Latest News
August 20, 2014
Materialise has launched the 9.0 edition of 3-maticSTL, the latest version of its software suite for design modification and simplification, 3D texturing, remeshing and forward engineering at the STL level. 3-maticSTL 9.0 offers improvements in its design, remeshing, texturing and lightweight structure functionalities. New features and improvements reported by the company focus on rendering, robustness and usability. This update also enables users to create watertight designs that will ensure the quality of 3D printed parts, according to the company.

3-maticSTL is built around a core application for designing or repairing missing or badly scanned components and dedicated modules for creating textures, perforations and patterns as well as for creating lightweight structures. With this toolset, designers and engineers can prepare data for FEA (finite element analysis) and CFD (computational fluid dynamics) analyses, additive and rapid manufacturing and CAM (computer-aided manufacturing). 3-maticSTL also allows users to create scale models, wind tunnel models, concept models and similar models by making adjustments directly on a mesh.

The 3-maticSTL 9.0 Design module has been updated with a new render with ruler and automatic rib patterning capabilities. The new renderer, says the company, allows for faster model manipulation and visualization than earlier releases and offers improved transparency rendering and enhanced detail. The new automatic rib pattern functionality creates a clean rib structure that conforms to the 3D model.

Enhancements to curve manipulation tools in 3-maticSTL include a new Edit Curve feature that allows users to adjust the shape of a curve once it is created rather than requiring them to redraw the curve. Additionally, the Edit Curve Tangent feature lets users manipulate the tangent vector of a curve in 3D space to tangentially align the curve with a user-defined direction at the selected point. A Blend Curve feature creates a smooth connection between two entities. Other enhancements include a Lip and Groove Cut feature that automatically creates a Z-section in the “cutting” surface of a 3D model being split into two separate models, and improvements to the offset function’s algorithm now allows offsetting a whole part or selected surfaces.

The 3-maticSTL Lightweight Structures Module enables the design of lightweight structures as well as parts with variable flexibility and rigidness. Updates to this module in version 9.0 include the ability to create randomized porous structures, conformal structures and grid structures. With version 9.0, a design’s 3-matic graph lines can now be visualized as CAD files without converting the design to STL format.
The 3-maticSTL 9.0 Texturing module now offers slice-based and STL-based texturing capabilities. Slice-based texturing allows the user to go directly from a 2D texture on a 3D model to a slice export for a specific type of 3D printer, skipping STL conversion of the 2D textures entirely. A new 2D UV page provides controls in positioning and rescaling the 2D texture on a part.

The 3-maticSTL 9.0 suite also includes CAD import and remeshing modules. The CAD import module provides functionality for creating STL data from CATIA V4 and V5, PTC and Siemens PLM formats as well as IGES, STEP, VDA and VRML files. The Remesh module for preparing parts for CAE applications optimizes surface meshes using manual and automatic remesh operations and has a volume meshing functionality.
Materialise says that the 9.0 release of 3-maticSTL takes into account many of suggestions from its customers. 3-maticSTL will also become available through the Altair Partner Alliance later this year.
For more information of version 9.0 of 3-maticSTL, visit Materialise on the web.
Sign up and download the “What’s New in 3-maticSTL 9.0” brochure.
Learn more about 3-maticSTL for design applications.
Read some 3-maticSTL case studies.
Check out the system requirements for 3-maticSTL.
See why DE‘s Editors selected Materialise’s 3-maticSTL version 9.0 as their Pick of the Week.
Sources: Press materials received from the company and additional information gleaned from the company’s website.
Subscribe to our FREE magazine,
FREE email newsletters or both!Latest News
About the Author

Anthony J. Lockwood is Digital Engineering’s founding editor. He is now retired. Contact him via [email protected].
Follow DE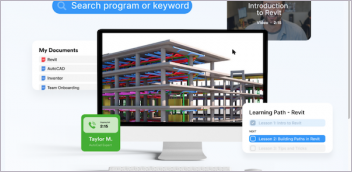

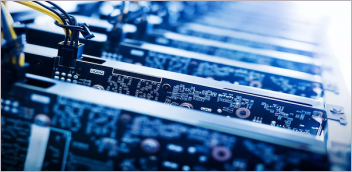
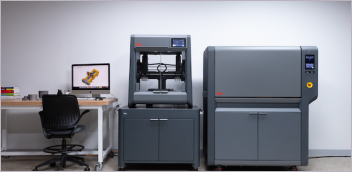