Latest News
May 1, 2005
Innovator Extraordinaire: The co-founder of DP Technology Corp. discusses his vision for the future of manufacturing.
By Ann Mazakas
This is the second in a series of interviews with leaders in the CAM industry. - DE Editors
Never one to let an opportunity pass him by, Dan Frayssinet was selling NC tools for a French software company when he set up his own software business to fill a need he saw in the industry. With the money he made from his first sale to a Hewlett-Packard plant in Oregon, he and partner Paul Ricard rented a small office in southern California and spent a year and a half designing and perfecting their well-known signature product, ESPRIT.
Starting with that success, Frayssinet and Ricard built DP Technology of Camarillo, CA, into a leading CAM software developer. Today, Frayssinet has more than two decades of experience producing machining technologies that have been integrated with DP Technology’s ESPRIT CAM software, a line of full-spectrum CAM solutions for multiaxis turning, advanced milling applications, and wire EDM. He holds a bachelor’s degree from the University of Lyon, France, a master’s in mechanical engineering, and an engineering license from Institut National des Science Appliquées (INSA) in Lyon.
We asked Frayssinet to explain the emerging application of ESPRIT and the new technologies that it’s being fitted with.
How do you see the design and manufacturing fields changing in the next few years?
Dan Frayssinet, DP Technology Corp. |
Frayssinet: What I envision is that manufacturing will become more closely linked to the upstream design process. For example, you design the part you want to make and just send it to the CNC machine tool. The vision is to have no operator interaction in between. Similar to the printer driver, it’s a machine tool driver. It’s ludicrous to think you should be working in NC code. It’s an obsolete concept when you compare what an NC machine is to some other disciplines. Stereolithography is a good example, where parts are produced with very little interaction from a CAM type of software. This type of process is relatively simple, so it’s easier to accomplish; but that’s the vision.
It’s a new concept because we want to remove all the detail that’s tedious at the machining level. Saving time was a primary driver, but now we see that a vast amount of manufacturing knowledge will, in time, go back to the designer in a real-time fashion. We don’t have the technology yet. ... It’s just a matter of time.
We’re taking practical steps toward that vision by focusing on six main design tools: SolidWorks, Solid Edge, Autodesk, Pro/Engineer, Unigraphics, and CATIA. These products represent the lion’s share of the mechanical parts that are designed worldwide. About 80 percent or more of designs are developed in those six systems. We focus on implementing KnowledgeBase concepts within the framework of those six CAD systems with ESPRIT being used as the CAM engine.
How does a manufacturing KnowledgeBase benefit design?
Frayssinet: A KnowledgeBase is a huge database that handles anything from materials, machine tools, cutting tools, fixtures, speeds and feeds, processes and so on and then is smart enough to analyze the model and make a decision based upon the quality of what you want to make, what it is made of, and what tools you have to make it. So when you take all this information, that’s the concept of a KnowledgeBase.
This will benefit engineering as time goes by because people are starting to gather knowledge within their own factory on how they make things with the tools they have. Until now, knowledge was dispersed on a network or on paper or even on a computer and was more likely to be instructions, not something that could make a decision. Now, with a KnowledgeBase system, you can teach the system about the tools you have, the materials you have, and the processes you use to get the quality and types of parts you want to make. With all this manufacturing knowledge stored within the system, the next step is to take this manufacturing knowledge and plug it back into the CAD system at the design level.
When I print, I can choose any printer on my network and adjust its properties. Does a knowledgeBase give me the same control?
Frayssinet: The biggest parallel is when a new design is machined in a prototype shop. I go iteratively through the machining process until I’m happy with the prototype. The process used to machine the prototype is stored in the KnowledgeBase. Now, I need to take that prototype and put it on the production floor with a big horizontal machine that’s equipped with a pallet. It’s very important to duplicate the process exactly to get the same result.
A KnowledgeBase will do that for you. It will duplicate the final prototype, but it will adapt to the machine you choose. Instead of using the tools and operation settings from the first machine, it will take the process and adapt it to the tools and capabilities of the production machine. What remain constant are the quality and the geometric information of the design model. Based on the desired quality and the material and the part itself, the system will decide what types of tools to use and what tools are available in that type of machine. The system learns and, as the process changes, the system adapts.
Can people use this technology out on the shop floor directly at the machine?
Frayssinet: Typically companies don’t want programs changed in the factory. But in a prototyping environment, it’s very useful. They try something, then try something else. Since the process is stored in the database, the system relearns the process. The programmer creates the original NC program and then the shop adjusts a few things because it’s a better way to go. Not only is the part program updated, but the database is updated as well. Instead of changing the NC code, they change the process so you don’t lose information. You learn from your mistakes to make the process better.
When are you planning ESPRIT’s next release?
Frayssinet: We have a major release every year. The international release of ESPRIT 2006 is planned for fall 2005. This release includes even more improvements to the ESPRIT KnowledgeBase. We have two patents pending on our technology.
In our upcoming release, the feature trees in the CAD systems will be directly available in ESPRIT. This is a key factor in taking more complete design information into the CAM system. It gives you more understanding of what you’re going to make because you can see the design intent. It’s no longer acceptable to be working with basic geometric information anymore. There is a more complete flow of information, which will result in a lot of productivity.
One of the consequences of this communication is that you can deal with more complex processes than ever before. It changes the market for manufacturers. For example, until the last year or so, multiaxis machines and mill/turn combinations were primarily used in production because they were difficult to program and run. Now, our technology automates this so you can create an NC program for a part very quickly. Instead of using these multitask machines strictly for production, it makes them easier to use by a wider range of people.
This works well for standard milled parts, but what about other types of machining?
Frayssinet: It applies to milling, turning, anything. It’s just that the processes are different. That’s the core competency of a KnowledgeBase system. In mold making, the most time-consuming aspect is the prismatic machining of holes and pockets. This is a very good example of what could be printer-driver oriented. In a mold shop, the geometry of the cavity and core can change dramatically, but when you look at the bases, there’s a lot of similarity. With today’s technology, that can be totally automatic. This is a great example of where the feature tree is very useful because you can see the different types of prismatic shapes.
With surface milling, the efficiencies achieved are less dramatic. At this point, KnowledgeBase technology applies primarily to the prismatic and EDM worlds and, to a lesser extent, the turning world. When you start with the development of a product, you start where you think you can have the most impact. As the technology matures, it spreads and applies to more applications. I fully expect that in the next couple of years you’ll see true 5-axis work included.
Ann Mazakas is the president of Intelligent Creations LLC. You can reach her regarding this article via e-mail sent to [email protected].
Subscribe to our FREE magazine,
FREE email newsletters or both!Latest News
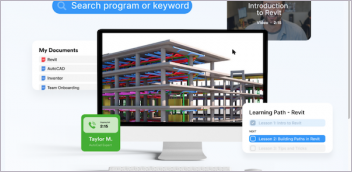

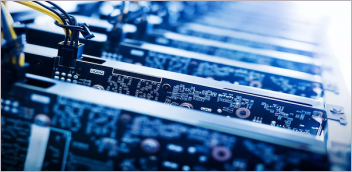
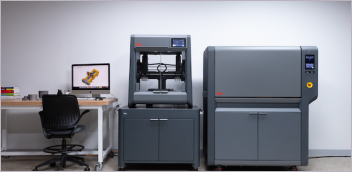