Window Treatment Maker Uses 3D Printing to Cut Design Costs
Company quickly creates new mold patterns, ensure fit and function.
Latest News
November 13, 2011
By DE Editors
UK-based window dressing manufacturer Integra Products is using Z Corporation 3D printing technology to create prototypes in house, reduce costs, eliminate errors, and speed products to market. The Staffordshire company uses physical 3D printed models at every stage of development and across the organization to refine concepts, ensure fit and function, communicate effectively with partners, and quickly create mold patterns.
Integra now prints as many as 25 models overnight, rather than waiting as long as seven days for prototypes from the service bureau. They reduced prototyping costs by 85 to 90 percent compared to the service bureaus fees for SLS prototypes. Creating molds for the rapid creation of silicon molds for sand casting has cut the 10-week development cycle to four weeks.
Our ZPrinter saves us time and money at every step, said Ben White, Integra senior product design engineer. The biggest savings is getting things right before we invest in tooling. Instead of waiting 40 days for tooling and then seeing if we like our samples, our ZPrinter helps us ensure, before the fact, that our products are going to work, fit with adjacent components, and look great. That can eliminate errors that would otherwise cost us thousands of dollars.
In addition to saving time, money and errors during development, 3D printing has uncovered ways to cut costs on actual product materials. Through extensive prototype testing, the company has reduced the weight of each curtain hook by .3 grams, saving 500 kg of plastic per year.
For more information, visit Z Corporation.
Sources: Press materials received from the company and additional information gleaned from the company’s website.
Subscribe to our FREE magazine,
FREE email newsletters or both!Latest News
About the Author

DE’s editors contribute news and new product announcements to Digital Engineering.
Press releases may be sent to them via [email protected].
Related Topics
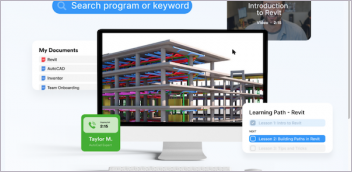

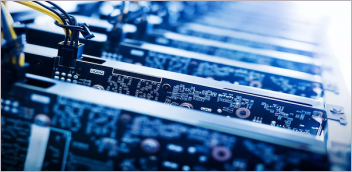
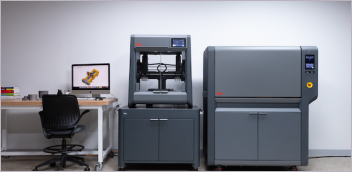