
Autodesk CEO Andrew Anagnost delivers keynote at AU 2018. Image courtesy of Autodesk.
AU 2018: Fusing Generative Design with Manufacturing Constraints
Autodesk University user conference highlights efforts to perfect generative design in Autodesk Fusion 360
Latest News
November 20, 2018
Generative design—AI-like software that can suggest the best geometry for a project—seems well on its way to reshape the design software sector. But where it is heading?
Last week, at its annual user conference Autodesk University (AU 2018, Las Vegas, Nevada, November 11-15) that attracted more than 11,000 attendees, design software giant Autodesk reveals the direction for its generative design implementation, as part of the cloud-straddling CAD-CAM-CAE software suite Autodesk Fusion 360.
During Day Two's keynote, Greg Fallon, VP of Design and Manufacturing Business Strategy, Autodesk, said, generative design “automates the ideation process, giving the user the ability to easily explore all valid geometric options for a given set of materials, manufacturing processes, and operating conditions.”
Adding manufacturing constraints as generative input means the software will consider, in addition to the assigned material properties and stress loads, the practical needs of certain manufacturing methods, such as milling or 3D printing.
A strategy adopted by a leading software developer, this represents the general direction of generative design not just for Autodesk but for the design and simulation software industry itself.
(A live streamed version of the AU 2018 keynote is available below.)
Generative Design 2.0 with Manufacturing Constraints
In a company blog post, Fallon describes the company's vision. “We see the convergence of design and manufacturing as the inevitable—and beneficial—future of making products. We see our customers embracing this evolution and, for our part, we’re pushing to accelerate it,” he says.
One way the convergence happens is in the manufacturing constraints added to Autodesk Fusion 360, a comprehensive software suite covering design and simulation to manufacturing. “We are in development to expand the manufacturing constraints for Autodesk generative design technology to include 2- and 2.5-axis machining,” says Fallon.
This augments the existing manufacturing constraints—3- and 5-axis milling constraints.
Because the computer-proposed topology is often impractical or impossible to be manufactured, designers using generative design have to spend time and effort refining the geometry in CAD. Additional support for manufacturing constraints reduce the rework, removing more barriers from large scale adoption of generative design.
Newer startups that focus on generative design, such as Frustum, have also taken a similar approach. For example, in Frustum Generate software Version 1.4, you can control the extrusion direction, which produces topology favorable to specific types of millings; and you can also prevent overhangs, which produces topology less prone to problems in additive manufacturing.
NASA's Moonlander Shaped by Generative Design
One of the highlights of this year's AU keynote was the presentation of the NASA Jet Proppulsion Laboratory's (JPL) concept lander, designed in Autodesk generative design.
The Autodesk-NASA collaboration gave the project team a chance to use generative design to explore structural designs, specifically for the frames and regions that hold the scientific equipment, Autodesk writes in a blog post. The final design was 35% smaller in mass compared to the original baseline design, the company states.
“We had developed a custom version of our software for high performance motorsports that enabled us to help our customers solve for multiple constraints at once. We then applied it to the problems JPL needed to consider,” said Mark Davis, the senior director of industry research at Autodesk. (Image below shows the NASA JPL lander as presented on stage at AU 2018, image courtesy of Autodesk PR.)

Partnership with HP
Generative design practitioners often look to additive manufacturing as the ideal method—sometimes the only method—to manufacturer the organic, assymetrical shapes suggested by the software. To that end, Autodesk supports the workflow with tools in Netfabb software, which targets the additive manufacturing industry, to produce generative design projects.
At AU, the company also announced partnerships with HP, to connects HP Multijet Fusion 3D printers to Autodesk software; and GE Additive, to facilitate metal-based 3D printing on GE machines.
Forge a Development Platform
The first day of AU was devoted to Autodesk Forge, an application development platform that the company uses to create its own software stacks. In the recent years, the company has opened up Forge to third-party developers, hoping to create an app economy centered around Forge.
In July, Autodesk hired Sam Ramji as VP of cloud platform. It's a familiar title for Ramji, who preivously worked as Google's VP of cloud platform.
“I want to turn Forge into a Manufacturing cloud,” he said. “When people think of cloud for general use, they think of AWS. When they think of CRM or ERP cloud, they think of Salesforce. Just like that.”
A manufacturing cloud would have an architecture that considers and facilitates manufacturing-specific needs. In his meeting with the press at AU, he further clarified what a “manufacturing cloud” is supposed to be. “When an event happens in the manufacturing process, it should trigger notifications that go to all interested parties and stake holders,” he said.
Forge as a development platform has attraced some on-demand simulation app developers, among others. One example is simulationHub, which offers a series of template-like web-based simulation apps for people with limited simulation software exposure or skills to run fairly complex structural and flow analyses.
In his meeting with the press, Autodesk CEO Andrew Anagnost pointed out, “This looks like something new, but it's not. If you look back to our beginning, AutoCAD's success was due to the fact that it made a great platform for third-party developers. So in a sense, we're going back to where we started.”
The company's flagship product AutoCAD, which still dominates the architecture and manufacturing industries as the standard drawing and drafting package, had an API that let others develop add-ons and plug-ins, fostering a thriving app economy centered around AutoCAD users.
If the company's bets and strategies pay off, Autodesk Forge, similarly, may become the centerpiece of a new app economy.
AU Growth
This year's AU drew more than 11,400 attendees, a 6.5% increase from last year, according to Autodesk press office.
Those who couldn't physically attend the show also had the option to tune in for the live streaming of keynotes and major presentations. This year's keynote on Tuesday Nov 13 racked up 47K views, the company verifies. It includes those who viewed the streaming event live as well as those who viewed the archived version later.
Counting the views received for all industry keynotes in addition to the main keynote, the number rose to 392K views, the company reports.
For More Info
Subscribe to our FREE magazine,
FREE email newsletters or both!Latest News
About the Author

Kenneth Wong is Digital Engineering’s resident blogger and senior editor. Email him at [email protected] or share your thoughts on this article at digitaleng.news/facebook.
Follow DE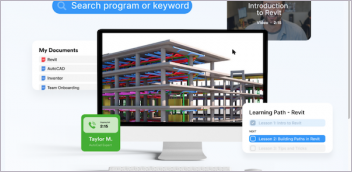

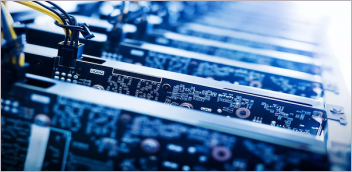
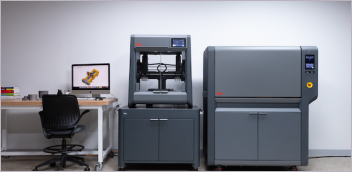