Unilever Reduces Prototyping Production Times With 3D Printing
Latest News
January 21, 2015
Unilever, a consumer goods and food company, has reduced lead times for prototype parts by using Stratasys technology. In addition to using 3D printers, its Italian division is using 3D-printed injection molds for parts and consumer tests.
The company is using a Stratasys Objet500 Connex 3D production system for its household care and laundry goods division, with a run of around 50 units for a variety of parts. For making parts, it uses ABS (acrylonitrile butadiene styrene).
Unilever is also producing thermoforming mold prototypes with the Fortus 360mc production system, which is based on FDM (fused deposition modeling) technology. These prototypes have flexible strength that can endure functional testing.
“[With] Stratasys 3D printing technology, we can design and print a variety of injection molds for different parts that can undergo functional and consumer testing, all on the same day,” said Stefano Cademartiri, research & development, CAD and Prototyping Specialist at Unilever. “Before, we would have to wait several weeks to receive prototype parts using our traditional tooling process; not only would this lengthen lead times, it would also increase costs if iterations were required. With 3D printing we’re now able to apply design iterations to the mold within a matter of hours, enabling us to produce prototype parts in final materials such as polypropylene, 40% faster than before.”
For more information, visit Stratasys and Unilever.
Sources: Press materials received from the company and additional information gleaned from the company’s website.
Subscribe to our FREE magazine,
FREE email newsletters or both!Latest News
About the Author

DE’s editors contribute news and new product announcements to Digital Engineering.
Press releases may be sent to them via [email protected].
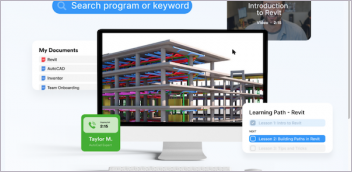

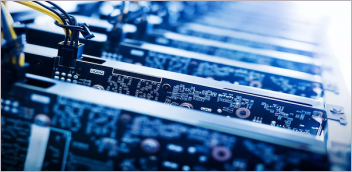
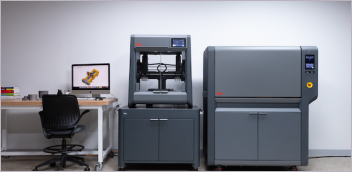