Latest News
September 1, 2010
By Siemens PLM
Editor’s Note: This content is sponsored by Siemens PLM.
![]() |
ATK is a premier aerospace and defense company with more than 18,000 employees in 22 states throughout the United States, Puerto Rico and internationally. ATK develops and manufactures armament, mission and space systems, with the goal to ensure that their customers accomplish their goals – whether they involve a military operation, a satellite launch, or a technological breakthrough.
“At ATK, we’re focused on our mission success, on making our customers successful,” says David Riemer, vice president, Science and Engineering, ATK Space Systems Group. “We’re involved in the Space Shuttle, the Ares Program, the Shuttle Replacement, a lot of technology. We build solid rocket motors as well as participate in other advanced work, including a cancer treatment drug.
“Our business objective is ‘Innovation Delivered,’ which means meeting our customer commitments. It’s understanding the requirements, creating the innovation and putting it in the hands of the war fighter, the astronaut, our customer, whoever that may be, in order to be able to meet their mission requirement.”
“Innovation Delivered” with PLM
To fuel innovation at ATK, the company has fully embraced a PLM strategy that spans the lifecycle, standardized across its divisions and value chain. “The PLM Strategy is important to us because we’re creating an environment that can be used in a standard way across the entire corporation,” says Alan Whitaker, director of IT, ATK Space Systems Group. “Siemens has helped us focus on what PLM really means to us as a business.” Riemer adds, “We picked Siemens’ solutions because of two basic factors: One is Siemens’ commitment to making sure we’re successful. The second is the breadth of the tool set that Siemens offers us.”
ATK’s PLM strategy starts at the onset of a project. Jon Jarrett, senior manager of Engineering Systems at ATK, explains that this covers “from portfolio management to actually gathering requirements, using those requirements, throughout all the organizations inside of ATK and even our supply chain outside of ATK. And then designing and analyzing the product with Siemens’ tools.Obviously one of the most important things is then manufacturing and delivering the product to the customer at the right time for the right price.”
Right time and right price means right system. Some companies have preset notions that limit their perspective in making the best PLM choice. Riemer notes, “When most people go to look for tools, they say, ‘I’m looking for a CAD data manager. I’m looking for a scheduling system. I’m looking for X.’ Whenever you approach it that way, you focus in on a very narrow point system versus looking for an integrated solution that really does transform the business. What we’ve found in Siemens’ products is the means to have all of those elements in one package.”
Challenges:
Keys To Success:
Results:
|
An integrated, enterprise approach ultimately enables effective collaboration. “Siemens provides a footprint that we can take and utilize throughout all of ATK so that we talk a common language, so that we communicate in a succinct way and know what each other is doing, so that manufacturing may be done at a totally different plant than the design engineering effort,” says Jarrett. “We’re then able to use the common tools that Siemens provides in order to communicate across manufacturing, across quality, across all of the aspects of the product.”
At ATK, collaboration typically extends beyond the organization. Riemer explains, “We collaborate extensively with our NASA customer on Ares and on the shuttle program.We do programs with the Navy and the Air Force, and it’s important that we can collaborate with them. We share and act as a team using Teamcenter’s community collaboration.” Jarrett adds, “We’re utilizing Teamcenter to connect our products to our customers, to our suppliers, to our vendors. They are part of the actual work flow process. So they may approve our design changes as well as our designs. In a collaborative role, we’re able to utilize Teamcenter to get ideas from all sorts of venues and manage changes within one system.
“For Ares, the benefit of having the single source of data within Teamcenter has really been the fact that we’re getting ready to go fly our Aries 1X, the first unmanned flight of Ares this summer. There were a lot of people who said that couldn’t be done. We’re going to fire our first development motor, a full-scale, five-segment solid rocket motor. It’s the world’s largest rocket motor. It’ll produce 3.6 million pounds of thrust. It’s going to burn 1.3 million pounds of propellant and we’re going to do that this August, on schedule.”
Unified PLM to meet customer commitments
A long-time Teamcenter customer, ATK is now transitioning to Teamcenter’s unified architecture to take advantage of the most tightly integrated PLM available. “Without a unified architecture, you can do effective data sharing and migration between systems, but it’s a loose integration,” says Riemer. “What unified does is a tight integration; a sharing of one common set of data for all of these tools. For project management, for systems engineering, for our CAD data, for our knowledge capture, so you get all of that integrated in one system, one data base. It’s one data entry. The same piece of information shared multiple times.
“Teamcenter unified is going to help us better meet our customer commitments. By integrating the scheduling information, the cost information and the technical information into one entire package available to our engineering staff when they need to do their work, we become acutely predictable. When a customer expects us to do something, we’re going to deliver on it.” Whitaker adds, “In the past we’ve had to support all of these as individual standalone applications.” With Teamcenter unified, now we’re going to be able to manage one common environment.”
![]() |
Managing customer needs
When it comes to meeting the needs of customers, ATK takes Teamcenter’s integrated solutions to a whole new level. “One of the critical items that we look at is managing a portfolio of products,” says Jarrett. “Trying to understand what our customers need; trying to understand where we should focus our business resources as well as our financial resources is very critical to the business. And so utilizing the portfolio management suite is certainly a key contributor to our success.”
Riemer agrees, “It’s important to understand, of all the projects every year that we want to start work on – and we in engineering have a long list of projects in the queue – we have to figure out which ones make the best business sense.We use Teamcenter’s portfolio management tool to help us make the assessment as to which products, which programs, which customer needs are the priority. In so doing, we are also explicitly tracking customer requirements.”
Effective requirements tracking translates to accountability. “The requirements gathering up front really helps out in determining who needs to use those requirements,” says Jarrett. “We take those overarching requirements and we delineate them into requirements for engineering, requirements for manufacturing and requirements for quality. So at the downstream level, those guys are aware of what requirements they are designing to or what requirements they are manufacturing to. And then they can validate and verify that they’re actually meeting those requirements. With overarching and individual requirements management, the entire value chain has access to the appropriate requirements and they’re accountable for them.”
Not just innovation, “Innovation Delivered”
In the highly competitive business of innovation, it’s not enough to have the best technology. ATK’s PLM strategy is also focused on execution. “One of the most important things we do in engineering is manage projects,” notes Riemer. “If you look at today’s marketplace in aerospace, it’s very difficult to get a competitive advantage on the technical side, alone. I have to abide by the same laws of physics that our competitors do. I buy materials from the same suppliers that our competitors do. So when you really get down to it, it’s very difficult to get a quantum leap in the technical answer that we give our customer versus a competitor’s answer. That doesn’t mean we don’t strive to optimize such breakthrough insight, and we do use the tools to do accomplish that, but what really is important is impeccable delivery on the total set of customer commitments, which means delivering on schedule, on budget, a technically superior answer.”
Jarrett adds, “Technically we’re really good, but to manage cost and schedule is a whole different ballgame for us.While we’re effective, there’s always room for improvement, which can mean a competitive advantage. Therefore, we’re focusing on using the project management tool to help us thoroughly understand the schedule that we need to meet. We identify the critical deadlines that we must address as we design the product. Having such information available for everybody to look at and collaborate on throughout the process is extremely important for us in meeting the cost and schedule requirements of the program.”
The systems engineering capabilities of Teamcenter stand out in helping ATK meet its goals. “We can go all the way from a customer’s set of requirements, their statement of work, to the tasks in a schedule and we can trace all the way back to that statement of work and know why we’re doing that task. We’re doing that task to comply with this portion of the customer’s requirements, the statement of work. There isn’t anything like that out there. A company buys a scheduling system for project management, but then it stands alone. Many create their own work scope within Word. Well, we can create that within Teamcenter using Microsoft Office products like Word. We can actually trace all of those customer requirements down to ‘why we’re doing it.’ So when we hand an engineer a job to do, we can hand them defined scope, including: ‘Here’s the number of hours you have to do it. Here’s the time frame you’ve got to do it. And here’s the complete set of technical requirements that are needed in order to do the job.’ We do that using Teamcenter’s systems engineering functionality.”
Design and simulation for next-generation space shuttle
For product design and analysis, ATK uses Siemens’ NX™ digital product development solution. “ATK has been a long time user of the I-deas product and we’re now transitioning to NX,” says Riemer. “We’re using NX on Ares, the replacement to the space shuttle that will take man back to the moon and beyond; perhaps back to Mars someday. We’re responsible for the entire first stage within Ares. Therefore, we’ve got to develop the wiring harness and design plumbing routings of very large structures.We are responsible for simulation and analysis as well, so we are beginning to use the NX tool set to do the modeling and simulation portion of Ares.”
![]() |
“We’re using NX for product analysis and simulation to help us really understand how the products are going to operate,” says Jarrett. “Our products take care of the astronauts, and there’s no doubt that the Siemens’ tools provide us with the opportunity to move forward not only with NASA and our contributions to the space shuttle today, but also in proceeding with Ares. To simulate those products upfront is absolutely critical.We have to understand the loads that they’re going to be able to take. We have to understand how they’re going to perform under flight conditions. And doing the simulation in a digital environment is the only way that’s going to be accomplished.”
Off to a quick start to save IT costs
As ATK deploys Teamcenter on the unified architecture across its global sites, the company has developed a fast-track approach to implementation to save time and IT costs. “From an IT perspective, we manage the Teamcenter environment at ATK from our Center of Excellence, which allows us to create economies of scale throughout the entire business,” says Whitaker. “The processes we use are standardized, so we’re able to increase and optimize the efficiencies that exist in the environment.”
Jarrett point out, “The scalability of Teamcenter is astonishing. It’s wonderful to be able to manage total project scope across multiple sites and yet have succinct and specific information at the fingertips of the users and the engineers in any location.”
ATK notes that the ability to fast track a project is significant in terms of value. “The ‘Quick Start Program’ is specific to Teamcenter, and enables us to create and implement a production environment for ATK locations as needed,” says Whitaker. “This has allowed us to dramatically reduce our implementation costs and the time it takes to move from having nothing to a full-blown production environment. Prior to the Quick Start Program, it might take a couple of years to implement a location with this level of sophistication and return-on-investment to the organization. With Teamcenter, we’re able to go out to a location and stand up this environment within six to eight weeks.”
Subscribe to our FREE magazine,
FREE email newsletters or both!Latest News
About the Author

DE’s editors contribute news and new product announcements to Digital Engineering.
Press releases may be sent to them via [email protected].

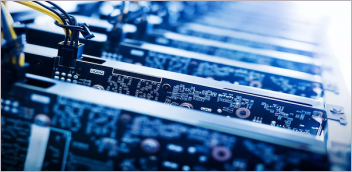
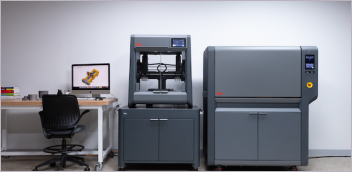
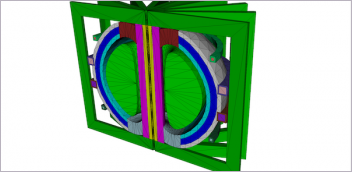