Sensor Data Meets Models

At LiveWorx 2015, PTC demonstrated the ability to stream sensor-captured real-time data to a ThingWorx interface. Image courtesy of PTC.
Latest News
June 1, 2015

The Big Brother in Orwell’s dystopia “1984” makes us associate monitoring with state-sponsored surveillance and totalitarianism, but today’s widespread availability of sensors and electronics is ushering in a different kind of monitoring, one that aims to improve workplace safety and industrial productivity.
At NIWeek 2014, National Instruments (NI) introduced a new product, NI InsightCM Enterprise. The company describes it as “a software solution with tightly integrated hardware options for monitoring critical and ancillary rotating equipment.” Siemens PLM Software, another company with strong links to manufacturing, offers a similar tool, dubbed Dimensional Planning & Validation (DPV). It’s part of the company’s Tecnomatix process planning and simulation suite.
Many large-scale manufacturers possess and maintain 3D models of their production facility and assets. A successful marriage of real-time feedback and digital models could catapult product and process engineering to new heights.
Eyes and Ears of the Plant
NI InsightCM Enterprise is designed to record industrial equipment conditions—such as rotation speeds, acceleration and failures—for trend analysis. The data-visualization environment lets you display the incidents from different devices and machines taken at specific time intervals in waveform, waterfall, full spectrum and other standard data-plotting formats. The method is expected to let facility managers not only see trends and patterns among the equipment but also to predict impending catastrophes and take preventive action.

Siemens describes DPV as “a closed-loop system for the real-time collection of measured quality data, which automates data collection, organization and reporting.” With such data, facility operators have a better chance of reducing scrap, rework and preventing losses.
“Real-time collection, analysis and reporting of measured quality data can help manufacturers to reduce their overall cost of quality,” writes Siemens’ press office. “Software tools like Tecnomatix DPV can be used to identify and resolve quality issues before they adversely affect product quality, operational productivity and warranty costs.” The company’s offering benefits from integration with its CAD software, which enables data and geometry to be displayed in the same environment.
Digital Avatars
In the last few years, CAD and PLM (product lifecycle management) vendor PTC has refashioned itself as an IoT (Internet of Things) product development company. In late 2013, the company acquired ThingWorx, a platform for building and running IoT applications. In late 2014, it also bought Axeda, which offers solutions to connect sensors to the cloud. The technology stack PTC received from these purchases has since become the cornerstone of the company’s IoT offerings.
“Very little about what happens in the physical world ever makes it back to the digital world. It’s been this way for decades … If you ask questions about your product like, ‘I wonder how it’s used’ or ‘I wonder how it’s working,’ there’s just silence,” said Jim Heppelmann, president and CEO of PTC, at the PTC LiveWorx 2015 conference in May.
That silence is about to be broken. The company has begun working to stream sensor-acquired data to the ThingWorx interface. A live demonstration took place on stage at LiveWorx. Mike Campbell, PTC’s executive vice president of CAD products, demonstrated what he called “the concept of a virtual twin, a product avatar,” using a mountain bike from Santa Cruz Bicycles. The sensors mounted on the bike were measuring the “wheel speed, cadence of the paddles, compression on different suspension mechanism and steering angle,” he says.
The real-time data from the sensors was fed into a ThingWorx dashboard for display, overlaid on the CAD model of the bicycle (Santa Cruz Bicycles uses PTC software for product design). The movements of the physical bike—its wheel spins, handlebar turns and frame tilts—were faithfully replicated by the 3D CAD model in the software. Furthermore, the demonstration showed sensor data could be projected into a live video feed of the bike in motion, in an iPad augmented reality app.
Finding Insights in Big Data
The desire to monitor and track manufacturing assets may force owners and operators to confront Big Data issues. “As intelligent industrial systems scale in number and complexity, the amount of data coming off of each sensor increases as well,” says Kamalina Srikant, senior project manager at NI.

Finding meaningful patterns and insights in the collected data is next to impossible with the naked eye. It requires algorithm-driven operations. “NI’s goal is to continue evolving and adding to the analytics that we have within the platform to provide more sophisticated and meaningful insights to users. Additionally, users have the option of integrating with third-party tools or tools like the Watchdog Agent (an NI tool on the LabVIEW Tools Network) to perform advanced predictive analytics or prognostics. With the emergence of the IoT, new technologies like smart sensors, the cloud, mobile devices and embedded intelligence are growing more prolific, meaning dependable data management, systems management and data analytics tools are more important than ever,” says Srikant.
Combining Data with Models
Also on the rise is the interest to create virtual counterparts of manufacturing facilities, driven by software that lets you create detailed 3D replicas of factories and plants as well as the content within. The use of photogrammetry and laser scanning makes it easy to create such models. Owners and operators often use the digital factory and plant replicas—usually constructed with CAD geometry, point cloud, or a mix of the two—to experiment with different manufacturing processes, identify possible clashes and collisions, or to verify ergonomic feasibility in the workflow.
The incorporation of real-time sensor-captured data into virtual factories and plants could elevate the type of process simulation possible to new heights. Displaying equipment health data that usually exists as pie charts, bar graphs, and spreadsheets in an immersive 3D environment could yield new insights into manufacturing processes. For now, however, the handshake between 3D models and real-time sensor data is not straightforward or easy. 3D models were initially developed to record geometric dimensions, not intended as the hub for real-time equipment data. However, the IoT movement and the resulting desire to harness the power of data in product development may change that.
Subscribe to our FREE magazine,
FREE email newsletters or both!Latest News
About the Author

Kenneth Wong is Digital Engineering’s resident blogger and senior editor. Email him at [email protected] or share your thoughts on this article at digitaleng.news/facebook.
Follow DE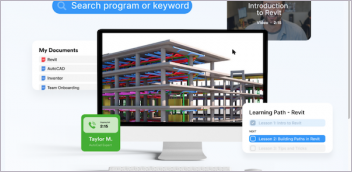

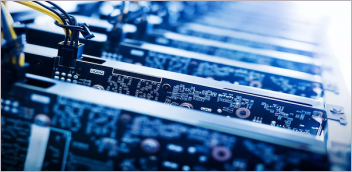
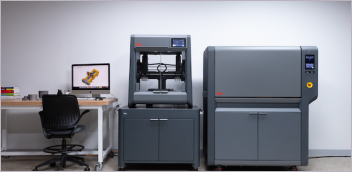