A Work in Progress
At this point, concepts and culture are changing slowly. It's the new crop of enabling tools that is driving and shaping the mechatronics methodology evolution.
Latest News
July 1, 2010
By Tom Kevan
Mechatronics’ evolution has been much like that of the design of a complex machine. The essential concept is present in the early stages of development, but a fuller picture slowly unfolds as layers of detail are added that define new elements. For the machine, this means a better understanding of structure and functionality. In the case of mechatronics, the core concept and “culture” are being fleshed out, and new enabling tools have been added to the designer’s arsenal.
![]() Figure 1: The top window depicts an electromechanical system that contains a DC motor, worm gear, Hall effect sensor, speed controller, and a motor servo-amplifier. These components are combined in an associated SimElectronics model (left). The colored blocks in the model correspond to the components in the electromechanical system. Image courtesy of MathWorks |
The fact is that the methodology is not static. Instead, it is slowly changing, evolving, and re-inventing itself to adapt to the changing nature of the machines and devices it creates and the marketplace it serves. Additionally, its core concepts and practices morph as engineers better understand how they can best meet the end user’s needs.
Putting the T in Mechatronics
When it was first introduced, mechatronics was generally perceived of as the integration of the mechanical and electrical disciplines. Recently, however, the engineering community has begun to see the methodology as a broader multidisciplinary effort that pulls together mechanical, electrical, software, and control (see Figure 1), along with problem-specific specialties, such as civil, biomedical, environmental, and chemical engineering.
To implement this multidisciplinary approach, designers must be familiar with the general principles and concerns of a broad range of engineering disciplines. This breadth enables the degree of collaboration called for by mechatronics.
“The modern engineer is what we call a T-shaped engineer,” says Kevin Craig, Robert C. Greenheck Chair in Engineering Design, Marquette University. “He has discipline depth but also multidisciplinary breadth….”
Now design innovators are casting their net even further to include additional areas of expertise. What makes this evolution so radical is that the new disciplines were not previously part of the design process.
Leading proponents of mechatronics now recognize that design problems cannot be solved by science, technology, engineering, and math alone. The problems must be solved through human-centered design, where the engineers understand the end users and their needs and the culture in which the device or machine is going to operate.
“Human-centered design includes people with business, social science, language, culture, and complexity training,” says Craig. “And forward-thinking companies are taking this approach. This is where solutions happen, and when innovation occurs.”
Only by adding the human element to the equation can the design team determine what is desirable. Once they do that, science, technology, engineering, and math will tell them what is feasible, and business will tell them what is viable and sustainable.
This shift in mechatronics is beginning to make the nontechnical skills just as important as the hard sciences in the design process. The challenge now is to achieve the right balance.
Shifting Culture
Even with the growing awareness of the multidisciplinary approach’s value, traditional mindsets still impede broad adoption of mechatronics. The greatest barrier is the silo structure that permeates the design cultures of many companies. The profile of narrowly focused engineers prevents mechatronics from reaching its full potential. Everyone knows what needs to be done. The challenge is making it happen.
The silver bullet that might do in design silos is the growing assertiveness of the major mechatronic practitioners and the influence they have on their suppliers. One example of this is the relationship Procter & Gamble—which makes the machines that make its products—is cultivating with Rockwell Automation, a major supplier of motors and drives.
P&G needed Rockwell to become a mechatronics-enabling supplier and a full design partner. That meant Rockwell would provide insight into how its products could best be incorporated into P&G’s designs. In doing so, P&G’s needs are met, and Rockwell gains a competitive advantage over other suppliers.
Most machine-building companies are small to mid-size, and they don’t have big engineering staffs. As a result, they need the level of advice and integration help that P&G was seeking. So if a supplier can provide that advice, its offerings become more valuable.
If the efficiency enhancements that mechatronics offers aren’t enough to make companies change their design culture, then perhaps lucrative ties with major machine makers will. If Walmart can require its suppliers to use RFID tags, then maybe machine makers can nudge their suppliers toward embracing mechatronics.
Ironically, another factor moving companies’ design culture toward mechatronics has been the economy. “I think the financial crisis helped a little bit because it gave people more time to step back and look at their development process,” says Christian Fritz, Product Manager for Motion Control and Mechatronics at National Instruments. “And the companies that had optimized their processes positioned themselves well for the downturn.”
Common Ground
Not all mechatronics concepts are new, but many of the established practices it incorporates must be adapted to accommodate the methodology’s multidisciplinary approach. For example, mechatronics is model-based design. But to really implement the methodology, engineers need a common modeling environment, where all the disciplines can interact and see how design requirements can be met with different or complimentary approaches.
“If you look at mechanical, electrical, and software engineering, the abstractions that each discipline uses to encode its ideas are very different,” says Gary K. Fedder, Director, Institute for Complex Engineered Systems, Carnegie Mellon University. “In most respects, the abstractions in one discipline don’t translate to the other disciplines. The common ground on which all can relate to each other is on the functional level.”
Tools for Change
Until recently, engineers were limited to a few tools that provided the functionality required to support mechatronics. “There are two main programs: MathWorks’ MATLAB, which is a leading model-based design tool, and National Instruments’ LabVIEW, which is predominantly focused on real-time measurement and control design,” says Marquette’s Craig.
Practitioners of mechatronics, however, can now point to a new generation of tools. “In the past, mechatronics was more about what engineers should do,” says Christian Fritz, Product Manager for Motion Control and Mechatronics at National Instruments. “But recently, tools have begun to emerge that enable the engineer to pursue mechatronics. Companies that provide design tools have started to extend their functionality to cover more than just one area. For example, companies that provide mechanical design tools have started to include control and motion simulation capabilities, or they are partnering with others to compliment their design tools with other tools.
“We’ve seen a number of major industrial suppliers of servo drives and mechanical components, such as gearboxes and timing belts, come out with their own electronic tool sets to calculate critical parameters and help size and select components,” says Stoyan Lokar, Associate Director of Mechanical & Materials Technologies at Procter & Gamble Corporate Engineering.
According to Lokar, Rockwell Automation has made a major update to its Motion Analyzer software, with much more functionality. And Wittenstein-Alpha (gearboxes), Zero-Max (couplings), and Gates (timing belts) have all updated their software and published critical data required for mechatronic analysis.
As you would expect, major design software vendors are also delivering mechatronics tools. “Over the past 12 months, National Instruments released a couple of features that help realize the mechatronic design approach,” says Fritz. “For example, we released some features in LabVIEW that allow you to implement real-time algorithms in a real-time embedded system….”
By themselves, mechatronics’ concepts and the design culture would probably change at a slow pace. But the introduction of tools designed specifically to support the methodology might speed things up.
“Better tools that are easier to use will mean more engineers capable of doing Mechatronic analysis early in the development cycle as a means of option analysis,” says P&G’s Lokar. This will require less and less prototyping of parallel paths. Engineering decisions can then be made based on models, then the models can be extended to higher fidelity and finally proven out on hardware that’s close to final design.”
More Info:
Gates Corp.
Contributing Editor Tom Kevan is DE’s sensors and embedded systems expert. Send your comments about this article to [email protected].
Subscribe to our FREE magazine,
FREE email newsletters or both!Latest News
About the Author

DE’s editors contribute news and new product announcements to Digital Engineering.
Press releases may be sent to them via [email protected].

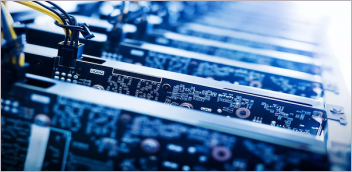
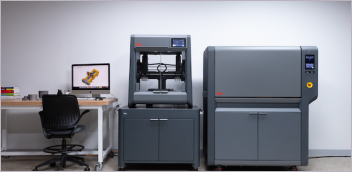
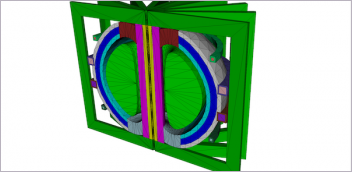