The State of Electronic 3D Printing
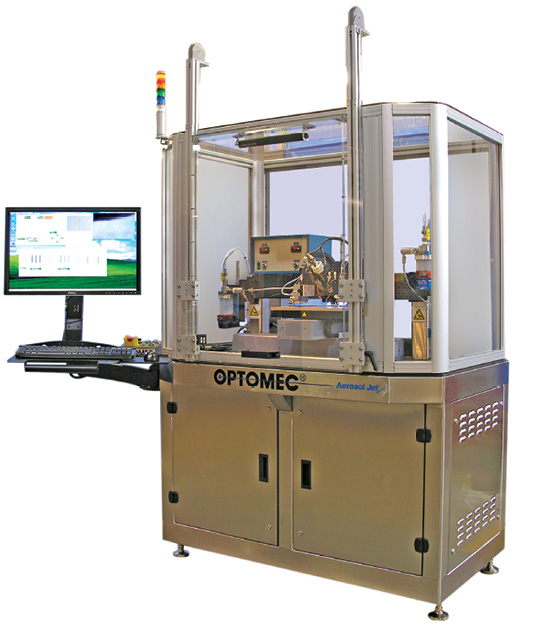
Optomec uses Aerosol Jet technology for electronics 3D printing. Image courtesy of Optomec.
Latest News
June 1, 2017
3D electronics printing is still an emerging technology, but production systems are now in place in a few industries, and these innovative additive manufacturing solutions appear poised for more growth.
According to “Opportunities for 3D Printing in the Electronics Industry” from SmarTech Publishing, the technology began being mainstreamed in the electronics industry in 2015 after being used for years in research and development. Initial applications include direct manufacturing of antennas, interconnects, printed circuit boards, sensors and other devices. 3D electronics printing reportedly will generate $428 million in revenues by 2022, and potentially reach $2.8 billion by 2025.
“We are seeing a surge in interest in the last 12 months,” says Martin Hedges, founder and managing director at Neotech AMT. “A lot of industries are waking up to the potential of 3D printed electronics (PE). Another factor is the convergence of classical 3D printing with 3D PE. This will lead to fully-automated, digitally-driven manufacturing.”
“About four years ago we started getting interest from commercial companies who were just starting to look at printed electronics for next-generation challenges they were seeing,” says Mike O’Reilly, director of product management for Optomec’s Aerosol Jet product line. “They couldn’t figure out how to address them using traditional manufacturing techniques. We’ve seen systems go into place—first as pilots and then full production—in a few different markets.”
Multilayer printed circuit boards (PCBs) prototyping is an initial driver of electronic 3D printing. Traditional printed electronics require flat surfaces. What 3D printed electronics can do is allow the creation of electronics on 3D surfaces and in variable shapes and configurations. So far, companies in the field are printing electronics components (like PCBs and antennas), as well as embedding electronics into other objects (3D printed objects and traditionally manufactured items). In this case, the circuitry can be printed on an existing object of almost any shape.
Conformal antennas are a common example. Being able to print these antennas can reduce production time and allow companies to create antenna designs that weren’t previously possible.
The market is currently dominated by a group of specialist companies, including Optomec, Voxel8, Nano Dimension (that specializes in PCB development) and others.
Production Printing Systems Emerge
3D printed electronics are already being used for end products in consumer electronics, semiconductor packaging, Internet of Things and other applications. Optomec’s Aerosol Jet solution is in mass production at the LITE-ON Mobile Mechanical SBC factory in China, printing conformal electronics on consumer devices—a project deployed in conjunction with Neotech.
“LITE-ON won a large contract and couldn’t figure out how to fulfill it,” Optomec’s O’Reilly says. “That was our first major commercial win in the consumer electronics space. They are printing antennas inside of smartphones.”

Optomec has also demonstrated its technology for printing capacitive filling sensors and a circuit on a molded tank, as well as printing heater elements on glass. Its technology also can create single-layer circuit boards that emulate multi-layer circuits by building interconnects at circuit crossover points. Materials also can be switched or blended during printing.
Nano Dimension has targeted its DragonFly 2020 3D printer at rapid prototyping for circuit boards. Voxel8 has provided solutions for PCB and flex circuit manufacturing, as well as 3D phased array and antenna printing. The company’s printer system uses a two-nozzle arrangement to print both polylactic acid filament and conductive silver ink to create embedded electronics.
O’Reilly says another emerging market is for advanced packaging, including printing up the side walls of stacked chips to printing wafer-level fan-out technology. “Another way to describe it is being able to mount components onto 3D surfaces and wire those components to get a functional circuit,” O’Reilly says. “In the automotive world, for example, if I can print a circuit on a plastic substrate and use that as a connection point for interfacing into various electronic components, I can make them lighter and cheaper—and more functional.”
There is increasing interest in the technology in the automotive industry, as well as for IoT applications, and some emerging interest for medical devices. Moving forward, 3D printed electronics could allow designers to have more flexibility in how they stack circuits, integrate circuitry into products and possibly enable on-shoring of more electronics manufacturing once the technology is better able to scale.
“There are a lot of other applications in the prototyping/development stage,” Hedges says. “I think realistically it is going to take several years to get parts into production for automotive due to industry requirements. Other markets such as white goods, consumer goods or industrial segments could go faster.”
The effect of the IoT on printed electronics is still unclear, although there is some interest, particularly in printing sensors. Optomec, for instance, is printing sensors on turbines for one customer. “They are printing sensors up and down the blades to detect stress or strain. They can do real-time health monitoring and just-in-time servicing of the product,” O’Reilly says. “They can constantly interrogate those blades and validate that they are still functioning as specified without having to take the system offline.”
Luxexcel specializes in 3D printing optical lenses for eyeglasses, but has also tested out printed electronic circuitry to create smart glasses and other products. With 3D printed electronics in the lens, manufacturers could create embedded polarization filters, embed UV or eye-tracking sensors and create eye movement-based control systems or electrically switched sunglasses. There are also augmented reality applications for such lenses.
“You can put all kinds of sensors, indicators or LCD screens in the lens,” says Guido Groet, chief commercial officer at Luxexcel. “You have to make sure the electronics are not in the field of view, and that they don’t create optical aberrations.”
Printing the electronics in the lens can make that integration easier, although not every component can be printed. “A lot of sensors have odd materials in them that you can’t print, and there are other components that really can’t be printed,” Groet says.
A pair of projects in Europe are also pushing the envelope. The Eureka PENTA Cluster has a project under way to develop hybrid 3D manufacturing methods that combine printing of polymers with assembly and integration for electronic parts. The MANUNET Project AMPECS will develop processes for printing electronics in and on ceramic substrates.
According to Neotech’s Hedges, the value of these processes would be in low- to medium-volume manufacturing of customized/personalized products, or where end users are trying to iterate new products more quickly. Localized manufacturing could also be enabled this way.
“At the moment, it is not clear where the cutoff point will be. I expect it will be different for different product types. The slowest part of the process will be their structural build by 3D printing,” Hedges says.
Growing the Market for 3D Printed Electronics
Advancements in materials will help expand the use of 3D printed electronics. Optomec, for example, announced improvements in it ability to print and post-process copper and copper/nickel inks for its aerosol jet systems. The company offers print recipes and special hardware to shield the materials during printing and curing. Other vendors are finding ways to provide more functional materials as well, including stretchable materials.
“We’ve seen advances in noble metals like silver, copper and nickel, as well as some work in palladium and gold,” O’Reilly says. “Customers want to get lower-temperature materials like polycarbonate, which has a strong tensile strength but melts at 120°C. There’s work being done to develop materials that give you the electrical performance you need, will adhere to the surface of the substrates and pass environmental tests.”
There are also conductive filament materials that can embed some level of functionality into the underlying part. However, they may have limited application. “They have lower performance than commercially available inks/pastes,” Hedges says. “These materials are already quite mature and are simpler to interconnect to switched multimegabit data service/external systems.”
“There’s room for everything, and I don’t think one approach will win out over another,” O’Reilly says. “It depends on the application. Printing plastics and adding conductive filament along the way is just too slow for production right now. But for low-volume applications, that could work.”
Subscribe to our FREE magazine,
FREE email newsletters or both!Latest News
About the Author

Brian Albright is the editorial director of Digital Engineering. Contact him at [email protected].
Follow DE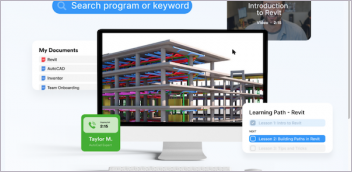

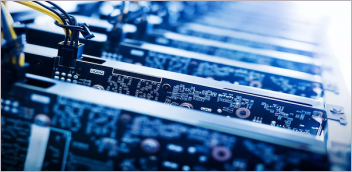
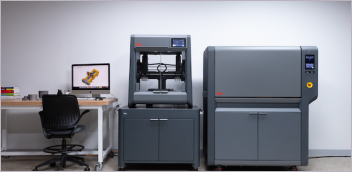