Stable Testing for Aerospace

Latest News
March 1, 2015
Just a few days before the maiden flight of the new European Space Agency (ESA) Vega launcher, Marc Pitz, Testing, and Product Engineer Marc Rigal at SABCA noted that they did not know if the electromechanical thrust vector actuation system from SABCA, which would be used to steer the rocket ship that took off from the French Guyana Space Center in Kourou, would perform according to plan. A few days later, the first qualification flight of the Vega launch vehicle proved to be a success.
“The outcome of the Vega program is extremely important for us,” says Pitz. “Vega will mark our future.”
SABCA is one of the main aerospace companies in Belgium. It was founded in 1920 and is based in Haren, near Brussels, and Charleroi. Besides being a subcontractor for different aircraft manufacturers, such as Dassault Aviation and Airbus, SABCA just delivered its 100th Airbus A380 T-Shape: a large metallic structural assembly that carries high fuselage loads between the main wheel wells of the aircraft. The company also builds servo-actuators for the Ariane 5 launcher and the Interstage 0/1 skirt and the thrust vectoring systems for the four stages of the new Vega launcher.
This new Vega launcher has been developed by the ESA during the last nine years. It will be able to bring a 1.5-ton payload into low earth orbit. The technology on the Ariane 5 program goes back as far as the early 1970s, and the servo-actuators that were used to direct the rocket thrust and steer the rocket ship are still electrohydraulic systems: GAT (Groupe d’Activation Tuyère or Nozzle Activation Unit) and GAM (Groupe d’Activation Moteur or Motor Activation Unit).
For the new Vega launcher, SABCA developed a fully electrical thrust vector actuation system (electromechanical actuators, control, power electronics and the associated software). This system is based on a proprietary SABCA microprocessor hardened against space radiation. It will operate in a vacuum at very low temperatures and have to withstand the heavy shocks generated by the various stages of separation of the rocket.
Due to significant constraints, the thrust vector actuation system undergoes a very strict and severe qualification test program during development. But each subassembly also undergoes a set of predefined lower and shorter tests on the shaker just before rocket assembly.
Appreciating Versatility
Five years ago, SABCA decided to replace and update its first system, and now uses LMS Test.Lab software in combination with LMS SCADAS hardware for closed loop shaker control and data acquisition from Siemens PLM (product lifecycle management) Software.
“We evaluated different suppliers, and the solutions of Siemens PLM Software offered far more possibilities and flexibility, mainly because of their modal capability,” says Pitz.
Two years ago, the test environment was further enhanced with a brand new 160 kilo Newton (kN) shaker, referred to by Pitz as “our big elephant.”
“We use the same test setup for both qualification and production testing of the servo-actuators,” says Pitz. “This built-in flexibility is considered a key advantage of the Siemens PLM Software testing solutions.
“Ease of use is very important to us because different engineers are using the system, and not everybody is a test software expert or can invest vast amounts of time studying the tools. Production engineers are no vibration experts, but once the configuration is set, they push the button and the test is done. These time savings are important for us.”
Providing Accurate Control
The SABCA engineering team performed thermal tests and basic vibration tests on the actuators, mainly of the sinusoidal and random type.
“During the qualification tests, the components are put under severe stress, up to 22.5 g in sine mode and 20 g in random mode,” says Rigal. “During production, test levels are topped off at 12 g in random mode. Production tests are mainly focused on random mode.”
“A vibration test on a hydro-mechanical actuator typically takes half a day,” says Pitz. “Since it takes two actuators to steer the thrust of an engine, tests are performed on two hydro-mechanical actuators consecutively, as a twin configuration. So testing one set takes a day, plus two days for the thermal test.”
“Starting from the primary parts, it takes three to four weeks to have a hydro-mechanical actuator ready,” says Rigal. “Producing an electromechanical actuator takes less than a day, but far more time to test. The test cycle takes more time than the assembly cycle.”
Controlling risks during these tests is important because safety is a critical consideration.
“Testing actuators means that the level on the hydraulic pump needs to be limited to a max of 250 g, especially when reaching resonances,” says Rigal. “We control this level accurately because harmonic and peak estimators are computed in real time by the software.”
Integrating Testing and Simulation
“We perform about 15 to 20 vibration tests per month,” says Rigal. “We’ve used the system for five years, and during that time we’ve never experienced any unexpected or unstable behavior of the system.”
The development of the Ariane 5 launcher predates virtual testing and testing models. Although numerous tests were performed and data was gathered, no truly correlated virtual test model of the hydro-mechanical actuator was ever built. Since the beginning of the Ariane 5 program, the technology of servo-actuators has undergone a major change.
The actuators on the new Vega are electromechanical, which follows the recent trend in the industry. Testing these electromechanical actuators means entering unchartered territory.
“This electromechanical character complicates vibration testing in a certain way, because besides mechanics, we also have to test the electronic components on a small board inside the electronic box,” says Pitz. “Resonance frequencies are a lot higher with electronic components. Exposure of these components to space radiation also means that we have to perform electromagnetic compatibility tests.”
It is believed that testing and simulation will be further integrated in the future. “We believe that simulating testing using correlated models will be required in the future in order to better predict the vibration behavior during the qualification test,” says Pitz.
The use of the virtual shaker technique will increase confidence in the test and enhance the notching profile definition.
“Mechatronic actuators are quite a new product, including for us,” says Pitz. “Testing has become more detailed and delicate. For the moment, the mechanical and electronic parts are still separated, but in the near future, the electronics will be integrated on the mechanical parts, thus actuators will become truly integrated mechatronic systems.”
More Info
Subscribe to our FREE magazine,
FREE email newsletters or both!Latest News
About the Author

DE’s editors contribute news and new product announcements to Digital Engineering.
Press releases may be sent to them via [email protected].
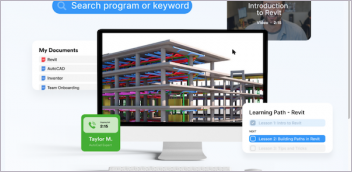

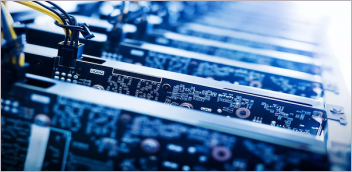
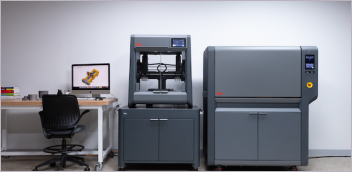