Evaluate Testing Services

Ultrahigh Temperature Scanning Probe. Image courtesy of NIST.
Latest News
September 1, 2018
At the National Institute of Standards and Technology (NIST), scientists and engineers are developing a nanoscale coating for solar cells. The coating, applied with a technique that can be incorporated into manufacturing, opens a new path for developing low-cost, high-efficiency solar cells with abundant, renewable and environmentally friendly materials.
Using laser as a light source to excite individual nanoresonators in the coating, the team found that the coated solar cells absorbed, on average, 20% more visible sunlight than bare cells or uncoated devices. The measurements also revealed that the coated cells produced about 20% more current.
The beauty of science and the merits of engineering design rely heavily on the accuracy and results of testing.
Whether the testing laboratories are simple or sophisticated, engineering design teams rely on the fidelity of labs and testing services companies that can provide full and reliable testing. However, there are numerous considerations when evaluating a testing service and laboratory.
As new technology is constantly being introduced, labs and their testing services expand and become more in-depth. Innovation and product development lifecycles are highly dependent on such technologies.
“We all recognize the many societal benefits offered by technology, from cloud computing, big data, machine learning and artificial intelligence, to augmented reality and various types of mobile platforms,” says Jay Alexander, senior vice president and chief technology officer at Keysight Technologies, which provides testing and prototype development assistance with software and testing services. “But gaining the full value of these new technologies requires deep expertise across the whole design and test workflow, plus the measurement expertise to effectively implement them.”
Understanding what technologies are needed for product development efforts is paramount. Devising a means of evaluating the testing hardware is necessary. But it’s even more important to look at the operation of the company, its facilities and its essential processes, then develop an objective way to measure them as a basis for evaluation.
The test workflow, however, has parameters that can be reviewed and monitored in trying to forge the strongest partnership with a testing services company. This means focusing on key areas to evaluate before the prototype goes to the lab.
Response Time
Time to market is always critical for any new product development and product lifecycle discussion. Part of the rubric that aids time to market is getting the best possible grip on the testing vendor’s turnaround time.
Testing can sometimes serve as the time period where the product lifecycle may make up ground to make launch dates. Therefore, it’s critical to know and understand the average turnaround time of any vendor.
“Engineering and design efforts inevitably take longer than anticipated, yet the product launch date doesn’t change, so testing is often expected to make up the difference,” says Jared McInelly, engineer solutions director at engineering firm Fresh Consulting. “If you know this, you can plan for it. Utilizing testing services that can give you accurate turnaround time that fits your schedule is important. Be ready to pay more for quicker turn times—some companies will offer this as a service, and it can be referred to as “next-on-bench.”
Cost Considerations
Cost always enters the equation in testing new products and designs. Some test methods can be quite sophisticated and require complex test equipment. Laboratories may require special materials and other supporting equipment to test certain designs. It’s important to understand the total cost of testing and what effect it will have on product development cost. This may vary also, depending on the volume of testing conducted.
“Make sure to ask for volume discount breaks,” McInelly adds. Large-batch testing allows the vendor to achieve economies of scale; setup time can be amortized across many units, for instance. This lowers the testing service provider’s costs. If there are ways to save the testing company money, it’s appropriate to ask for some of that savings to be applied.
Capability and Certification
Not all testing services are created equal. Some have calibration equipment, as well as test equipment used for various applications. Depending on what is needed, it’s important to survey the equipment capabilities as well as the knowledge base of the company or organization. In the case of NIST’s solar cells and their coatings, certain sophisticated test equipment would be required to adequately test and evaluate them to achieve a valuable proof of concept.
Facilities that perform functions such as calibrations often follow certain industry standards. This may be an ISO standard and the equipment and laboratory must be audited, evaluated and certified. Depending on what is needed, it’s important to ask questions regarding their certification, who issues them and how long they’re valid.
This may also serve as a basis of comparison when evaluating multiple labs or facilities to ensure their practices are comparable.
Management Processes
Another important consideration is the company’s management and how it operates. In evaluating a service company, evaluate how many subcontractors they have and how they are used. Myriad other questions may be posed about the way the company handles deliverables, reports and how long things take. It’s best to develop a checklist regarding management practices and combine such a list with individual lists related to capability, certification and testing processes.
There’s a long list of items to inquire about in evaluating potential testing firms. In general, in selecting a testing services provider, it’s important to be aware of any downsides of the firm. “You’ll know if they have tested similar products and have experienced the trade-offs and gotchas that come with testing a product like yours,” McInelly says. “This kind of knowledge is difficult to make up and their response should give you a solid reading of their true capabilities.”
The discussion will also impart the ability to anticipate where testing might be difficult and allow one to better “design for test,” saving time and costs.
Understanding the test provider’s weaknesses puts companies in a partnership with the test provider, according to McInelly. “You are looking to them for expertise and you are open to their ideas and suggestions,” he says. “It opens a dialogue between you and the test provider that can lead to a good, transparent partnership. Things will go wrong and there will be difficult engineering problems to solve as the project progresses.”
All told, a testing services company is a critical partner for any design team. It’s important to know their infrastructure and their strengths and weaknesses. It will prepare the team and their products for the challenges of the marketplace that lie ahead.
“Having a strong relationship built on transparent and open communication with a test provider is crucial in meeting time-to-market and cost demands,” McInelly says.
More Keysight Technologies Coverage
Subscribe to our FREE magazine,
FREE email newsletters or both!Latest News
About the Author

Jim Romeo is a freelance writer based in Chesapeake, VA. Send e-mail about this article to [email protected].
Follow DE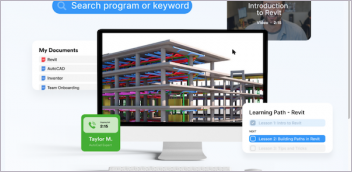

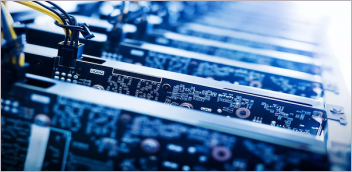
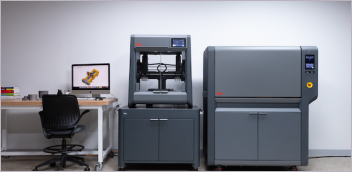