Sustainable Designs for Manufacture and Assembly
DFMA 2009 helps engineers assess a product's environmental impact while simplifying design and holding down costs.
Latest News
April 1, 2009
By DE Editors
![]() DFMA 2009 from Boothroyd Dewhurst includes new Design for Environment (DFE) functionality that lets engineering teams check the environmental impact of their material choices while they are in the concept stage of design. |
Boothroyd Dewhurst, Inc. (Wakefield, RI) has added new design-for-environment tools to DFMA 2009, the latest version of its Design for Manufacture and Assembly (DFMA) software suite. The new Design for Environment (DFE) functionality enables engineers to check the environmental impact of their material choices, pick an end-of-life scenario, and meet compliance issues while they are in the concept stage of design.
DFMA 2009 provides a quantitative, multidisciplinary approach to identifying and controlling design, manufacturing, and assembly costs, according to Boothroyd Dewhurst. It guides engineers through a product design simplification process that helps identify major cost drivers associated with a wide range of part manufacture and finishing choices. Engineers leverage this input to develop products with fewer parts, making the end product more economical to manufacture and easier to assemble.
The new DFE functionality extends the DFMA vision to environmental design considerations. The goal of the new DFE functionality is to enable product development teams to make quick, basic, and informed decisions about a product’s environmental impact during the concept phase of product development while simultaneously leverage DFMA to reduce unnecessary costs. This combination enables manufacturers to identify and rate materials for their compliance to standards such as WEEE and RoHS regarding toxicity and end-of-life destinations.
Engineers use DFE to make informed green decisions by selecting and analyzing materials from a library that’s part of the DFM Concurrent Costing database. This library gives designers a comprehensive understanding of the costs and materials used to manufacture parts through such means as turret pressworking, laser and plasma cutting, sheet metal stamping with a variety of dies, machining, structural foam molding, plastic extrusion, injection molding, thermoforming, blow molding, cold and hot die casting, hot forging, powder metal processing, sand casting, investment casting, and metal injection molding.
![]() Materials selection in DFMA 2009. |
The library, which is user-extensible, now categorizes materials as “preferred,” “non-preferred,” and “avoid.” The latter category indicates materials on the Environmental Protection Agency’s banned substances list and─for European versions─materials that will prevent RoHS compliance. Once an engineer selects a material, DFE determines the amount and weight of the material used in the product and then estimates and designates the proportions of product for different end-of-life destinations, including reuse, recycling, landfill, and incineration.
“Manufacturers are increasingly aware that addressing the environmental impact of their products will soon be a requirement for entry into major markets,” said Dr. Winston Knight, senior vice president at Boothroyd Dewhurst, in a press statement announcing DFMA 2009. “Designers can now select the best materials for greener products, even as they innovate with DFMA to build more performance into efficient, leaner designs.”
Additional enhancements in DFMA 2009 include the ability to estimate the cost of machining a batch of parts in a dedicated machining cell when processing on a single machine is not possible─for example, milling and grinding operations. This new capability automatically combines individual processes, times, and costs within the cell, and users can choose and calculate various cell arrangement scenarios for maximum efficiency. The software can help uncover hidden costs of labor and machine idleness and can assess the time needed to complete entire manufacturing runs at different production volumes.
![]() Design for Assembly in DFMA from Boothroyd Dewhurst. |
The updated DFM Concurrent Costing component in DFMA 2009 now offers two types of machined/cut-from-stock analyses: a traditional full analysis and a new quick estimate. The new quick estimate approximates part cost by allowing users to enter the volume of the finished part, the number of part features produced by various machining operations, and the surface area of those features. It then automatically selects the machine tools and estimates cutting-tool movements.
Miscellaneous enhancements include the ability to read SolidWorks geometry directly. Additionally, engineers can now install their own cost model for a manufacturing process into the DFM Concurrent Costing software.
DFMA 2009 operates in Windows environments. For complete details on DFMA 2009 with Design for Environment functionality, visit the Boothroyd Dewhurst website.
For more information on Design for Environment, click here.
Click here for more information the new DFMA machining cell capabilities.
Details on DFMA 2009’s quick estimates functionality are available here.
Sign up to download a webinar on DFMA 2009 and related topics.
The 2009 International Forum on Design for Manufacture and Assembly will be held June 9-10 in Providence, Rhode Island. Click here to learn more.
Read why DE’s editors chose DFMA 2009 with Design for Environment tools as its Pick of the Week.
Subscribe to our FREE magazine,
FREE email newsletters or both!Latest News
About the Author

DE’s editors contribute news and new product announcements to Digital Engineering.
Press releases may be sent to them via [email protected].
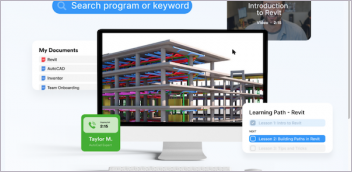

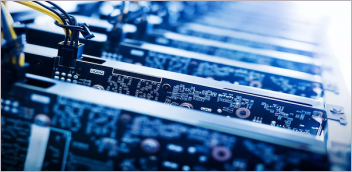
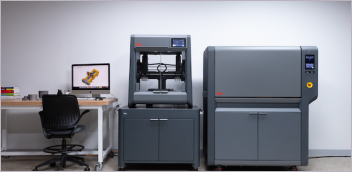