Working with Algorithm-Generated Design: Panelists Respond to Audience Questions

CIMdata’s Keith Meintjes and Advanced Engineering Solutions’ Andreas Vlahinos as panelists for a LIVE roundtable chat on topology optimization (January 31, 2017, 11AM Pacific / 2PM Eastern).
Latest News
February 14, 2017
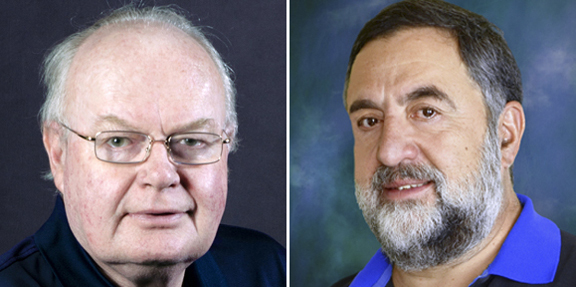
Several weeks ago, CIMdata‘s Keith Meintjes and Advanced Engineering Solutions’ Andreas Vlahinos joined me in a roundtable talk on optimization. At the heart of the discussion is the following question: Would you be willing to put your trust in algorithm-generated designs? (The webcast is now archived online here.)
In the past, engineers relied on their industry knowledge, experience, and aesthetic sensibilities to decide the shape of a product. Today, they have the option to turn to generative design, topology optimization, and other technologies to solicit input from AI-like algorithms. The new approach turns the traditional workflow upside down.
As Solidworks CEO Gian Paolo Bassi put it, “The era of design and validate is about to end. We’re entering the era of optimize and manufacture.” (The comments were made during his keynote speech at the recent Solidworks World 2017 conference in LA. For a full report, read “SWW17: From Design and Validate to Optimize and Manufacture.”)
During the webcast, we conducted two live polls with the audience.
Poll #1: If the software’s algorithm suggests a shape that seems counter-intuitive, would you trust it?
- Yes, I’ll trust it.
- No, I’ll reject it.
Poll #2: Do you feel that topology optimization software is too difficult to learn?
- Yes, it is.
- No, it isn’t.
During the Q&A session of the LIVE webcast, Keith and Andreas received more questions than they could address on the spot. Both panelists were kind enough to offer written replies, which are published below.
Audience comment [on Poll #1]: Wish there was a third answer—I would investigate it.
- Keith’s Answer: There is a third option: Understand why the topology optimization software is giving the result it does.
- Andreas Answer: You are correct. We always investigate the load cases, the units, the manufacturing constraints, and the mesh quality to understand why we get these results.
- Keith’s A: TOSCA in particular can do optimization for fluid flow. But that is on much shakier theoretical ground than structural optimization. It relies much more on heuristics (informed guesses) and brute force computing power.
- Andreas’ A: In addition to TOSCA Fluid all major CAE vendors, national Labs and universities are working on Multi Physics topology optimization
- Keith’s A: The results are always biased. The software is searching for the top of a nearby hill. What they find depends on the starting point and the path taken. Except for the simplest linear problems, there is no single ‘correct’ solution. Many solutions include manufacturing constraints like die direction. But, there are often constraints that cannot be put in the software, so the TopOpt solution needs to be modified. Prof. Shea has an interesting example where they were designing roof trusses for a stadium, but the software suggested structures that intruded on the audience sight lines. So, they had to program additional constraints they had not thought of before.
- Andreas’ A: The major TopOpt codes have manufacturability constraints such as symmetries, extrusion, casting, stamping, radial filling, minimum/maximum member size, etc. When we run the same problem with different codes we get similar results but not identical.
- Keith’s A: Altair has done a great job of making Inspire a single-user tool that requires minimum expertise in CAD and Finite Element Analysis.
- Andreas’ A: I think this is the right direction to embed TopOpt within the CAD environment. We should start with the available design space then use the performance requirements in TopOpt and finally we can start the CAD geometry building.
- Keith’s A: By contrast, these designs are often visually appealing. It is, of course, possible that they may be rejected because they are more expensive to manufacture.
- Andreas’ A: Several times. Some of the reasons are: the manufacturing cost is high, the time to production is high, the material properties for the specific geometry are not validated.
- Keith’s A: Autodesk (Project Dreamcatcher) clearly intends to put variation into the analysis. As Andreas said in his introductory remarks, you can always add robust design as a step after TopOpt.
- Andreas’ A: I have not tried Dreamcatcher but the major TopOpt codes do not include statistical variations. If your performance requirements include quality metrics (i.e. this requirement x needs to have six sigma quality) then you need to perform a DFSS study on your final design.
- Keith’s A: The idea is that TopOpt should give you first-time capable designs that you expect to pass validation testing. It is hard for me to imagine how a design-build-test-break-redesign iterative cycle could be at all effective here.
- Andreas’ A: I couldn’t agree more with Keith’s answer. In addition, if the TopOpt gives you very different shape that your previous design you should reexamine your loading conditions. In that case, an experiment or an IoT process may be necessary to validate your loading conditions.
- Keith’s A: If you have the Altair Hyperworks suite, SolidThinking Inspire is a good start and would be “free” to use with your existing license token pool. This capability is being embedded in CAD tools like CATIA, NX, etc. Andreas mentioned that there is open-source and public-domain software available.
- Andreas’ A: You can find free Applets and Software at http://www.topopt.dtu.dk/ . They work great on desktops, tablets and phones.
- Keith’s A: Probably not, and there is a problem. As Andreas mentioned, the path from TopOpt results to CAD is broken. Once the design is realized in CAD, it is sufficiently different that it has to go through a CAE evaluation step. In addition, the optimization may be based on linear analysis, but you have to assess possible nonlinear issues like fatigue and durability.
- Andreas’ A: Typically we run the topology optimization and the validation steps with different codes (i.e. Genesis. Optistruct or TOSCA for topology and ANSYS, NASTRAN or Abaqus for validation)
- Keith’s A: To do TopOpt effectively requires expertise in CAE, CAD, manufacturing, and product performance requirements. Being an FEA specialist will certainly help if you are part of a team, but the people who do this best seem to simply be acknowledged by their peers as great engineers.
- Andreas’ A: I don’t see it as a cross over, it is complimentary. Every good design engineer should use topology optimization during the design concept generation.
- Keith’s A: Yes. But, there are additional constraints such as allowable (physical) design space and attachment points to other parts which are not explicitly stated in the conventional design process.
- Andreas’ A: Yes Typically is a combination of load cases with the addition of manufacturability constraints.
- Keith’s A: Yes. Take a look at what Jeff Kowalski, CTO of Autodesk, has to say on the topic. https://www.youtube.com/watch?v=uj2XNpvvYvI
- Keith’s A: Not really. It’s more an issue of getting the generative design activity upfront, ahead of where we today do detailed CAD. In many organizations, they do not have anyone assigned to do that job.
- Andreas’ A: Absolutely not. The hardest part is to have the design requirements clearly defined up front. If the requirements are defined the Topology optimization process is fun.
- Andreas’ A: I am very familiar with Gordon. We worked together on an “Advanced Engineering Environments” project funded by DOE. In addition to good ideas and tools you need an internal champion in the management of a large corporation to recognize the vision, adopt it, adapt to achieve it.
To listen to the original webcast, go to /de/optimize.
Subscribe to our FREE magazine,
FREE email newsletters or both!Latest News
About the Author

Kenneth Wong is Digital Engineering’s resident blogger and senior editor. Email him at [email protected] or share your thoughts on this article at digitaleng.news/facebook.
Follow DE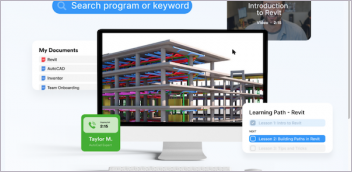

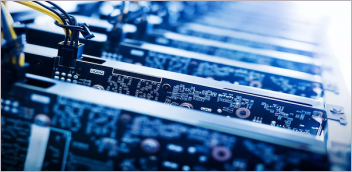
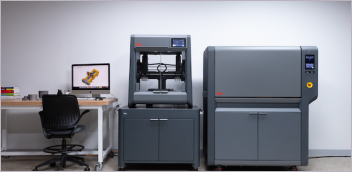