom design elements needed to match the rest of the bike.
The first challenge was to create the intricate copper part with the highly detailed Hamster logo embossed on it. After spending two days trying to create the logo, time pressures and other work piled up. We decided to switch tactics and import the mechanical prototype into SensAble’s FreeForm 3D modeling system.
![]() This air cleaner was modeled in FreeForm after a stock unit was scanned and digitizedto optimize final fit and function. |
Past experience had demonstrated that FreeForm provides unparalleled creative freedom, modeling speed, and flexibility when creating complex, highly detailed organic shapes while maintaining the integrity of imported MCAD parts.
FreeForm is based on voxel technology (think of voxels as 3D pixels) instead of mathematics, and unlike traditional MCAD, it has no topology restrictions and the order of operations does not matter. Additionally, FreeForm speeds our design process by providing touch-enabled modeling — an approach analogous to physical modeling. The designers use a SensAble PHANTOM haptic device — instead of a computer mouse — with a Dell Precision T3400 workstation. As they push, pull, deform, and extrude virtual clay, they feel the force feedback on their hand as if they were modeling with actual clay.
Once the team imported the 3D model of the mechanical prototype into FreeForm, sculpting the intricate background shape and embossing the logo into it took only minutes. After that, the rest of the stylizing and detail work required just a few additional hours. The ability to feel the evolving design — literally — in the designer’s hand is both practical and fun. It mimics what we used to do in years past when modeling in wax or clay.
After finalizing the details, we used a Stratasys 400 MC rapid prototyping system to print the prototype in polycarbonate to withstand high heat. The 3D printer is capable of printing larger parts without seams.
![]() SensAble’s FreeForm gave the designer the ability to sculpt and emboss the Hamster’s 30thannual Sturgis ride emblem with the PHANTOM haptic device as though working in wax or clay. |
Challenge Two: Exhaust Tips
The second challenge was to design and build exhaust pipe tips that mirrored a unique swooping shape in keeping with the rest of the bike’s design. The team again turned to FreeForm to solve our design challenge. Once the model was imported into FreeForm, we proceeded to create the shape we wanted in just 15 minutes, retaining all the correct measurements.
FreeForm creates better curves and fillets than traditional CAD systems, and in less time. It also builds a watertight design, which is a huge deal in motorcycle components as well as in toys and other types of products. It provides tremendous creative freedom because we can freely manipulate the model without taking any math into consideration. Another bonus is that FreeForm can maintain the mathematical equations and angles in place while allowing designers to manipulate the outside of the design in any way you can imagine without returning error messages.
After the team was satisfied with the design of the exhaust pipe tip, it was exported as an STL file and then printed as a full-size rapid prototype in ABS plastic, this time using a Dimension 3D printer. Once the prototype was approved, the part was cast in copper using a vacuum-cast process.
![]() Exhaust tips were the final parts created in virtual clay before being printed in ABSplastic on a Dimension 3D printer. |
Saving Time, Preserving Design Appeal
Special design touches such as exhaust tips or custom air filters can be perceived as so much gingerbread when in reality their meticulous detail is often what makes a product appealing. In this project, as with others that our team has completed, we have found SensAble’s FreeForm to be the best solution for rapid form creation and the addition of intricate curves and design elements. Once created in virtual clay, these designs can be readily reused in other components of the product — in almost no time at all.
Between the air cleaner, logo embossing, and exhaust tips, FreeForm reduced our design time by more than half. Just as importantly, it enabled us to meet the functional requirements of the bike while keeping all the “Wow” factor of the design that was so necessary to building our business during Bike Week. FreeForm allowed us to unite form and function in a way that showcased us as first and foremost, artists and inventors, not solely technicians.
The results were what we’d hoped for: I left the Sturgis Motorcycle Rally with multiple business projects and opportunities in the motorcycle accessory business.
More Info:
Dimension 3D
Minneapolis, MN
ROMER
Wixom, MI
SensAble Technologies, Inc.
Woburn, MA
Stratasys, Inc.
Eden Prairie, MN
Scotty Ziegler is the owner of Scotty of California, Inc. To comment on this article, please send e-mail to [email protected].
Subscribe to our FREE magazine,
FREE email newsletters or both!Latest News
About the Author

DE’s editors contribute news and new product announcements to Digital Engineering.
Press releases may be sent to them via [email protected].
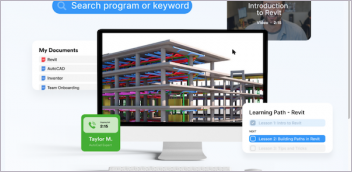

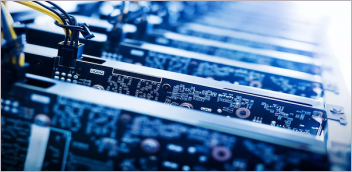
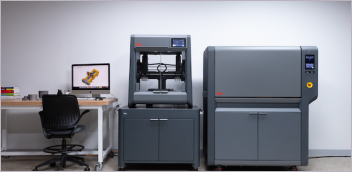