Siemens PLM Software Releases Four D-Cubed Components
Version 42.0 of the 3D Dimensional Constraint Manager, Collision Detection Manager, Hidden Line manager, and Assembly Engineering Manager released.
Latest News
July 6, 2010
By DE Editors
Siemens PLM Software has released new versions of the 3D Dimensional Constraint Manager (3D DCM), Collision Detection Manager (CDM), Hidden Line manager (HLM), and Assembly Engineering Manager (AEM).
The D-Cubed 3D DCM is a software component that positions parts in assemblies, simulates their kinematic motion, and parametrically controls the configuration of 3D sketches and the shape of parts. New enhancements specific to version 42.0 include:
- Full evaluation / incremental evaluation query. 3D DCM offers the application two distinct evaluation functions, a full evaluation and a much more rapid incremental evaluation. The full evaluation analyzes a previously unsolved scheme of geometries, dimensions and constraints, identifies a solution procedure and solves the system of equations required to correctly position the geometry. An incremental evaluation allows a previously solved model to be re-solved much more quickly when only the values of dimensions or the positions of geometries are changed.
- Model satisfied query. Another new status query to be added in version 42 is the ability to inquire of the 3D DCM whether geometries in the model are currently in a position to satisfy the constraints and dimensions without having to perform a full evaluation. This can help developers working on integrations to check that constraints have been added to the 3D DCM in the manner intended.
The latest release of the D-Cubed CDM, a software component that accurately and rapidly detects collisions and computes clearances, includes the following enhancements specific to version 42.0:
- Collision computations. The CDM can be given one or more parts and a direction, and compute whether a collision would occur with the remainder of the model if the parts moved in the specified direction. The CDM’s optimized “collision along a path” algorithm is used by CAM and CMM (coordinate measuring machine) applications when simulating the motion of tools and probes relative to the parts being machined or measured.
- In this release, intersections can be detected between wire geometries, that is geometries with length, but no width or depth. They are also now detected between combinations of wire geometries and faceted parts.
- Clearance computations. As well as detecting collisions, the CDM can also compute clearance, sometimes known as closest approach. This release extends support to include computations between a position and a part, including the closest approach to the surface of a part when the position is inside the part.
The latest release of the D-Cubed AEM, a software component that the company says provides a more realistic and productive assembly environment, includes:
- Initial contacts enhancement. The AEM uses two different types of constraints. Firstly there are the explicit assembly constraints that the user has added to the 3D DCM to define the relative position of parts or the joints in a mechanism. Secondly there are the contact constraints that the AEM applies automatically when parts collide during a drag operation or simulation. Before the first motion step in an operation, there may be parts in the model that are in a touching position, but which don’t have explicit 3D DCM constraints applied. The AEM will analyze the model and apply a set of initial contacts between geometries in these touching parts. In version 42 this algorithm has been improved. As a consequence, the first and subsequent motion steps are more efficient and the user will notice that certain models respond faster when first dragged.
- In version 42, the algorithms that solve contact constraints close to the boundaries between parametric edges and faces have been improved, resulting in smoother and faster transitions of contacts across the boundaries of these geometries, according to Siemens.
The latest release of the D-Cubed HLM, a software component that computes hidden line views, includes:
- Hidden line computations on “long” curves. Some parametric curves can be thought of as computationally “long,” meaning that in order to be processed by the HLM’s hidden line algorithms they have to be divided into numerous segments. In this release, a new method of segmenting the curves has been implemented that the company says reduces the number of segments involved in the computations, in turn reducing the number of cycles through the relevant algorithms.
For more information, visit Siemens.
Sources: Press materials received from the company and additional information gleaned from the company’s website.
Subscribe to our FREE magazine,
FREE email newsletters or both!Latest News
About the Author

DE’s editors contribute news and new product announcements to Digital Engineering.
Press releases may be sent to them via [email protected].
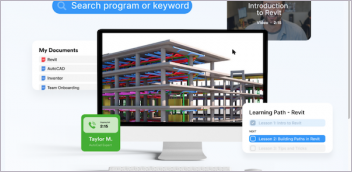

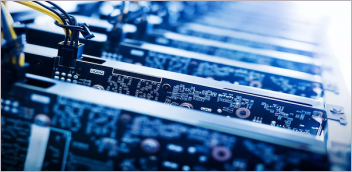
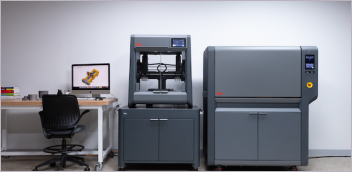