Editor’s Pick: Digimat 2017.0

In version 2017.0, the Digimat-RP Solution for analyzing reinforced plastic parts has been enhanced with new extended support for widely deployed FEA (finite element analysis) systems. Image courtesy of e-Xstream engineering SA.
Latest News
January 25, 2017
If it weren’t for computers, some things would be quickly categorized as “easier said than done.” Take modeling how a composite material or plastic will behave on the microstructural level so that you can predict how your material will perform in its intended real-world environment. Today’s Pick of the Week takes a look at the latest release of a suite of software widely used for composites and plastics design, development and processing.
The Digimat suite of nonlinear, multiscale material and structure modeling software from e-Xstream engineering is a go-to system in industries as diverse as aerospace, automotive, consumer electronics and medical devices. In broad strokes, the Digimat suite organizes its components in categories labeled Tools, Solutions and eXpertise.The latter is a catchall for knowledge sources, examples, training and support. Tools are interoperable applications for experts engaged in material or structural engineering or both on microscopic and macroscopic scales. Solutions are the tools for non-experts. They guide you through all kinds of tasks such as analyzing reinforced plastic or designing honeycomb composite sandwich panels.
The company just released Digimat 2017.0, and it sounds like there are a bunch of goodies for Tool and Solutions users. A key new capability lets you perform progressive failure analyses of short fiber reinforced plastic (SFRP) parts with implicit FEA (finite element analysis) solvers, which should help you predict the ultimate part strength without additional testing.
The Digimat-RP Solution, the Digimat-FE Tool and the Digimat-MX public material database see some big additions. The Digimat-RP Solution for analyzing reinforced plastic parts offers new interface support for RADIOSS/Shell, OptiStruct and Permas FEA systems, which should make for more accurate results and efficient workflows.
The Digimat-FE Tool for computing the performance of composite materials can now model discontinuous fiber composites (DFC) inter-chip delamination. It also has new woven 3D geometries, meaning you can define most common weave patterns for orthogonal and interlock woven 3D materials.

The Digimat-MX materials database has been extended with new ready-to-run models from DSM and DuPont Performance Materials. Digimat-MX also supports automatic reverse engineering of unidirectional and woven PFA models.
Digimat 2017.0 also debuts new capabilities in its Digimat-MF (mean-field homogenization) Tool and its Digimat-VA (virtual allowables) Solution that could boost efficiency and improve workflows. You can read more about that in today’s Pick of the Week write-up. Download the release notes linked at the end for the full skinny. Definitely worth the effort.
Thanks, Pal. – Lockwood
Anthony J. Lockwood
Editor at Large, DE
Subscribe to our FREE magazine,
FREE email newsletters or both!Latest News
About the Author

Anthony J. Lockwood is Digital Engineering’s founding editor. He is now retired. Contact him via [email protected].
Follow DE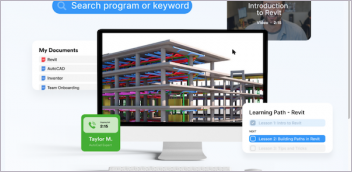

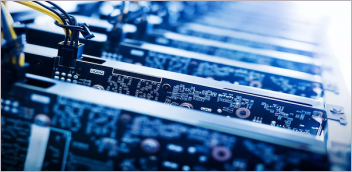
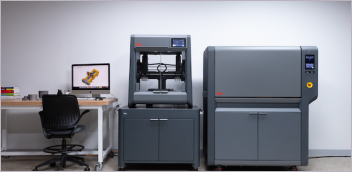