Siemens 3D Prints Power Turbine Blades

Siemens testete erstmals vollständig mit Additive Manufacturing (AM) gefertigte Gasturbinenschaufeln nach konventionellem sowie neuem Schaufeldesign unter Volllast in einer Gasturbine. Siemens finished its first full load engine tests for conventional and completely new designed gas turbine blades produced using Additive Manufacturing technology.
Latest News
June 12, 2017
Siemens has successfully tested 3D-printed metal turbine blades that could be used in production for power-generation. The blades survived testing under full-load engine conditions.
The blades can survive temperatures above 1,250°C (2,282°F) and extremely high pressures.

“To have this rotating part running is a breakthrough because it is submitted to these extreme loading ... It rotates with 13,600 rotations-per-minute, which means it is the most highly loaded component in the whole gas turbine. So this blade that weighs 180 grams will weigh 11 tons while rotating with this speed,” Jenny Nilsson, team leader for additive manufacturing at Siemens, told Reuters.
The blades were printed by Material Solutions, a company Siemens acquired last year, using nickel superalloy powder. They were tested on a 13-megawatt SGT-400-type industrial gas turbine.
The tests were conducted at the Siemens testing facility in the industrial gas turbine factory in Lincoln, UK.
Siemens claims the process will reduce the design-to-test time from years to months. The blades went from component design to testing in just 18 months, including the development of new material, as well as simulation and quality control.
“When you apply casting procedures it will probably take one to one-and-a-half years to provide you with these blades because of their long lead time for tooling. And by applying additive manufacturing, we could significantly shorten lead time by down to three months,” Christoph Haberland, Siemens Manufacturing Engineering, told Reuters.
Because the blades were built via additive manufacturing, Siemens was also able to produce blades with a revised and improved internal cooling geometry.
You can learn more about the tests in the Reuters video below.
Source: Reuters
Subscribe to our FREE magazine,
FREE email newsletters or both!Latest News
About the Author

Brian Albright is the editorial director of Digital Engineering. Contact him at [email protected].
Follow DE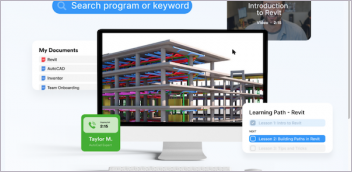

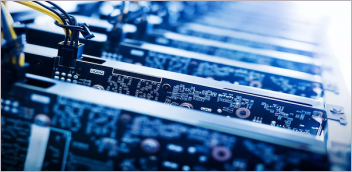
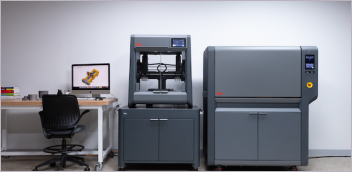