Latest News
August 1, 2006
By Pamela J. Waterman
No longer the lone domain of a handful of back-room experts or a thinly connected box-element on a manufacturing workflow diagram, finite element analysis (FEA)—in its many flavors—is becoming a full member of a product’s lifecycle. Moreover, software developers have recently taken new and practical steps to ensure that this trend continues.
Design re-use, enterprise-wide data management, and process innovation are now terms with real, grab-and-run-with-it meanings that you can use to cut design times and produce better products. Whether you’re a single user tasked with doing a little bit of everything, or a team-player in a worldwide supplier chain, you’ll want to investigate these new tools.
Reduce, Reuse, Recycle
This ’90s mantra is more important than ever in today’s competitive market. For one thing, few designers have the luxury of starting from scratch. Why reinvent the wheel when you can change the size of one or two existing parts within the analysis model, have the dimensions report parametrically to the design model, run the revised analysis, and quickly fill the needs of a new customer?
|
ALGOR |
> > ALGOR FEA software allows users to import material property data from commercial services such as MatWeb, a widely used engineering material database on the Internet (above left); provides tools for managing and customizing a material library (top right); and allows input of experimentally obtained material properties using standard file formats such as Microsoft Excel or comma-separated value files for automatic curve fitting (bottom right).
Moreover, since many designers only spend a few months on analysis, otherwise gathering up-front requirements and searching for parts after design completion, they need tools that maintain their proficiency. User-customizable wizards can help, says John Buchowski, a director of product management at PTC.
“Powered by an .xml template file,” he says, “a process wizard inside Pro/Engineer Mechanica can tell you: check your materials, check the units you’re in, and go to this company intranet site to see how we’ve loaded these things in the past or what type of analyses you should be performing. Subsequent steps could show the user specifically how to apply the particular load, how to constrain the model, how to run the analysis, and what results to look at. These can be customized by a consultant or a more experienced user at the company.”
Compiling prior wisdom is becoming essential to successful FEA, whether building one’s own materials library or providing a series of simulation steps for others to follow. Richard Bush, marketing director for NX Digital Simulation at UGS, explains that a fundamental goal with its Nastran software development is to give the normal (non-expert) user an answer quickly enough so that he can actually base a design decision on it.
|
Dana Corp. |
< < Dana Corp., whose manufacturing line includes engine and drivetrain products, has incorporated Abaqus FEA directly into its design process.
“If you take someone who isn’t quite a specialist, you have to support them very well,” says Bush. “The challenge there is that you really have to have industrial-grade tools underneath the covers to be able to do that.”
To expand the knowledge beyond that which is built into an existing FEA package, you can tap your own company’s expertise to customize wizards with UGS’ NX Simulation Process Studio. Their drag-and-drop wizard building (no C++ here) allows a company’s experts to combine personal notes with previous models and successful process steps, and convert them into their own, tailored wizards.
ANSYS’ DesignSpace environment also started out with its own wizards and evolved into offering tools for wizard creation. Mike Wheeler, ANSYS vice president and GM for the Mechanical Business Unit, makes it clear that there are different needs for different levels of design, and that analysis software must allow for this in its design re-use strategy. He notes, “There’s a big difference between an innovative design process and a refinement design process.” ANSYS Workbench software offers a unified environment that responds to these various needs with interfaces to such differing products as Maplesoft and MS Excel.
Working Across Boundaries
The days of a single department owning a file or design are fading away. Companies routinely share not only 3D CAD data, but analysis results with suppliers, consultants, prototype shops, manufacturers, and marketing personnel across companies, states, and countries. Now you can proactively include FEA results as an integral part of the planning and decision-making process from the comfort of your modeling environment.
|
ANSYS |
> > This simulation wizard leads an engineer through an ANSYS thermal analysis of a cell phone design.
“There’s a lot of emphasis on the reporting side of things, making it easy to create web-based reports published to the company’s intranet or on the Internet,” explains Bob Williams, Algor’s vice president of product development. “Everyone can check the latest revision of a design; this is where the HOOPS Stream File (.hsf) format gets a lot of support, making it easy to share 3D visualizations.” (HOOPS allows highly compressed files of 3D data and bitmap images to be streamed over any bandwidth Internet connection.)
Popular opinion states that for every image generated, there are 20 people who need to view it—and most of them would like to be able to interact with it, too. In response, new visualization products continue to emerge, whether integrated or stand-alone. For example, UGS offers JT2Go, a JT-standard based viewer, including an MS-Office plug-in, that uses lightweight images and data. Think of it as a PDF Viewer for Engineering.
From the independent point of view, VCollab 2006 software offers a multidisciplinary suite of products for CAD, CAM, and CAE visual collaboration. Within a Microsoft Internet Explorer window, a PowerPoint slide, or other programs, product development teams and suppliers throughout the manufacturing enterprise can view and manipulate 3D CAD, CAM, FEA, and CFD information without needing any of the native engineering authoring tools.
How about sharing and organizing all that valuable information across months and years involving different projects and people? That fellow who retired last year; do you know where his 20 years of analysis models reside, or even those from last year? Without getting into the details of product lifecycle management (PLM), we’ve gone full-circle to the topic of data reuse.
“If someone needs to come back and reuse the data three months, a year, two years later,” says UGS’ Richard Bush, “very often it’s hard to work out what the guy did in the first place. This ties into automation very well—if you can understand the process and the workflow to develop something ]like a complicated analysis], and you can automate key areas of it, then you can enable less experienced people to run through the process.”
ANSYS’ DesignSpace tools also support process automation, where one can easily rerun an analysis with ever-changing loads. Users can create parametric models from legacy non-parametric data, and better understand detailed characteristics. Additionally, DesignSpace offers a parameter manager so can you easily compare the results of all the variations.
Andy Meyers, vice president of corporate marketing at MSC.Software, is well aware of the time wasted searching for or re-creating simulation inputs and data.
“Customers spend 60 percent of their time looking for old analyses, such as last year’s door design,” he says. “Keeping data to oneself has been a cultural issue, but engineers must now share, and create an audit trail.” He points to the need for moving from limited product data management to more comprehensive simulation data management, a point of view recently substantiated by a white paper from business/technology guru Bruce Jenkins of Spar Point Research. Within MSC’s SimDesigner Enterprise environment, fully integrated in CATIA V5, users have access to a product’s complete fit, function and performance information as a set of simulations complementary to the details of product definition.
Try, Try, Innovate
Implicit in all these efforts to expand the use of FEA is the driving question, how can companies be more innovative? By using such tools as FEA both up front and for detailed, refining analyses, designers can efficiently veer away from doing it the way it’s always been done. ANSYS’ Wheeler urges the “fail often, fail early” approach, using FEA for many rough-cut analyses to verify the direction of new designs, and reminds us that, “failure is often a better teacher than success.”
Suchit Jain, vice president of analysis products at SolidWorks’ COSMOS division, observes that with the analysis tools now offered within CAD programs such as SolidWorks, everyday designers can be more creative and inventive. By performing even nonlinear what-if FEA up front, users can identify the design elements that lead to a lower-cost product. Jain points out that by actually budgeting FEA as part of the early design process, the resulting freedom to innovate may reduce material costs. For example, a lighter-weight product will use less material at a time when raw material costs are reaching new heights.
Making FEA a part of your company’s bigger picture can be accomplished in many ways, but to stay competitive, the time to do so is now.
Contributing Editor Pamela J. Waterman is an electrical engineer and freelance technical writer based in Arizona. Send your comments about this article through e-mail by clicking here. Please reference “FEA’s Changing, September 2006” in your message.
Smoothing the Connections
Data management, in its broadest sense, is key to making analyses truly useful. Frank Popielas, manager of advanced engineering for the Sealing Products Division at Dana Corp., is an Abaqus user and says that your hardware and software must operate in sync. “With today’s huge file sizes, you have to have a process flow in place ]that manages] how you move information from model setup to solving to postprocessing.” Popielas notes he pushes the limits, and is getting results, but it doesn’t happen overnight.
Users should ask the hard questions about how each vendor’s products make these connections and how easy they are to use. For example, with PTC software, all the data you generate is stored with the model—there are no separate files of loads or materials, so as soon as you retrieve a component, you also get all the boundary conditions.
Dave Weinberg, president of Noran Engineering, observes that improving pre- and postprocessing connections with FEA widens the latter’s use, and is an important topic in discussions among the NAFEMS international community. Examples of these trends include the ability to put together an assembly comprising differently meshed parts and automated report-generation options for end-users with differing needs. Noran’s NEiNastran for Windows, NEiFEA, and NEiWorks products address both issues.
Algor has also strengthened ties in this arena. For the first time, the company is making its FEMPRO pre- and postprocessor widely available for users of other finite element analysis systems, including Nastran solvers from companies like MSC.Software and UGS.—PW
Companies Mentioned
Abaqus, Inc.
Providence, RI
ALGOR, Inc.
Pittsburgh, PA
ANSYS, Inc.
Canonsburg, PA
COSMOS
A Division of SolidWorks Corp.
Santa Monica, CA
Dana Corp.
Toledo, OH
Maplesoft
Waterloo, Ontario, Canada
MSC.Software Corp.
Santa Ana, CA
NAFEMS Ltd.
East Kilbride, Glasgow, UK
Noran Engineering, Inc.
Westminster, CA
PTC
Needham, MA
Spar Point Research LLC
Danvers, MA
UGS
Plano, TX
Visual Collaboration Technologies Inc.
Detroit, MI
Subscribe to our FREE magazine,
FREE email newsletters or both!Latest News
About the Author

Pamela Waterman worked as Digital Engineering’s contributing editor for two decades. Contact her via .(JavaScript must be enabled to view this email address).
Follow DE
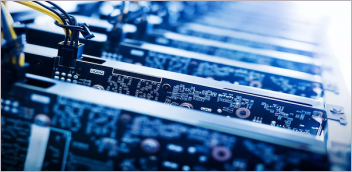
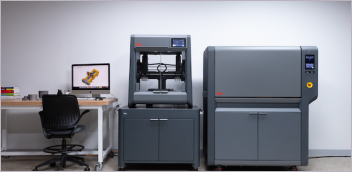
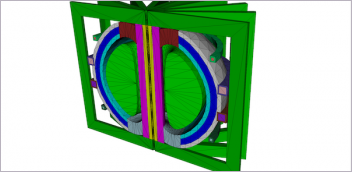