Formnext 2018 Pinpoints Anticipated Disruptions to Additive Manufacturing
Additive manufacturing hardware vendors shift from optimization for quality to optimization for speed and face competition from open-system material manufacturers.

The 3D Systems DMP Factory 350 is the extendable factory version of the new DMP Flex 350. 3D Systems says the new direct metal printer offers 15% improved print productivity at lower cost compared to its predecessor ProX DMP 320 metal 3D printer. Image courtesy of 3D Systems.
Latest News
November 27, 2018
The additive manufacturing industry is built on the disruptive notion that digital processes can directly lead to physical products. At this year’s Formnext conference in Frankfurt, Germany, vendors and analysts emphasized how the latest innovations in printers and materials must be combined with innovative workflow processes.
“The main goal is the industrialization of 3D printing technology,” says Martin Boch, project lead for metal additive manufacturing at Audi. Boch says Audi’s current use of 3D printing divides up three ways. Research and development occupies about 20% of the company’s use of 3D printing; 60% is for prototyping; and another 20% is for creating spare small parts and tooling. Before Audi can move into serial production of small parts, Boch says it must define standard processes for sourcing both printers and materials.
Audi is using production on a low-volume model, the A4 Limousine, as a proving ground for its process innovation research. A large steel frame section was difficult to manufacture with traditional techniques, including the 1,472°F (800°C) foundry work. By moving the frame section to additive manufacturing, Audi optimized the design for improved cooling and a 50% weight reduction. Audi then used selective laser melting (SLM) to create 10,000 pieces.
3D Printing at Higher Volumes
Boch says the increased use of 3D printing technologies and processes will be driven by labor costs. Though the A4 part design “was interesting,” the post-printing processes (including powder removal) were too expensive. Audi expects labor costs to drop 10-fold by 2025 as vendors and manufacturers work together on process innovation to match current technical capabilities.
The next stage of disruptive innovation must address both the processes of industrial production and the 3D printing industry itself, according to Dr. Wilderrich Heising with Boston Consulting Group. By nature, so to speak, additive manufacturing technology is disruptive to both the technology of manufacturing and the supply chain. Heising says the industry has reached a point where “every player needs to redefine its strategy.”
He envisions a shift among AM hardware vendors from optimization for quality to optimization for speed. The ability to “increase build rate by up to five times at the same quality” translates to total reduction of machine cost per part by more than 50%. Today some 3D printing processes can be justified for final part production but only at low volume. Heising says speed optimization will lead to the break-even point moving to higher volumes.
Open Market Materials
Heising sees new competitive pressure in AM is forming around materials.
“Established players, the machine makers, are using the razor blade business model,” he says, in which the same vendor sells the machine and supplies the consumables. More specialty players with new fit-for-purpose materials are coming, bringing with them an open market approach to materials that will lower costs. “There are currently poorer print results in fully open systems,” notes Heising, but “there is high potential to differentiate by mastering materials.”
Research analyst Tugce Uslu at Lux Research echoes Heising’s view. Since 2015 there has been near-parabolic growth in patent activity and published research for polymers and metal, the two largest materials segments in AM. Uslu says technical innovations in printing processes are still ahead of workflow innovations, which will come as a result of software catching up. She points to “positive accomplishments” in software innovation from companies like publicly traded Materialise and CAD startup Frustum, the latter of which was acquired by PTC just after Formnext ended.
Uslu recommends manufacturers looking for the right time to buy into a new process should look for a balance between innovative processes and ecosystem maturity. A new process might provide a technological advantage but be unable to deliver consistently if materials are in short supply.
Polymer and Copper Innovations
Examples of innovative processes and materials were readily available at Formnext. Cubicure introduced a photopolymer offering high strength and high heat deflection. It is aimed at 3D tool printing for plastic injection molding where 3D printed forms must have high accuracy and suitable material properties. The company—a research spinoff from Technical University Vienna—also announced a Hot Lithography technology it says processes viscous photopolymers with high precision at greatly increased structuring temperatures of up to 248°F (120°C). “The high printing temperature enables the use of highly viscous chemical building blocks that were previously not suitable for stereolithographic processing,” the company said in a statement.
GKN Powder Metallurgy presented a new process to create 3D printed inductors from copper. “The unpredictable service life and quality of manually manufactured copper inductors do not meet growing industrial demands,” says Umit Aydin of GKN. Manual soldering is labor intensive and creates disruption points at each soldered connection “leading to significant energy loss.” GKN is currently using selective laser melting to produce copper inductors certified to the IATF 16949:2016 standard. Research continues on process parameters to increase production volume.
30,000 Fuel Nozzles
Industrial giant GE created its Additive Manufacturing division several years ago when it realized it had many divisions developing and using 3D printing technology scattered throughout the company. At Formnext, GE Additive Manufacturing celebrated the 3D printing of the 30,000th fuel nozzle for GE jet engines.
“We eat our dog food,” says GE Additive’s Chris Schuppe, referring to the software industry’s description of using one’s own product. For a new part headed to the next iteration of the Boeing 787, Schuppe says GE will “make the powder, the [3D printing] machine, the part and put it in the engine.” A recent software acquisition, Geonix, adds thermal modeling and build simulation to GE’s software portfolio for AM. Geonix can work with models from all 3D modeling software without needing to make changes to the model.
Functional Full-Color Parts
Rize is a relative newcomer among 3D printer manufacturers, having introduced its first model last year. At Formnext, Rize introduced its second-generation Augmented Deposition printer, the XRIZE. The new printer extrudes engineering-grade thermoplastic and simultaneously jets CMYK inks (cyan, magenta, yellow, black) into the material as it forms. A release ink is then jetted between the part and the automatically created supports to enable the user to peel away the support. Rize says the process eliminates the need for additional finishing.
The combination of approved plastics and full color offers intriguing possibilities, says Rize CEO Andy Kalambi. A print run of otherwise identical parts could have unique QR codes that link the part to an internet of things ecosystem or a blockchain smart contract. This extends the idea of the digital thread “as an immutable connection into a blockchain,” Kalambi says. Part designers could allow customers to print parts onsite in a “digital supply chain” where every instance is verified as authentic.
For More Info
Subscribe to our FREE magazine,
FREE email newsletters or both!Latest News
About the Author

Randall S. Newton is principal analyst at Consilia Vektor, covering engineering technology. He has been part of the computer graphics industry in a variety of roles since 1985.
Follow DE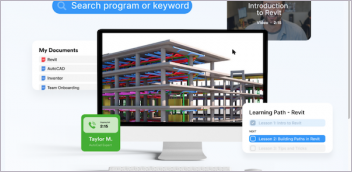

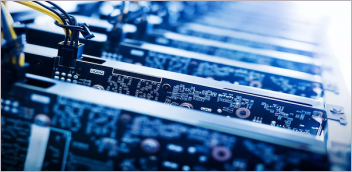
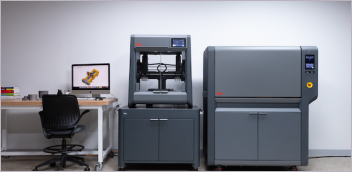