
After inheriting details of the “as manufactured” components from the press shop, SYSWELD simulates the entire assembly and welding process chain in the body shop step by step. Composite image courtesy of ESI Group.
Latest News
September 27, 2017
ESI Group has released the 2017 edition of its SYSWELD FEA (finite element analysis) multiphysics simulation solution for assembly, welding and heat treatment. This latest release, ESI says, sees enhanced welding and heat treatment simulation capabilities as well as new features for simulating assemblies in body shops.

ESI describes SYSWELD as offering capabilities that enable manufacturers in industries such as ground transportation, aerospace, heavy industry and marine to reduce product development costs and time to market as well as ensure process automation and optimization. It’s used to simulate thermal joining (arc, electron beam, laser, friction stir and spot welding) and heat treatment (carburizing/carburization, carbonitriding and quenching). It predicts material characteristics, residual stresses and distortions of structures. By accounting for all relevant manufacturing effects and enabling the transport of simulation results from one manufacturing step to the next, SYSWELD delivers a predictive end-to-end solution for the manufacturing of welded and assembled industrial parts, ESI says.

SYSWELD 2017’s welding and heat treatment simulation capabilities have been enhanced to help to secure process feasibility and security, to control material characteristics and residual stresses, to keep distortion within specified tolerances and to improve the performance of the product, according to the company. New meshing capabilities are said to “strongly reduce the time needed to create dedicated meshes for weld and heat treatment.”
To better support multi-pass welding, SYSWELD 2017 provides automatic control of the interpass temperature between each weld. This, ESI says, ensures better component integrity with direct control of phase proportion and stresses.

Version 2017 also supports new manufacturing processes, including spot welding using spacers, friction stir welding and carbonitriding. New functionality allows the smart transfer of dedicated data from one simulation discipline to another, so that complete manufacturing processes can be simulated and used as input for performance. Of note to current SYSWELD users are new core technologies to support the treatment of very large models and to minimize the output file size.

SYSWELD 2017’s enhancements for body shops enable the modeling of the full stamp-welding-assembly simulation chain for fast distortion engineering in the context of car body manufacturing. Engineers can now control the dimensional inaccuracies of hot- and cold-joined assemblies by accounting for mechanical load effects during successive assembly processes as well as heat effects induced by welding. This approach, according to the company, means that engineers can virtually manufacture, assemble and test physically realistic virtual components before manufacturing hardware prototypes. This can help automotive manufacturers and suppliers reduce the cost and delays of manufacturing planning, tryout and process validation, the company adds.
For the shipbuilding industry, SYSWELD 2017 provides automation and optimization to reduce the cost and time required to prevent or mitigate weld-induced distortions. New functionality reportedly ensures distortion control for large welded assemblies with thick plates and multi-pass welds.

Aimed at shop floor production, the software provides a streamlined and intuitive interface, dedicated automatic meshing functionalities and easy model setup that can help designers and engineers optimize a weld sequence plan. This can help manufacturing engineers identify the welds primarily responsible for distortion quickly, and it provides the ability to investigate the effects of changes to a variety of process parameters, including sequencing, clamping and pre-heating, according to ESI.
For more information about SYSWELD 2017, click here.
Download the SYSWELD brochure.
Download the technical paper “Welding Characteristics and Modeling of Lithium-Polymer Battery for Electric Vehicles.”
See why DE’s Editors selected SYSWELD 2017 as their Pick of the Week.
Sources: Press materials received from the company and additional information gleaned from the company’s website.
Subscribe to our FREE magazine,
FREE email newsletters or both!Latest News
About the Author

Anthony J. Lockwood is Digital Engineering’s founding editor. He is now retired. Contact him via [email protected].
Follow DE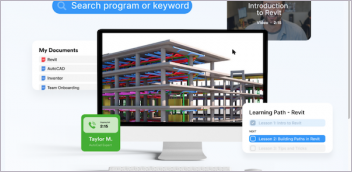

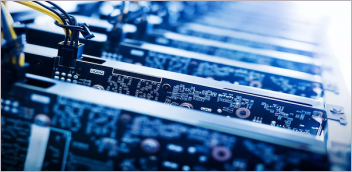
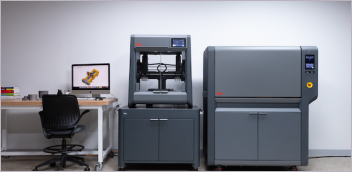