3D Printing Accelerates Cars into the Future
This hybrid car is the first prototype to have its entire body 3D printed by additive manufacturing.
Latest News
March 1, 2011
By Susan Smith
What if the car you drive was made with a sustainable design process, and saved you a bundle at the gas pump? Or maybe, you’re no longer going to the gas pump at all?
![]() Team Urbee poses at the recentSEMA show in Las Vegas. |
Both of those scenarios would be a benefit for our planet, as there is a finite resource of 1.258 trillion barrels of proven resources of oil in the world—and 20 million barrels of oil are currently being consumed daily in the U.S.
While several vehicle manufacturers are addressing this issue, KOR EcoLogic is among the leaders of the pack. Jim Kor, president and senior design engineer for the Winnipeg-based company, reports that his team’s low-energy, hybrid car is considered to be the first prototype ever to have its entire body 3D printed by additive manufacturing processes. All exterior components of the vehicle—including the glass panel prototypes—were created using Dimension 3D printers and Fortus 3D Production Systems at Stratasys’ digital manufacturing service, RedEye on Demand.
Blaine McFarlane, KOR EcoLogic’s senior design engineer, says the electric/liquid-fuel hybrid reaches more than 200 mpg, highway, and 100 mpg, city, in U.S. gallons with either gasoline or ethanol. That means the Urbee costs only 2 cents per mile for combined city and highway use, according to its creators. This is only about 10% of the fuel consumed by a typical sports utility vehicle (SUV). On the highway, the Urbee costs about 1 cent per mile, or 95% less than a typical SUV.
In terms of electrical energy, the car is charged overnight from any standard home electrical outlet. It can also be charged by renewable energy from a windmill or a solar-panel array that is small enough to fit on top of a single-car garage.
![]() The T.25 with Gordon Murray. |
Design Specifics
There are 10 panels in the body of the car, and it takes three weeks to build the parts. At press time, Kor and McFarlane had the door, the side, the nose and the back end of the body finished.
The car body panels are made of plastic and are 3D printed. These go on the car directly. However, the glass or windows of the car are also 3D printed out of solid plastic. These opaque windows are used as templates only, while Toronto-based Accura Glass Bending, Inc. makes the glass windows by hand. The glass windows then go onto the car, glued to the plastic body panels in the traditional way.
“We designed the parts to be low-energy; we designed an aerodynamic body,” says Kor. “We have two industrial designers on the project who are car stylists, and they were worried it would be too ugly with the aerodynamic body—the eye can’t follow the shape, etc. So they took all the aerodynamic specs and then made it look appealing without sacrificing aerodynamics.”
![]() The Urbee has already earned tremendous accolades: It competed in the 2010 X-Prize Competition, and is the topic of an upcoming episode of the Discovery Channel’s Daily Planet. The team was encouraged to take the design to SEMA, where people thought the body was machined. In addition, CNN News interviewed Jeff Hanson of Stratasys and Jim Kor, viewable online here . |
This was done by making a sculpted clay model of the car at 60% scale and then having it scanned into the computer. With the body in the computer, CD-adapco software was used for aerodynamic simulation, from which they derived a drag coefficient (Cd) of 0.15. The lower the number, the less horsepower needed to push the car through the air. By comparison, the Toyota Prius has a Cd of about 0.26.
After the aerodynamic simulation, the next step was to cut the computer model into body and glass panels, and verify the fit with the scale model. To accomplish this, the body panels were printed full-scale and the window templates were 3D printed full-scale to make glass windows.
The Urbee’s chassis is made of stainless steel for longevity. It is made of sheet metal and welded, which is like a traditional chassis used for vehicles, according to Kor. “We had the chassis moving to verify certain things, and then the body is fit over the metal chassis,” he says.
Kor says they were familiar with other processes before choosing rapid manufacturing. They had done fiberglass for other projects on buses and tractors, but they wanted the car to look like a real car with sharp edges.
“We wanted to adhere to a perfect shape that was aerodynamic,” he adds. “The other process requires months of labor, but this is pretty rapid for the designer. Those pieces are all done with minimal handwork at all in Minneapolis.”
Project History
Kor says the project itself is quite old. They have been working on it for about 15 years. KOR EcoLogic designers wrote their own software for designing the Urbee.
“The formulas are simple,” Kor says. “We did a typical city trip where you accelerate, you cruise, you decelerate, you stop. We made 100 trips and scenarios to make this faster or that a little heavier, and we got a deeper understanding of how that went.”
The Urbee project began with trip simulations, and the team did not have any preconceived ideas about what the car would look like, says Kor: “We followed the energy, just wanting to use the least energy to go get that liter of milk we are always running out of—whether the convenience store is a mile or 100 miles away from your home.”
KOR EcoLogic used Autodesk Inventor to design some of the parts, and Alias for most of the parts on the first prototyping.
Physical Prototyping
Rather than allowing the parts to be shipped, Kor says the team picks them up at RedEye in Minneapolis. “The first body panels are a little thicker than we expect in later panels,” he admits. “Also, we are just focused on body skin right now, and getting that correct. Later, body panels will have depth and likely include interior finishes as well.”
As a group, Kor adds, “we’re just learning the process ourselves. We’re learning how to make the panels very efficiently.”
In terms of continuing to manufacture with the Stratasys Fortus system, Kor says, “When I first talked to Stratasys, it seemed this process was perfect for prototyping. But as we move forward, production pieces are becoming more feasible—especially with advances in technology and as we all learn how to use this technology specifically for production parts.”
For a milling process, Kor says, the company would have to tool up, “but with this process we don’t have to tool up. 3D printing is completely flexible. If we had made fiberglass molds, change to the body would have been traumatic.”
“FDM is certainly suitable for limited production manufactured parts that will be installed to an automobile,” says Joe Hiemenz of Stratasys. “This is currently going on with a few high-end custom automobiles in Europe.”
This car may start out in limited production, which would mean additive manufacturing would be an excellent fit, Hiemenz says. “However, when the car goes into mass production, additive manufacturing will no longer make sense.”
Green from the Get Go
“Other hybrids on the road today were developed by applying ‘green’ standards to traditional vehicle formats,” says Kor. “Urbee was designed with environmentally sustainable principles dictating every step of its design. Urbee is the only practical car we’re aware of that can run solely on renewable energy.”
The team’s goal in designing the Urbee was to be as green as possible throughout the design and manufacturing processes, Kor says, and Stratasys’ FDM technology has been central to meeting that objective.
“FDM lets us eliminate tooling, machining and handwork, and it brings incredible efficiency when a design change is needed,” he adds. “If you can get to a pilot run without any tooling, you have advantages.”
Gordon Murray Design Takes Prototyping In-house At press time, the company was working on its T.27, an all-electric three-seater city car, made possible through an approximately $7 million investment from the government-backed Technology Strategy Board. Gordon Murray Design uses Stratasys FDM Fortus 400mc as its in-house machine because the team wanted to manage the entire design and prototyping process in-house. They use Fortus 400mc in the Prototype Workshop to build multiple components for tooling and design. According to Murray, FDM technology was primarily used for component design rather than body design, using ABSM30 as the material. Murray says the Stratasys FDM technology enables the team to embrace traditional CAD design processes in four ways:
The design software Gordon Murray Design used was Catia V5 Revision 17. Stratasys’ Fortus 3D Production System came into the picture as Gordon Murray Design sought to protect its intellectual property, have control over the overall design process and save on outsourcing costs. “We were initially using the machine (Fortus 400mc) as a design tool, but soon discovered that we could use it more and more for structural parts,” says Murray. “In fact, we’ve designed the entire of the T.25 interior using the Stratasys machine—including the instrument panel, sun visor, internal mirrors and internal trim. We expect to be able to do the same with our next project, the T.27.” “The lightweight philosophy of T.25 meant it achieved 96 mpg during the inaugural Brighton to London Future Car Challenge,” says Murray. “Had it been powered by diesel, it could have recorded 131 mpg.” |
More Info:
Accura Glass Bending, Inc.
Gordon Murray Design
KOR EcoLogic
RedEyeOnDemand
Stratasys
Contributing Editor Susan Smith has written and edited for various publications in the tech industry for more than 17 years. Send e-mail about this article to [email protected].
Subscribe to our FREE magazine,
FREE email newsletters or both!Latest News
About the Author

DE’s editors contribute news and new product announcements to Digital Engineering.
Press releases may be sent to them via [email protected].
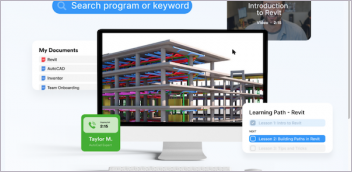

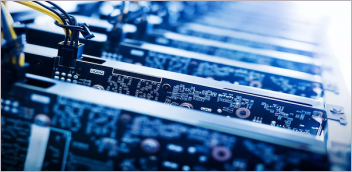
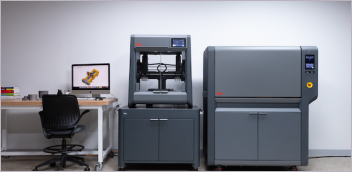