Build It, and They Will Come
Multi-material 3D printing just might elevate your prototyping to new levels.
Latest News
February 1, 2014
By Pamela J. Waterman
Whether the topic is a better mousetrap, an unexpected baseball field or a multi-talented 3D printer, customers still need to be educated before they beat a path to your door. Take multi-material printing: Do you know what company has been doing it for seven years? Do you know who just entered the market in December? And if this is all so great, why aren’t more people doing it—or are they?
![]() Sample part demonstrating hard and soft material properties, built in a single run on an Arburg freeformer system. Image courtesy of Arburg. |
Much More Than a Black/White Mix
Multi-material additive manufacturing (AM) has three possible meanings, each referring to a single build run:
- printing multiple parts where one part is done in Material A and one in Material B;
- printing one part with different areas made of Material A or Material B; or
- creating one part where some or all of its structure is Material C1, C2 or C3, etc., where each C is a blend of different proportions of A plus B created in process.
Illustrating the multi-material advantage, customer Trek Bicycle uses Connex systems to print bike prototypes where the frame is rigid white, the tires are rubbery black, the seat is somewhat soft, the handle-grips have a little give, and the brake cables feature a solid core with a flexible overmold.
Material blending is not a simple task, says Bruce Bradshaw, Stratasys marketing director for the Objet systems. “It requires a very scientific approach to put the material in the right place to create a part with properties that are repeatable such as Shore 70 hardness, independent of part geometry or which Connex system was used,” he explains.
These complexities help explain the lack of competitors in the 3D printing industry, but why don’t more customers and service bureaus employ existing multi-materials? Bradshaw says the public is still not aware of the benefits and, until the Connex 1000 debut, most service bureaus determined that the process’ throughput was too low.
The Service Bureau Perspective
Phoenix Analysis & Design Technology (PADT) has been operating Objet systems for years. “There is a convenience of being able to run multiple materials in a single machine run without having to do multiple machine setups,” says Rey Chu, PADT principal, referring to a run of flexible parts with rigid parts along with semi-flexible parts. However, demand for the multi-material capabilities is low, because parts designed for multi-material production are still few compared to parts specified for a single material. Drawbacks that Chu sees include costly materials and properties that are sometimes less than desirable: standard rigid materials are brittle, with low temperature thresholds, and flexible materials have low tear strengths.
![]() Sample tire for a remote-control toy car, with both black rubber-tire and rigid white wheel-sections built as a multi-material part on a 3D Systems Projet 5500. Image courtesy of 3D Systems. |
Patrick Gannon, engineering manager at rp + m, an Ohio-based design-through-manufacturing service company, also finds that clients are often surprised by the Connex option to create parts with both hard and soft properties.
![]() Integral clear plus opaque white sections on a part formed in a single build-run on a 3D Systems Projet 5500. Image courtesy of 3D Systems. |
“People just don’t know about it enough,” says Gannon. “And the multi-material, as with all the other technologies, has its limitations. The material is not going to last very long. Inside a car on a hot day it’s going to warp, but for prototyping it’s perfect.”
For the future, he sees people seeking a higher level of durability, better thermal properties and possibly a color capability beyond the white, black and gray options currently dictated by hardness.
Old Kids on a New Block
With years of development work under its belt, Objet has basically been the lone contender in the multi-material plastics world. The company’s systems give users control over a number of seriously complex parameters involved in building parts at the pixel level. Whether blending droplets, mixing powdered particles or depositing liquid resins, for anyone else to join this market—on-the-fly multi-material printing, with precise placement, properties and repeatability—would take major effort and resources.
A Higher Profile Interest in multi-material 3D printing is also on the rise from big-name manufacturing companies. Last year, General Electric (ranked sixth in the 2012 Fortune 500 list) solidly entered the additive manufacturing (AM) field with its acquisition of Morris Technologies’ direct-metal laser sintering expertise. Recently, the company’s Global Research division hosted a webinar with prominent AM industry figures, where the topic of multi-material options came up over and over again. In follow-up discussions, Todd E. Alhart, director of media relations for the group, said, “As excited as we are about the new designs and shapes of parts that can be created with additive technologies, we’re equally excited about new materials that can be engineered. The ability to form materials as you build your net shape has opened up new possibilities in the engineering of novel, better performing materials.” Alhart added, “We have a robust portfolio of ongoing research in multi-material AM; metals and ceramics are the classes of materials we are most interested in working with. As we work on the development of new materials in the lab, we are closely monitoring advances in technologies that can enable and enhance this discovery work.”—PJW |
Therefore, it wasn’t a complete surprise that AM pioneer 3D Systems was next to enter this field. At the December EuroMold show, the company presented the ProJet 5500X Multi-Material 3D Printer. Using VisiJet Composite materials, the ProJet 5500X (building on existing MultiJet Printing technology) is said to offer more than 200 material configurations as multiple composites of three base materials. Color variations of the composites go from translucent to opaque, through shades of white and gray to black.
Meanwhile, in the world of metals, DM3D Technology has rather quietly spent years developing a laser-based, direct metal deposition process that is inherently well suited to multi-material operation. Building on its previous ownership under POM Group, the company offers a way to deposit surface protective cladding and/or coating solutions to rebuild and protect tooling. With systems running dual- and even quad-hoppers of powdered metals, customers can specify different metals to be deposited on different areas of the base part, or request mixed metals for certain regions.
“With a dual-hopper, we do graded composites that allow you to add the ceramics as you want,” says DM3D COO Bhaskar Dutta, offering a cermet (a composite material composed of ceramic and metallic materials) as an example. Another example is applying a graded tungsten carbide (WC) hardfacing edge on an oil/gas drill—starting with a 10% fill deposition on the base steel, gradually changing to 25%, 50% and finally 60% for the final outer edge. Changing the mix layer by layer greatly minimizes expansion coefficient issues during end-use, extending tool life.
![]() Eyeglasses formed of multiple materials (clear and opaque black) in a single build-run on a Stratasys/Objet Connex System. Image courtesy of Statasys. |
Dutta says working with multiple materials is a sophisticated technology. His company has a propriety database that ties the build materials to the build parameters. A team of design, material and process engineers works together to define the best “recipe” for each combination. DM3D is currently in product development with several large customers, and expects to be in production mode in 16 to 24 months.
New Entries, Even Newer Ideas
3D Systems isn’t the only new entry in the multi-material marketplace: Stalwarts and newbies alike have announced relevant products and development programs. Arburg of Losburg, Germany, an equipment manufacturer since 1923, was also at EuroMold, demonstrating its freeformer AM system. The dust-free machine can deposit multiple colors and materials simultaneously, using a process based on melting plastic beads delivered through a nozzle as droplets; the part moves (in three- or five-axis versions), so no support structures are necessary.
![]() Steel-clad copper cores for high productivity tooling in aluminum die casting. The steel is bonded to copper through a proprietary buffer material. Image courtesy of DMD 3D. |
A development group at the National Nanotechnology Manufacturing Center in Swainsboro, GA, has demonstrated an interchangeable Multi Proto Lab system that builds a part from disparate materials while the part “stays put” and the process equipment comes to it. The lab currently combines modules for precision milling, soldering and 3D printing with ABS filament; a metal drop-on-demand module is planned.
“This is the way that the industry is moving forward, with multiple processes and multiple materials,” says Multi Proto Lab Marketing Manager Calvin Close. “It’s a whole paradigm shift where you only need five or 10 parts.” One goal is to create functioning parts in the field—such as (but not limited to) building a printed plastic part with operational copper circuitry deposited on its surface.
![]() A compaction tool built with alternate layers of hard and soft metals for high toughness as well as wear resistance. Image courtesy of DMD 3D. |
Also aiming at printed circuit boards, among a wide range of end uses, is The Technology Partnership (TTP), a technology development company located south of Cambridge, England. Its website describes a new printhead, the Vista 3D, that can handle various organic and inorganic materials such as ceramics, biological cells, enzymes, metals and plastics. At press time, there was no word yet on the 3D printers it supports.
Improving build speed in resin stereolithography (SL) systems is the primary goal of a University of Southern California Viterbi School of Engineering project. However, Professor Yong Chen says the research also supports fabrication with two base materials. The system uses bottom-up mask-image-projection, then switches out the resin vats during the build process of a single layer. A key factor is cleaning off the part between materials.
Cool Developments on Tap
To increase user demand for multi-material 3D printing of any sort, original equipment manufacturers (OEMs) will have to invest in material development that improves durability for both rigid and soft materials. Color options in plastics will probably be next, along with software that helps designers specify placement of material variations precisely across part geometry—even at the pixel level.
Certain efforts on the latter subject have been underway for years: Check out the work done by engineer/software developer Jonathan Hiller, now of Modular Robotics, on open-source VoxCad. The software has been tested at MIT’s Self-Assembly Lab on its 4D printing project with a mind-bending variation of Connex multi-material parts. In conjunction with Stratasys, the group has worked on programming different properties—specifically, water absorption variations—into each droplet of an experimental material. In their video, a sample rod, printed straight, bends itself into a 3D shape when immersed in water, as sections react differently to moisture. It’s somewhat like a dry sponge changing shape as it soaks up water, but much more sophisticated.
Contributing Editor Pamela Waterman, DE’s simulation expert, is an electrical engineer and freelance technical writer based in Arizona. You can send her e-mail to [email protected].
More Info
3D Systems
General Electric Global Research Division
Phoenix Analysis & Design Technology
University of Southern California
For more More Information on this topic, visit deskeng.com and rapidreadytech.com.
Subscribe to our FREE magazine,
FREE email newsletters or both!Latest News
About the Author

Pamela Waterman worked as Digital Engineering’s contributing editor for two decades. Contact her via .(JavaScript must be enabled to view this email address).
Follow DE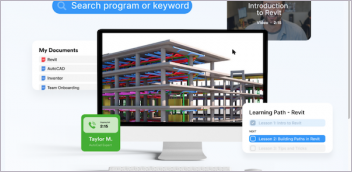

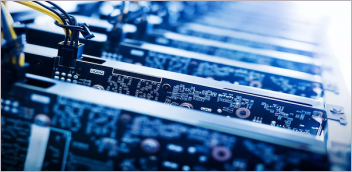
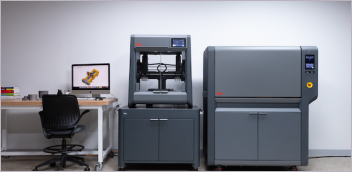