
An Amcor design, ready for analysis in the Impact Simulation Director. Image courtesy of Altair.
Latest News
July 1, 2015
In today’s remarkably competitive markets, the packaging industry needs to be highly responsive to the changing industry they operate in. New products are being produced all the time, and packaging professionals must maintain a fine balance between packaging performance, environmental impact and shelf appeal while keeping costs to a minimum.
Headquartered in Ann Arbor, MI, with over 59 manufacturing plants in 13 counties and over 6,000 employees, Amcor Rigid Plastics is a leading product supplier for food, beverage, healthcare, personal and homecare packaging segments. Working within the rigid plastics industry the demand for sustainable practices are high. The industry is under pressure to create more environmentally friendly products.
Packaging is often maligned, even considered environmentally unkind. It typically makes up a small cost of the overall product and is considered a disposable item However, if the package does not meet its requirements then spoilage can occur, or even food safety can be compromised, with much higher costs.
Amcor is continually looking for innovative and lightweight container designs that would be aesthetically pleasant and have easy handling for the consumer without compromising the quality, performance or safety. Simulation plays a major role in ensuring Amcor’s lightweight packages meet the functionality requirements.
Long-time users of Altair’s HyperWorks suite, the Amcor team was using the software to create accurate finite element models of the concept designs from the CAD teams in order to assess their performance in the virtual world. Amcor wanted to explore ways that it could accelerate engineering and analysis tasks associated with the development of new packaging products.
The Amcor team met with Altair ProductDesign’s Enterprise Solution Group (ESG), a team that specializes in assessing and improving product development processes and workflows. The ESG team worked with Amcor’s simulation specialists to identify where time and costs could be saved within the design process. The team discovered that the virtual test process used to investigate the performance of new packaging designs tied up a large amount of the simulation team’s time. To accelerate this process, Altair ProductDesign suggested that Amcor could take advantage of the Impact Simulation Director.
Applying the Impact Simulation Director
The Impact Simulation Director, or ISD, automates the laborious, manual tasks associated with model setup, analysis, post-processing and reporting. When tailored to an organization’s specific procedures and best practices, the ISD is designed to reduce development time and costs while enhancing product robustness and performance.
Altair ProductDesign worked closely with Amcor’s team to understand the existing impact simulation process in order to identify how the ISD could be best implemented to avoid disruption to the ongoing product development cycle. On-site training sessions were organized to help achieve a quick and effective adoption of the solution.
Once implemented, the ISD was able to accelerate the modeling process by allowing the user to define mesh criteria for each part, automatically mesh the model and then quickly check mesh quality and status. Amcor’s users can assign materials and properties to all the parts according to the solver specific material file as well as checking and fixing penetrations and interference for all the parts and sub-assemblies.
The solution guides the analyst through the impact simulation process, creating solver decks from CAD geometry for a wide variety of analyses. For Amcor, this included Empty Vented Top Load – where the empty bottle is analyzed for a buckling load, Filled Capped Top Load, where the fluid will be filled in the bottle, capped and analyzed for buckling load, Vacuum Response, which tests the container to see if the container is able to absorb vacuum, and Fill Pressure checks to see if the container is able to withstand the filling pressure.
Reducing Manual Effort from Hours Down to Minutes
What used to be a long, tedious practice that would have taken Amcor’s team as long as a few hours, has been simplified to a matter of minutes using the ISD solution. The team has been able to save a considerable amount time during the virtual test stage. For example, the company estimates that its team is now 60% more efficient in the pre-processing stage since implementing the solution for the simplest cases.
By accelerating the crucial performance analysis stage, Amcor is now able to allow its engineers and designers to focus more on research and development for future projects. In an industry where innovation is key, this is a big bonus for Amcor whose engineers no longer need to spend a large amount of their time modeling products and setting up analysis studies.
Amcor and Altair ProductDesign are currently in the process of creating more refinements to increase the range of containers that the tool can handle and we are looking forward to complete automation of the pre-processing in the future.
More Info:
Subscribe to our FREE magazine,
FREE email newsletters or both!Latest News
About the Author

DE’s editors contribute news and new product announcements to Digital Engineering.
Press releases may be sent to them via [email protected].
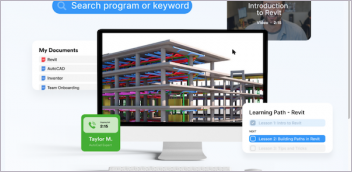

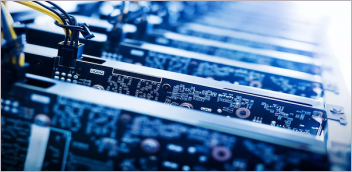
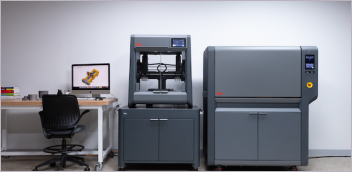