ANSYS, SAP Spin Digital Thread Between Engineering and Industrial Operations

The platform transforms information from physical sensors and physics-based ANSYS simulation models to create 3D visualizations for operations optimization. Image courtesy of ANSYS.
Latest News
July 2, 2018
ANSYS is pairing its digital twin technology with SAP’s cloud platform and manufacturing and asset management software portfolio to create a platform to help manufacturers optimize operations and maintenance based on real-time engineering insights.
SAP’s Predictive Engineering Insights Enabled by ANSYS creates a digital thread between engineering and industrial asset management, enabling machine operators to leverage real-time data to optimize operations and maintenance. For engineers, the platform will deliver intelligence that can shorten the development cycle on subsequent product iterations and inform future innovations. The solution, which runs on the SAP Cloud Platform, is targeted at a variety of industries that depend on large enterprise assets, including oil and gas, energy production, aerospace & defense, and heavy-duty industrial machinery.

Combining SAP’s Internet of Things (IoT) enabled Enterprise Asset Management capabilities with ANSYS simulation muscle will enable customers to harness the massive amounts of data generated by simulations and sensored industrial equipment to foster better decision making—whether that’s to ward off a potential maintenance problem before it happens or to make a design change based on real-world performance of a product in the field. The platform can also be used to create hybrid models that couple machine learning with physics simulation models so engineers can accurately predict the possibilities for asset failure well after it’s deployed in the field.
“The combination provides customers with the ability to translate insights from simulation-based digital twins into actions that significantly improve maintenance and operational outcomes,” says Sameer Kher, director, Product Development at ANSYS.
Using ANSYS Twin Builder, part of the joint solution, engineers can build, validate and deploy an asset’s digital twin and simulate its behavior under different environments and stresses displaying results in dashboards and 3D visualizations. Via integration with SAP Cloud solutions, users create runtimes, which are then linked to industrial assets in the field; the resulting digital twin utilizes the current product state to simulate future states. By doing so, engineers and manufacturing operations personnel can get a jump on maintenance problems before they occur, replacing traditional time-based maintenance methods with predictive and prescriptive maintenance. They can also leverage those same insights to make changes to the product design so subsequent iterations of the system will avoid future glitches.
Kher used the example of an electrical submersible pump (ESP) to showcase how the platform would work. The ESP, used to pump tens of thousands of barrels of oil per day, might encounter wear and tear problems due to exposure to excessive sand, which could result in unplanned downtime costing millions of dollars per day. “Simulation augmented predictive maintenance schemes would better predict such service issues through digital inspection,” Kher explains. “Unplanned downtime would be significantly reduced by scaling back production to a lower level and by ordering replacement parts.”
To power up SAP’s Predictive Engineering Insights Enabled by ANSYS, the pair are integrating technology from ANSYS that allows the SAP Cloud platform to execute the runtimes exported from ANSYS Twin Builder. In addition, ANSYS plans to continue development of Twin Builder technology that enables run-time code generation, Kher says.
To learn more about where the joint ANSYS/SAP partnership is heading, check out this video.
Subscribe to our FREE magazine,
FREE email newsletters or both!Latest News
About the Author

Beth Stackpole is a contributing editor to Digital Engineering. Send e-mail about this article to [email protected].
Follow DE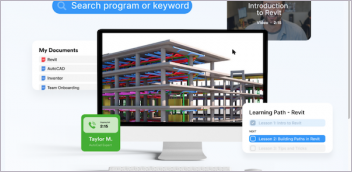

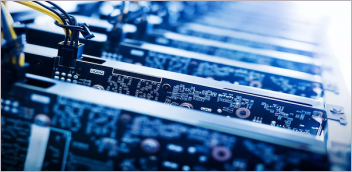
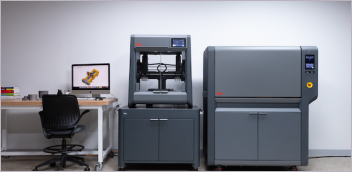