
Simulating a fuselage section in SIMSOLID, a simulation program from Altair. Image courtesy of Altair.
Latest News
June 30, 2022
John Chawner is an aerospace engineer by training, but he also refers to himself as a CFD (computational fluid dynamics) entertainer. From 1994 to 2021, he ran Pointwise, specializing in mesh generation for CFD programs. Some simulation veterans refer to him as “the mesh guy,” a moniker he is proud to wear.
“Is there a difference between novice- and expert-level simulation? Yes, there is. Is the dividing line clear? Probably not,” he observes. The line in the sand keeps shifting because, as more CAD users become well-versed in finite element analysis (FEA) and the software gets better at automation, what’s considered “easy” or “difficult” also changes.
The recalibration is not just in semantics but also in the functions of the so-called “novices” and “experts.” As efforts to democratize simulation gain momentum, FEA veterans found themselves taking on a new role—as template and app authors.
Insightful Error Messages
In 2021, electronics design software maker Cadence Design Systems made two strategic acquisitions: multiphysics CFD software maker NUMECA and Pointwise. Both are part of the Cadence multiphysics system analysis portfolio. Chawner is now the senior group director of CFD product management.
“You do want to give the designers on the front line—the ones designing your planes, trains and automobiles—as many simulation tools as possible so they understand the performance of their design. Preliminary design is when you have the best opportunity to correct your design at a low cost,” says Chawner. “But the users need to understand the acceptable range of usage.”
Automated tools might sometimes crash or fail, but Chawner thinks it’s important for the tool to provide an explanation—a meaningful error message.
“What good is that if it cannot tell you why it fails?” he asked, rhetorically.
“It’s also important for us to provide guardrails so non-expert users are clear about when they can use the automated tool, and when they can’t,” he adds. An automated meshing tool designed for dealing with fighter jet topology, for example, should have built-in safeguards to reject those who try to import and mesh a helicopter or a passenger jet model.
Chawner points out that even expert users enjoy using automated meshing tools, imperfect as they may be.
“It can get 90% of the job done, so they only have to manually tweak 10%,” he says. “They also like it because they can set up the job in a repeatable template so their junior associates can use it safely.”
With such a template, there’s also an opportunity to add a quality assurance layer to ensure the model, mesh and simulation complies with not just industry best practices but also the internal policies of the company— such as limiting material choices to those from the approved vendors.
Automation in meshing is constantly improving, but with machine learning, it’s accelerating, Chawner notes.
“If there’s a direct coupling with the CAD system, if the parts are correctly tagged as upper wing, lower wing, trailing edge, fuselage, for example, then the built-in intelligence from machine learning improves what you get from the automated application,” he says.
Novices Grow Up to Become Experts
Brett Chouinard, chief product and strategy officer at Altair, believes the term “simulation expert” has evolved over time. Perhaps it’s a sign that the industry’s collective efforts to broaden FEA expertise have largely succeeded.
“What was considered ‘expert analysis’ 10 years ago, is commonplace today,” he observes. He also points out many of the automation in the design software programs, introduced incrementally over time, have now become so ingrained that the users have forgotten they once had to manually do them.
“Before, you had to manually check to make sure your model is solid. Now, that’s done automatically for you. The software makes sure your model meets certain pre-simulation benchmarks,” he says.
In 2018, Altair acquired SIMSOLID, which champions meshless FEA. According to the announcement, “SIMSOLID controls solution accuracy using multi-pass adaptive analysis, making it extremely fast and memory efficient.”
When it first launched, SIMSOLID’s approach was a departure from many other FEA products. From the start, it was able to let users skip the meshing process and automatically prepare assemblies for simulation with little or no need to specify the types of assembly mates and joints.
There is, however, a difference between the software’s brute-force approach and an FEA expert’s considered approach. The software might fill a given geometric volume with all-purpose tetrahedral meshes with varying density based on stress distribution, whereas an expert might use simple meshes for primitive shapes and finer meshes for detected curvatures. They may also use a mix of solid and beam elements when appropriate. The expert could retain certain holes and rounded corners if they feel such holes are critical to the part’s performance. By contrast, designer-targeted preprocessors generally remove such features to simplify the geometry and save computing time.
“The more rules you want to follow, the more judgment it requires, the harder it gets to automate,” says Chouinard. “But every year, our software is getting better, so it requires less and less manual intervention. We are getting to the point where the software can correctly guess your assembly contact types 90% of the time.”
Guided by Purpose
Automation usually comes with generalized assumptions and approximations. Rahul Patil, product manager for Autodesk Fusion 360, believes the purpose of the simulation is a good indicator for how much generalization is acceptable.
“If you have 10 variations of a design and you just want to do a quick analysis on each to narrow them down to five, or you want to do a check for possible failure in injection molding, we believe there are certain things that should be automated. Things like meshing and detecting types of joints and assembly contacts are pretty straightforward to automate,” he says. “But we also leave room for you to edit the automated setup. If you believe you need finer meshes in one area, you can manually edit the meshes.”
An average designer with limited exposure to injection molding might not be able to identify the optimal point to inject the liquid into the mold. On the other hand, the knowledge is intuitive to those who regularly work with injection molding.
“That’s why, in the designer-targeted Fusion 360’s mold simulation workspace, the option to specify the injection point is not there; the software automatically adds it for you. But it’s customizable in the expert level Moldflow product,” says Kristen Kilroy, product marketing manager for Autodesk Moldflow.
Simulation to ascertain crucial product performance questions might be expert territory, Patil says. “If you need to know how the loads and constraints affect the deflection you see in the design, how a different type of material might behave and if you’re dealing with anisotropic materials or nonlinear behaviors, then an expert might need to intervene and validate the results.”
Through a voluntary opt-in program, Autodesk also gathers information about how software users navigate the many tasks, commands and tabs available to them.
“The data shows where the users tend to get stuck, what they do repeatedly, and so on, so it helps us decide what to automate, where to offer recommendations in the UI [user interface],” says Patil.
Emerging startup simulationHub offers browser-based simulation apps through Autodesk’s software development platform Autodesk Forge. The company’s current offerings are limited to just a handful of modules. For example, the company provides CFD apps to simulate flows inside a valve or an engine exhaust manifold. They’re offered under subscription plans, beginning at $500 a month.
simulationHub’s business model exemplifies an Apple app store-style market, where experts can develop highly automated FEA apps and offer them under the pay-per-use model. Patil believes that in the future, such apps may be coming from vendors such as Autodesk and also from expert simulation software users.
The advantage of Fusion 360, Patil points out, is the common data model used by the designer and the expert.
“You don’t need to keep a dividing line between designers and experts. We have bridges between the two; their workflows are more connected than ever,” he adds.
A Cautionary Note on Reduced Order Models
Subham Sett, VP of multiphysics solutions group at Hexagon Manufacturing Intelligence, points to a part’s mission-critical nature as one way to decide if the analysis is a candidate for simplified simulation.
“Think about an aircraft’s overhead luggage compartment. It bears some loads but it’s not as mission critical as, say, the landing gear. So you can have some liberty with it; you can let a designer handle its simulation,” he notes. “But the landing gear is a complex multibody system with multiphysics interactions. I’d be cautious about giving it to a designer.”
Many components are analyzed in isolation, but Sett points out that, in the finished product, components don’t operate in isolation. “They are part of a larger system. So design is moving toward system-level thinking,” he says.
At the system level, Sett believes a reduced-order model (ROM) might be the key to broadening use of simulation. A ROM is a simplified version of a complex system (such as an aircraft’s electromechanical operations) that can be used for predictive simulation and analyses. As on-demand computing power becomes more affordable, use of machine learning to develop ROMs is becoming common. Compared to a full-fledged physics-based model, a ROM demands less computation in simulation, but users must also acknowledge and accept certain approximations.
For example, an analysis expert can develop a ROM that accounts for the complex electrical, thermal and chemical interactions of an electric vehicle’s battery for a battery package designer who needs to perform routine analyses.
“If there are corner cases and outlier cases [outside the scope of the ROM’s intended use], you need to consult with the expert,” says Sett.
Dramatic changes in conditions, such as the substitution of one metal for another or the switch to composite frames for internal structures, could make the existing simulation model unreliable, he warns.
Hexagon acquired simulation software maker MSC Software in 2017. Two years later, it acquired AMendate, a Germany-based generative design and optimization software developer targeting designers.
The technology from both purchases is now in a new offering dubbed MSCOne from Hexagon Manufacturing Intelligence (MI). MSCOne’s modern UI makes Hexagon’s powerful solvers like MSC Apex, MSC Adams and MSC Nastran more accessible, Sett notes.
Understanding the Expert-Authored App
Phil Kinnane, senior VP of sales, COMSOL, points out that, in the conceptual design phase, designers do not necessarily need to start with a fully physical 3D model. “You can start off with simulation on a 1D or 2D model before you move up to 3D,” he says.
Reducing the number of physics involved to represent the event is also another option to save computing time and cost. But all of these involve varying degrees of compromises.
COMSOL’s option to make complex multiphysics simulation more accessible is through expert-authored templates, created in the Application Builder (part of COMSOL Multiphysics software) and publishable on the COMSOL Server. With this approach, “the user doesn’t need to be a physicist with a PhD,” he says. “The expert can set up an interface with only certain fields and inputs exposed. The rest of the simulation steps, like meshing [and] choosing the solvers, are still part of the simulation app, but not accessible.”
But the apps may contain certain blind spots for the users, Kinnane warns. “The expert might have built an app with an underlying model that’s valid for vehicles traveling between 10 km to 60 km per hour. If a user doesn’t know it, they might use it to simulate a scenario outside of that,” he says.
In such a case, the app may not provide a realistic solution—and, perhaps worse, produce an outcome that’s unreliable without any hint of an error. Therefore, such simulation apps should explicitly spell out the acceptable scope of use, or forbid invalid input entries in the UI itself, Kinnane suggests.
Ideally, the app’s UI should also allow the regular users to provide feedback to the expert author for refinement, he adds. “Maybe the user in the field can tell the simulation expert that the range of temperatures in the model is unrealistic. Material properties in Arizona versus New England, for example, need to be treated differently for more appropriate descriptions.”
Reading the Oracle
Chawner thinks that, in the future, automated meshing apps may become smart enough to offer “adaptive meshing”—starting the CFD job with rudimentary meshes but refining them in response to the CFD results.
“The idea is, the software can start off with clunky meshes and as the CFD job runs, the flow solver can evaluate discretization and other errors, look at gradients in the flow or apply adjoint techniques to the evolving flow and improve the mesh by adding or moving points along the way, ultimately converging to an accurate solution,” he explains.
There is, however, an area of simulation where automation cannot replace an expert’s judgment. “It’s the interpretation of the simulation results,” Altair’s Chouinard says. “Designers can look at the results and tell if the part meets the required safety factor, or the stress is below a certain limit, but they may not understand the complex failure mechanism.”
More Altair Coverage
More Autodesk Coverage
More Cadence Coverage
More COMSOL Coverage
More Hexagon Manufacturing Intelligence Coverage
Subscribe to our FREE magazine,
FREE email newsletters or both!Latest News
About the Author

Kenneth Wong is Digital Engineering’s resident blogger and senior editor. Email him at [email protected] or share your thoughts on this article at digitaleng.news/facebook.
Follow DE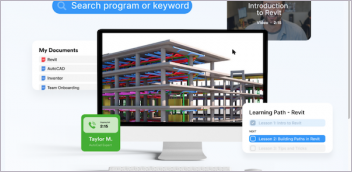

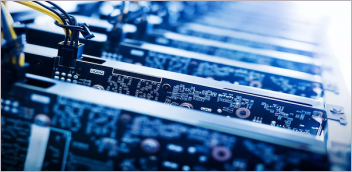
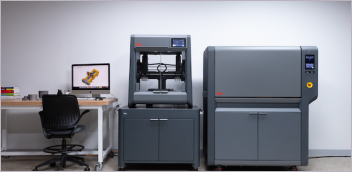