Designing for Short-Run Production Needs
Fast builds with no tooling make direct digital manufacturing increasingly attractive.
Latest News
August 1, 2012
By Pamela J. Waterman
Any time a product or service forms 30% of a business, it demands attention. That number is typically reported by service bureaus operating additive manufacturing (AM) equipment, as the percentage of their projects now involving direct digital manufacturing (DDM).
Distinct from rapid prototyping, DDM creates real parts for real end-use products. The term encompasses single-use models for lost-wax casting, multiple-use molds and tools for casting or injection molding, “on-demand” one-off consumer-customized pieces (produced through services such as Shapeways and Sculpteo) and short-run actual parts.
In this article, DE examines the benefits and challenges of the latter topic: DDM as a game-changing technical and business approach to high-end professional part production. Across the board, service bureaus and a number of manufacturing companies see this tactic as a growing part of their operations, even commanding a competitive advantage.
Confirming this trend, in his 2012 Additive Manufacturing and 3D Printing State of the Industry report, consultant Terry Wohlers says 24% of all money spent on AM products and services is tied to direct part production. (Editor’s Note: Although the term “direct digital manufacturing” is not officially acknowledged by ISO or ASTM International, we use it here for simplicity.)
Never Know Until You Try
Awareness of AM’s possibilities is (finally) growing faster now than it has in the past 25 years. Chuck Alexander, a veteran of the AM business for 23 of those years, helped usher in the industry at 3D Systems—and continues to push its limits as AM product manager at Solid Concepts, a California service bureau with broad experience and equipment in this arena. He says the growth of the 3D printer lower-end market has made more people aware of AM in general, and the capabilities of high-end DDM in particular.
![]() |
Dental models in a custom proprietary SLA resin built by In’Tech Industries on a fleet of 3D Systems’ IPro 8000 and 9000 SLA machines. Image courtesy of In’Tech Industries. |
Solid Concepts currently fills about 25% of its customer projects via AM. Alexander says he sees the technology’s freedom of design as a great plus, giving the example of forming zip-tie mounts into ductwork to eliminate assembly steps and simplify installation. He adds, however, that “there’s a lack of knowledge regarding both the benefits of AM and the need to define process specifications such as part orientation.”
Benefits that bureaus and their customers see include opportunities to:
- eliminate tooling production costs, both for initial designs and for revisions;
- quickly modify or customize a product during the production lifecycle;
- save time vs. ordering tooling;
- create parts with curves that are difficult to machine;
- hold tolerances better than with injection molding;
- consolidate assembled parts into a single unit, eliminating the time and cost of assembly labor, number of parts to be kept in inventory, and the accompanying traceability paperwork;
- provide cost savings when producing internal parts, where aesthetics may not be important; and
- compete directly with overseas manufacturers, because the pricing of AM systems, parts and operation is the same for them as for U.S. users.
Challenges when using AM for end-part production may include the following:
- A lack of knowledge of control processes, which is important for reproducibility, especially for aerospace—designers must be educated to add them to specifications.
- Tolerances may be harder to hold, compared to traditional production methods such as machining.
- Currently, there is a limited material selection.
- Costs are higher for equipment, consumables, labor and maintenance, although this is very quantity-, system- and design-dependent.
- Possible infrastructure issues may arise with managing massive amounts of data, when hundreds of unique files are involved—with dental applications, for example.
![]() |
Hearing-aid ear shell built by In’Tech Industries on 3D Systems’ Viper Si SLA system, with thousands built daily. Biocompatible material is Dreve Fototec; gloss finish is net-proprietary finished (no post-polishing or lacquering). Image courtesy of In’Tech Industries. |
For a growing number of manufacturers, however, the benefits clearly outweigh the challenges. DE spoke to companies across the country to hear why this approach works so well for them.
Axon Styrotech Corp.
In Raleigh, NC, Axon Styrotech manufactures machinery and systems for heat-shrink sleeving, tamper-evident banding and stretch-sleeving, as placed on a wide range of products—from lipsticks to ice-cream cartons to plant fertilizer bottles. In December 2010, the company purchased an Objet Eden 260V system, primarily to make custom tooling for its own machines.
One DDM part used in Axon’s sleeving equipment widens out a flattened shrink-sleeve label to conform closely to the final container’s shape (an oval plastic shampoo bottle, for example). The sleeve is then cut from the feed-roll and ejected down to surround the product prior to the shrinking step. Pre-shaping the sleeve helps eliminate jamming the wrapper-feed process.
Ken Nyren, an Axon engineering manager, says his company chose the Objet printer because the parts (generally built in Objet FullCure 840 Vero Blue polymer resin) come out homogeneous, with uniform strength in all directions. In addition to building the custom shrink-sleeve forms, Axon uses the AM system to quickly make spacers and guides that also go into its custom machinery. Nyren says they find more uses every day for the Objet printer, and about 65% of those parts are for end use. “It’s expensive to stock a part, but we can stock material and print a part in 20 minutes,” he explains. “Every day, we find something else to do with it.”
C.ideas
C.ideas of Crystal Lake, IL, has been heavily involved in AM beta testing and development efforts since 1998. Already offering more than 17 in-house AM machines and a choice of 24 materials, C.ideas has seen its orders for DDM parts steadily increase over the years.
“This incline is driving us to invest in more ‘production-ready’ based RP and AM systems,” notes Mike Littrell, C.ideas’ project manager, with the process now accounting for 30% of the company’s AM output.
![]() |
Close-up of shrink-sleeve tooling built on Objet Eden 260V additive manufacturing system, for Axon Styrotech shrink-sleeve packaging equipment. Image courtesy of Axon Styrotech. |
DDM’s benefits have been the deciding factor for a number of recent C.ideas projects. For example, the bureau recently helped the sales force of a turbine-manufacturing customer save time and back pain by creating 80 scaled-down plastic models for trade show travels.
Littrell has high praise for the results produced on the recently acquired sPRO60 HD HS selective laser sintering (SLS) system from 3D Systems.
“Even though it’s not the biggest build, it’s a phenomenal machine,” he says. “We produced four turbine designs, 20 parts each, in 48 hours.”
For another C.ideas client, the option of redesigning an assembly as a single AM-built part paved the way for building 60 sets of complex aircraft ventilation ducting, whose odd shape couldn’t be produced any other way. C.ideas also supplies low-quantity motor covers for an agricultural baling company that builds and customizes each of its customers’ $2 million to $3 million machines with different motors and controls.
In’Tech Industries
Medical and dental DDM applications may not seem flashy, but by volume, they’re the solid foundation of this field. At Ramsey, MN-based In’Tech Industries, about 20% of AM is for end-use products—mainly direct-fit consumer-based ear appliances done via SLA. If one includes SLA dental models for making final appliances (replacing plaster models), that number increases to 50% of its AM business.
![]() |
Hold/Release “fingers” for gripping bottles prior to shrink-sleeving, made on Objet Eden 260V equipment in Objet FullCure 840 Vero Blue polymer. Built by Axon Styrotech and used as final parts in its shrink-sleeve, tamper-evident banding equipment. Previously built in sheet metal, which was too springy and difficult to machine. Image courtesy of Axon Styrotech. |
Randy Stevens, Virtual Translation Manufacturing (VTM) division operations manager at In’Tech, explains that his company started with SLA in 2000 to support its injection modeling/tooling business. By late 2004, it was solidly in the digital hearing aid ear-shell and dental model markets.
“It’s fairly easy to manufacture hearing aid shells, but it involves handling massive amounts of data,” he says. “Some bureaus make 10 tools per day; we can make thousands of consumer parts a day. Also, dental files are extremely dense, involving massive FTP transfers. This requires high-end PCs, high-speed data lines, and planning for continued growth.”
Stevens points out that back in 2005, uploading an entire tray of dental items could shut down his AM equipment, because the internal PC controlling the system couldn’t handle that much data and had to be reprogrammed. Even today, that data load in a single build-run could be a problem for some machines, but In’Tech has it mastered.
Met-L-Flo
Originally formed in 1969, service bureau Met-L-Flo of Sugar Grove, IL, has employed AM since 1990—and uses 3D Systems’ SLA and STRATASYS’ Fused Deposition Modeling (FDM) equipment for plastics DDM.
President Carl Dekker, who somehow makes time to participate in every trade show and working group in this field, says about 20% of his company’s work creates end parts. Examples include inspection gauges and go/no-go devices, fixtures for ultrasonic welding (some for themselves, some for customers), masks that can be used for painting an object, and flight-qualified hardware.
For this field to expand even more, Dekker says, the challenge still comes down to education.
“People have not yet recognized the specialty niche market,” he adds. “They are not taking advantage of trying to replace a part ]using AM]. For the most part, outside of the current AM community, people in the design community are just not aware of the possibilities. If someone is working in the development phase of a new part, they can realize tooling savings and logistics savings.”
RapidFit+ Fixtures: Modular Fixturing Systems One unusual end-use application of additive manufacturing (AM) comes from Materialise. The Belgian company, known for its many AM-related products and services, operates RapidFit+, a division that produces custom fixturing via AM technology. |
Rapid PSI
It’s just this type of savings that led service bureau Rapid PSI to try FDM as the replacement process for a urethane-casting project begun in 2009. Rapid PSI operates four Fortus FDM 3D production systems, and is aerospace AS9100-certified. Based in Wichita, KS, the company makes production parts for global business-jet manufacturers.
Customer Kelly Manufacturing, a worldwide producer of general aviation instruments, was concerned about holding tight dimensions on the housing for a small toroid in a turn-and-bank indicator gyro. Moreover, the cast parts required manual sanding—and any new versions meant expensive retooling.
Wolfgang Struss, business development manager at Rapid PSI, switched to building the toroid housings on the Fortus machines using SABIC’s Ultem 9085 flame-retardant thermoplastic. By starting a run in the evening, Struss could have 500 parts ready in the morning—parts with better dimensional accuracy, usable directly off the machine with no hand-sanding. Per-piece price was reduced 5%, order-to-delivery time dropped to three days, and retooling costs were eliminated.
“The fact that FDM is a direct manufacturing technology has become the determining factor in the price/volume calculation that governs a substantial portion of the decision-making process for our customers considering tooling cost as a part-revision parameter,” says Struss. The impact of that consideration is reflected in his company’s usage of its Fortus systems: a 70/30 percentage mix of end-user- to prototype-parts.
Consider AM Metals, Too
Plastics may form the better known side of AM, but metals form a growing presence. Long known for creating AM parts from various metals for medical and industrial applications, EOS is expanding its direct-metal laser sintering (DMLS) technology into more end-use businesses. Recently, the German-based company signed a strategic development partnership with Cookson Precious Metals (CPM), a worldwide supplier for the precious metal industry. The two companies will introduce and further develop precious metal-based applications in the luxury goods industry, with products and services involving DMLS.
“The particular beauty of this technology is that it can be used to produce both one-off pieces as well as large-scale production, eliminating many process steps and tooling costs we see today,” says Stella Layton, global vice president at CPM.
The partnership plans to utilize various special metal alloys and install a custom solution chain for high-volume jewelry production. Cookson is initially offering production of 18-carat yellow gold designs for custom jewelry and watch components.
Solid Concepts also uses EOS systems for DMLS production, typically of small, intricate designs for the firearms aftermarket.
Influencing Company Strategies
You know a technology has reached critical usage when end users don’t want it known that AM is their key to shipping product in two days instead of two weeks. For example, Vista Technologies of Vadnais Heights, MN, uses a wide range of AM technologies, including Objet PolyJet and Stratasys FDM, to create about 30 parts a week. Yet, as proof of the importance of this approach, its DDM customers feel the technology gives them such a competitive advantage they are not willing to be named or discuss their applications.
According to Met-l-Flo’s Dekker, standards (and lack thereof) continue to be a sticking point for expanded AM production use. “No one wants to put out a product with a one-year warranty and find it falls apart in eight months,” he points out. “Since manufacturers don’t yet have enough data to know whether parts will last 20 or 30 years, they’re trying to put them into non-critical applications. They often don’t want to make it known they’re using AM parts until they get more data from experience.“
Rapid PSI openly admits to DDM as a game-changing experience. “FDM technology has transformed Rapid PSI’s core business from rapid prototyping with custom manufacturing to rapid manufacturing with custom prototyping,” says Struss. “We are participating firsthand in the direct manufacturing sea change, which is displacing traditional prototyping and relatively low-volume production processes.”
Designing for AM vs. tooling is a growing trend that up-front design engineers should keep an eye on.
Contributing Editor Pamela Waterman is an electrical engineer and freelance technical writer based in Arizona. You can send her e-mail to [email protected].
More Info
3D Systems
Axon Styrotech Corp.
C.ideas
Cookson Precious Metals
EOS
In’Tech Industries
Met-L-Flo
Objet Geometries
Rapid Processing Solutions Inc.
Sculpteo
Shapeways
Solid Concepts
STRATASYS
Vista Technologies
Wohlers Associates
Subscribe to our FREE magazine,
FREE email newsletters or both!Latest News
About the Author

Pamela Waterman worked as Digital Engineering’s contributing editor for two decades. Contact her via .(JavaScript must be enabled to view this email address).
Follow DE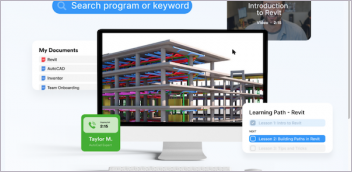

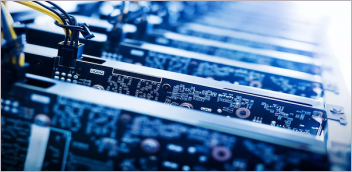
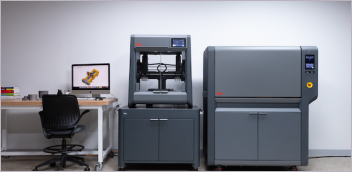